Safety and Health Program Management Guidelines
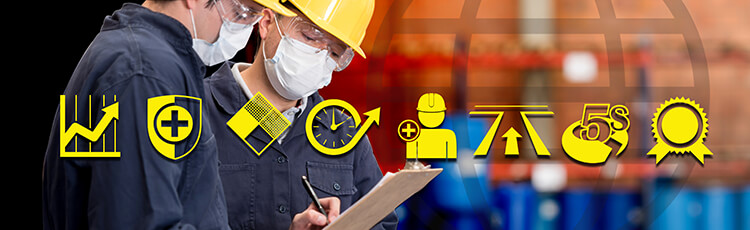
OSHA has updated Safety and Health Program Management Guidelines in order to provide employers and workers with a sound, flexible framework for addressing safety issues in the workplace.
Originally published in 1989, the new guidelines build on a previous version, as well as best practices under two OSHA programs: the Voluntary Protection Program and the Safety and Health Achievement Recognition Program. The guidelines also align with industry and international initiatives, such as ANSI/AIHA Z10 and OHSAS 18001.
What's New in the Guidelines
- A proactive approach to finding and fixing hazards before they cause injury, illness or death
- Improved safety and health in all types of workplaces
- Help for small and medium-sized businesses to effectively protect their workers
- Increase worker involvement, so all employees have a voice in workplace safety and health
- Better communication and coordination on a multi-employer worksite
Seven Core Elements
The Safety and Health Program Management Guidelines are based on seven core elements. Each guideline section describes a core program element, followed by several action items; these action items list steps that employers and workers can take to establish, implement, maintain, and improve their safety and health programs. The seven core elements are:
1. Management Leadership
- Top management demonstrates its commitment to continuous improvement in safety and health, communicates that commitment to workers, and sets program expectations and responsibilities.
- Managers at all levels make safety and health a core organizational value, establish goals and objectives, provide adequate resources and support for the program, and set a good example.
2. Worker Appreciation
- Workers and their representatives are involved in all aspects of the program-including setting goals, identifying and reporting hazards, investigating incidents, and tracking progress
- All workers, including contractors and temporary workers, understand their roles and responsibilities under the program and what they need to do to effectively carry them out
- Workers are encouraged and have means to communicate openly with management and to report safety and health concerns without fear of retaliation
- Any potential barriers or obstacles to worker participation in the program (for example, language, lack of information, or disincentives) are removed or addressed
3. Hazard Identification & Assessment
- Procedures are put in place to continually identify workplace hazards and evaluate risks
- An initial assessment of existing hazards and control measures is followed by periodic inspections and reassessments to identify new hazards
4. Hazard Prevention & Control
- Employers and workers cooperate to identify and select options for eliminating, preventing, or controlling workplace hazards
- Workers develop a plan that ensures controls are implemented, interim protection is provided, progress is tracked, and the effectiveness of controls is verified
5. Education & Training
- All workers are trained to understand how the program works and how to carry out the responsibilities assigned to them under the program
- All workers are trained to recognize workplace hazards and to understand the control measures that have been implemented
6. Program Evaluation & Improvement
- Control measures are periodically evaluated for effectiveness
- Processes are established to monitor program performance, verify program implementation, identify program deficiencies and opportunities for improvement, and take actions necessary to improve the program and overall safety and health performance
7. Coordination & Communication on Multi Employer Worksites
- The host employer and all contract employers coordinate on work planning and scheduling to identify and resolve any conflicts that could impact safety or health
- Workers from both the host site and contract employer are informed about the hazards present at the worksite and the hazards that a contract employer's work may create on site
Continuous Improvement
The concept of continuous improvement is key to the guidelines. The idea is to begin with a basic program and simple goals and grow from there. By focusing on achieving goals, monitoring performance, and evaluating outcomes, workplaces can achieve higher levels of safety and health achievement.
According to OSHA, if these guidelines are implemented, the renewed or enhanced commitment to safety and health and the cooperative atmosphere between management and workers have been linked to:
- Improvements in product, process, and service quality
- Better workplace morale
- Improved recruitment and retention
- A more favorable image and reputation (among customers, suppliers, and the community)
Public Comments
OSHA is seeking public comment on an updated version of its voluntary Safety and Health Program Management Guidelines (OSHA-2015-0018). Read OSHA's Safety and Health Program Management Guidelines and submit your public comment here.
Related Resources
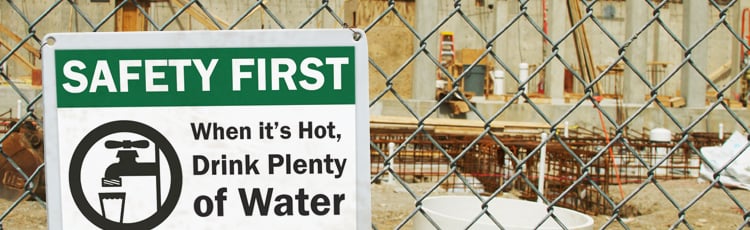
Safety Campaigns Heat up for Summer
OSHA's Heat Illness Prevention Campaign educates employers and workers on the dangers of working in high ...
Read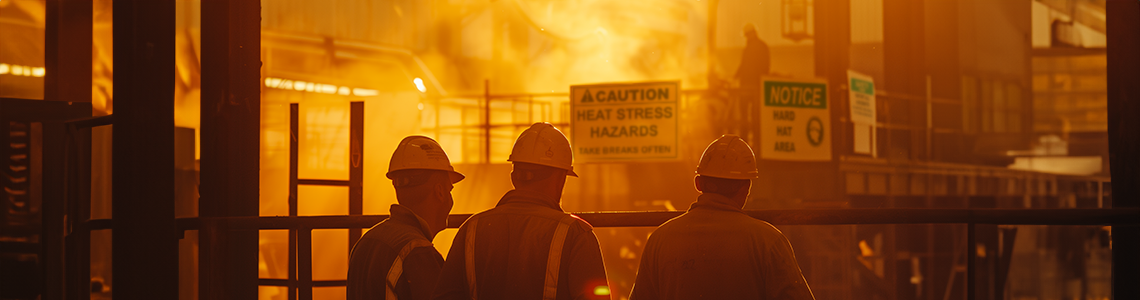
OSHA Cranks Up Heat Safety Standards
In compliance with the Small Business Regulatory Enforcement Fairness Act (SBREFA), OSHA assembled an SBAR ...
Read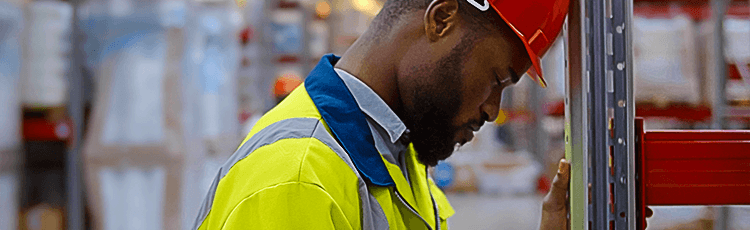
Mental Health is Worker Health: 6 Tips to Prevent Employee Burnout
88% of workers experience some burnout, with 60% reporting high levels of burnout* One-fifth will miss six or ...
Read