Work Begins When the Lights Go Out

Manufacturers are always looking for ways to improve production demands. The use of autonomous robots, CNC programming, and other industrial technologies will only continue to grow. Industries from warehousing to industrial tooling are benefiting from manufacturing "in the dark." This tactic creates workplaces that function 24/7, even when workers are off for the night or weekend. Facility managers can improve dark manufacturing efficiency further by strengthening hazard control.
Lights Out
Although expensive to implement, dark manufacturing has several benefits. "Smart" machines can work in extreme conditions that human workers would find difficult. This, in turn, improves safety and efficiency, as human workers can then carry on more complex tasks.
By combining basic principles of pattern making with the innovative and incredible power of technology, Peerless Pattern Works develops and produces high-quality patterns and tooling to meet industrial needs. A longtime CNC operator, owner Adam Clayton masters this strategy well. By establishing a focus on introducing new technology and safer processes over time, Peerless is unlocking unprecedented gains in efficiency and productivity. Workers analyze multidimensional blueprints on computers, program large machines, and maintain the shop's progressive production machinery schedule. Worker downtime rates and product defects are lower.
For example, many pattern maker duties include a physical burden of moving heavy pieces of wood and hand carving them. Much of that work has gone away. "Our guys are able to use cranes and forklifts to move the larger patterns and equipment and use the forklifts to set them on the machine, and the machine removes all the material. We're able to program our machines and they run 24 hours a day: we can program them for a couple of hours, hit start and walk away, close the doors, and come back the next day with a finished part."
Highlighting Safety
Creating a dark manufacturing facility doesn't simply involve turning off the lights and going home. Facilities must have the correct equipment on hand. Human workers are best for more flexible operations that require the handling of varied sized product and projects. Remote monitoring and having maintenance on-site also help minimize downtime. Therefore, there is some human worker intervention in the process. There are a few safety features that help make the process efficient and maximize the effectiveness of dark manufacturing.
- Adequate lighting: Although machines do not need light to function, other human staff do. Too much or too little lighting causes worker discomfort and increases safety issues such as risks for slips, trips, and falls. The Center for Disease Control (CDC) cites falling as one of the most common work-related accidents.
- Asset management: Barcodes, QR codes, and other labels assist with the movement and accuracy of automatic systems such as self-driving forklifts, palletizers, and conveyor systems. Be sure to use quality label materials that can withstand heavy traffic and last on varied surfaces.
- Safeguarding: Workers need to be safe from potential injury from automated systems. Ensure messages are clear as to where walking and working areas are through floor marking. Keep signage bold and at eye level to reinforce safety best practices, detail working area restrictions, and more.
- Tools and Personal Protective Equipment: Be ready to provide new tools and equipment as human tasks evolve.
Safety at Peerless is part of the job and facility protocol. Clayton said the company stays on top of regulations. It recently changed some safety measures to implement more modern controls for hazards such as silica and dust, even during dark manufacturing.
"When we implement safety programs, it's literally not optional," Clayton said. "It took a bit but once people get onboard and start using newer or safer equipment, it becomes the norm."
It is integral to businesses that in implementing any new technology, whether automated or human-assisted, that safety is a priority. Management can find helpful visual communication assistance and utilize risk management resources to improve the working environment. Communicate new or changing procedures thoroughly with workers. Consistent communication, training, safety meetings, and improvements are key to any business' success.
Easily identify and solve workplace efficiencies through powerful visuals. Download our free Visual Workplace & Visual Management guide.
Related Resources
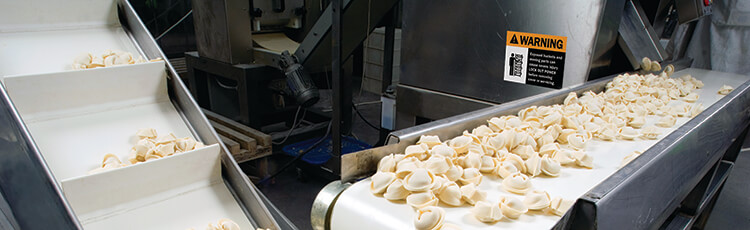
Efficiency and Safety Improvements in Food Manufacturing
Food manufacturing is continuously improving after a huge nudge from a year of disruption. How is food ...
Read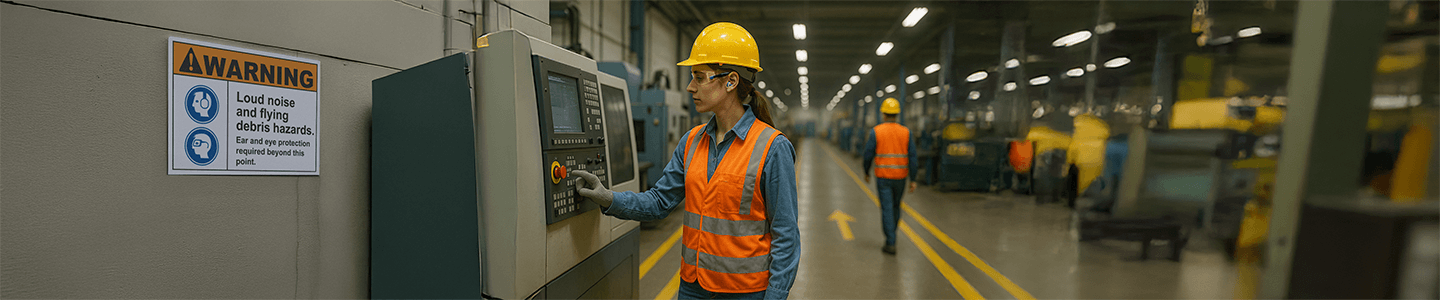
How to Strengthen Building Safety in Manufacturing Facilities
How Do You Keep Manufacturing Facilities Safe and Operational? Building safety in manufacturing facilities ...
Read
Simple Tips for Safety as Manufacturing Powers On
Growth and demand in the manufacturing industry shows no sign of slowing down. This rapid demand also ...
Read