Ways to Save Money in Maintenance

"If you fail to plan, you are planning to fail" is a hard-truth quote from Benjamin Franklin, a founding father of the United States.
When it comes to maintenance, a lot of workplaces want to save money and think the best option is to defer it. That could not be more wrong a thing to do, especially as the costs of downtime are ever-increasing. There are common thoughts and reactions to maintenance to make it safer and more efficient, and in the long run, they are also the most cost-effective approaches to maintenance.
Running into Trouble
"If you keep running machines and equipment continuously without maintenance, it will cause huge problems later on," said Lonnie Roberts, a production manager in Pennsylvania.
When maintenance isn't on some sort of a schedule, it creates an even larger amount of work down the line. It also postpones urgent repairs, which then creates a domino effect on labor, as the crew won't have enough time to get it all done. Work stops also can occur because a part is missing, or the team doesn't know how to approach the problem.
According to Reliable Plant magazine, only 27 percent of respondents in a manufacturing maintenance survey said they use Total Planned Maintenance. This lack of implementation and planning can result in faulty equipment, poor maintenance, and inefficiencies that contribute to weighty operational, labor, and financial losses:
- Unexpected breakdowns: Downtime for equipment repairs, which costs in lost production, labor, and parts.
- Set-up and adjustments: Operating conditions such as changeovers and other production changes.
- Stops: Some stops of as long as 10 minutes can be difficult to track if there isn't a computerized maintenance management information system. Stoppages of any kind can hinder production goals across the board.
- Speed: Slowdowns can often be just as bad as a stop.
- Quality: If equipment is off-spec or malfunctioning, it can affect output or create defects. This can also make waste.
- Equipment: When machinery and equipment are not cared for properly, the durability and capabilities of it break down, which leads to frequent replacements.
Smoother Operations
Failing to plan maintenance can cause all sorts of costly problems. Not only can it wreak havoc on finances, but it can also create hazards that can injure or kill workers. Implementing lean management and maintenance are great ways to correct inefficiencies. They are built on a systematic foundation of TPM. To achieve TPM, follow steps for asset management, visual management, and real-time actionable goals. Workplaces should schedule maintenance to take place regularly, or planned maintenance.
Visual communication is an excellent tool that can assist with maintenance for efficiency and safety. Alert staff of machine repairs and servicing using highly durable TPM labels, inspection tags, and signs. Create protective barriers for operators from machine or tool motion hazards by marking maintenance safety zones with floor marking tape. Maintain messages indoors and outside. Train workers to be proactive to help minimize machine failure and improve uptime.
Planning and scheduling provide everyone in the organization with the right tools, materials, people, and instructions to perform the right work at the right time. When combined with digital real-time reporting, it ensures accuracy and correct information. This improves the facility's overall reliability, safety, and strengthens efficiency.
Encourage workers to monitor nearby machines and tools for potential issues with this guide on Total Productive Maintenance.
Related Resources
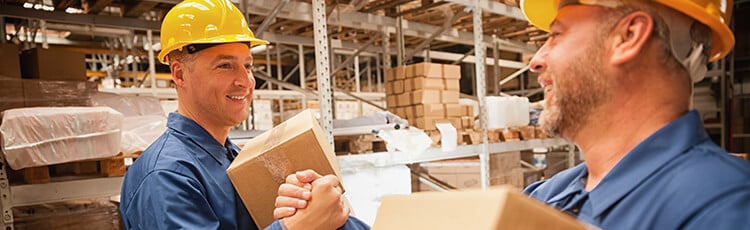
What is Total Productive Maintenance (TPM)?
You're only strong as your weakest link. While trite, the phrase embodies what manufacturing plants and ...
Read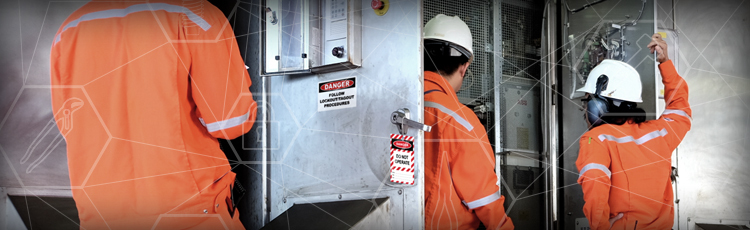
CMMS and Safety in the Workplace
Manufacturing and other industries are harnessing the power of CMMS for maintenance efficiency and safety. ...
Read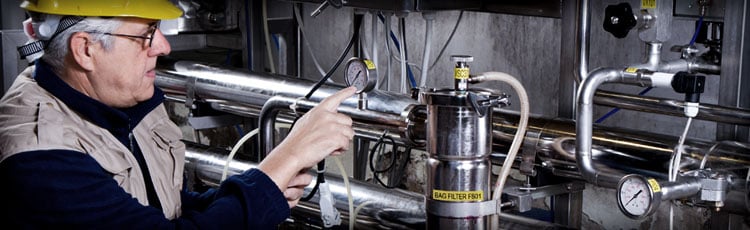
Planned Maintenance
Planned maintenance is a proactive approach to maintenance in which maintenance work is scheduled to take ...
Read