Signage for Safety & OSHA Compliance
Webinar | Signage for Safety & OSHA Compliance
Signage for Safety & OSHA Compliance
Improve your bottom line using safety signs
- Understand the costs and returns of safety
- See how signs play a crucial role in a safety program
- Get tips for creating effective OSHA/ANSI safety signs
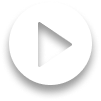
Presented By

Brian McFadden
Technical Writer
Compliance Specialist
Related Resources
Transcript
Webinar Preview
Contents of the Signage for Safety & OSHA Compliance Webinar:
- The Business Case for Safety
- Costs: Direct and Indirect
- Investments Pay Off
- Ways to Improve: VPP and SHARP
- The Role of Signage
- The Mandate for Safety Signs
- Complete OSH Programs
- Attention, Recognition, Understanding
- Keys to effective safety signage
- OSHA and ANSI
- Headers and Signal Words
- Messages
- Sizing and Placement
- Creating Your Own Signs
Excerpt from the Signage for Safety & OSHA Compliance Webinar transcript:
The Business Case for Safety
Costs: Direct and Indirect
The costs of an unsafe working environment are serious. As of January 2018, OSHA's maximum penalty for most citations is now nearly $13,000 per violation, and nearly $130,000 for willful or repeat violations; and these numbers increase each year to account for inflation. It's simply bad business to ignore OSHA's rules.
That said, following OSHA regulations, just to avoid citations, is like stopping your car at a railroad crossing when the barrier is down, just to avoid a traffic ticket. Sure, your reason is a good one; tickets are expensive. But getting hit by a train is much worse!
Beyond the obvious human costs, the direct financial costs of accidents, injuries, and work-related illnesses dwarf the potential OSHA fines. According to the Liberty Mutual Workplace Safety Index, workplace accidents leading to six or more days of missed work directly cost American companies nearly $60 billion in 2014. And that's just the direct costs involved - medical expenses, workman's compensation claims, and so on.
Indirect costs such as administrative expenses, hiring and training replacement workers, and lost productivity can add up even higher. The National Safety Council estimates that the total costs to American employers for preventable workplace injuries reached $120 billion for 2016.
Finally, consider how quickly the news of an accident can spread through a modern, connected marketplace. A single workplace accident can be a PR nightmare, with repercussions ranging from shifting customer preferences to stock price collapses.
Preventing these losses is clearly worth looking into, even if you know it will require an up-front investment.
Investments Pay Off
These safety investments are just that - investments - and their returns are just hard to match. Even the most conservative estimates place the return around two dollars saved for every dollar spent on safety; a separate survey by Liberty Mutual found that the majority of business executives see a three-to-one return or better. According to the American Society of Safety Engineers, one Massachusetts company tracked their costs and benefits carefully, and found an overall return of eight-to-one as they implemented a new safety program!
Safer workplaces don't just benefit from reduced accidents, injuries, and citations, either. In a 2007 study of American manufacturing facilities , a significant correlation was found between safety and operating performance. That is, as measures of safety improved in the facilities studied:
. rates of scrap and rework during production decreased,
. internal measures of reliability and durability improved, and
. external delivery rates increased.
The study backed up a simple and reasonable idea: companies that take care of their workers tend to get better work in return.
Ways to Improve: VPP and SHARP
I've already mentioned OSHA citations as part of the cost of an unsafe workplace, but OSHA's overall goal isn't to penalize companies; it's to protect employees. OSHA offers several positive approaches to help reach that goal, including On-Site Consultations, SHARP, and VPP.
On-Site Consultation Program
For small or medium-sized businesses, it can be difficult to build up the expertise required to start a new safety system. OSHA can help facilities clear this hurdle with the free On-Site Consultation Program. When a company requests help through this program, an inspector comes to the facility - not to give citations, but to point out problems, give practical recommendations, and answer questions. These consultation services include a written report on the issues found, and suggested action plans for improvements: a great kick-start for a new safety program.
Safety and Health Achievement Recognition Program (SHARP)
Companies participating in the free On-Site Consultation Program, and using it to create an exemplary safety program for their facility, may be eligible for the Safety and Health Achievement Recognition Program, or SHARP. This formal recognition from OSHA applauds safety improvements that bring a company's injury and illness rates below their industry's average. In addition to the positive press and the direct benefits of workplace safety, SHARP facilities are also temporarily exempt from normally-scheduled OSHA inspections.
Related Resources
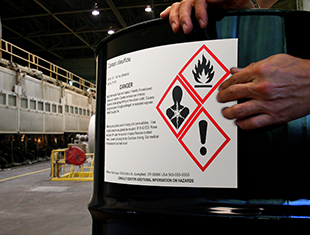
GHS & HazCom for Chemical Safety
Presented By Brian McFadden Technical Writer Compliance Specialist Related Resources GHS Labeling Changes ...
Watch Now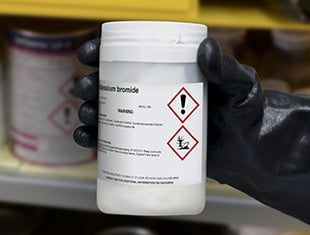
Chemical Risk Assessments
Presented By Brian McFadden Technical Writer Compliance Specialist Related Resources Risk Management ...
Watch Now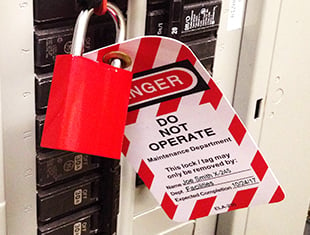
Electrical Safety with Lockout/Tagout
Presented By Brian McFadden Technical Writer Compliance Specialist Related Resources Sample LO/TO Sequence ...
Watch Now