What is HAZOP? HAZOP Analysis and Industrial Label Printer Insights

Workplace safety should always be at the forefront of your mind. Many recommendations exist on how to go about analyzing your workplace to ensure optimal performance and safety, but the go-to recommendation is usually to complete a HAZOP analysis. This begs the question; what is HAZOP?
HAZOP, or a Hazard and Operability Study, is a systematic way to identify possible hazards in a work process that is recognized in OSHA's Process Safety Management (PSM) standard. In this approach, the process is broken down into steps, and every variation in work parameters is considered for each step, to see what could go wrong. HAZOP's meticulous approach is commonly used with chemical production and piping systems, where miles of pipes and numerous containers can cause logistical headaches and the pipe markers may be underutilized.
Industrial label printers, such as the DuraLabel Kodiak Max Industrial Sign and Label Print System, play a vital role in ensuring that these systems have OSHA compliant labels used for clarity and safety. Incorporating an industrial label printer into your safety protocols can streamline the labeling process and ensure that essential information is clearly communicated to workers.
The Importance of HAZOP Analysis
The task of analyzing hazards in a workplace or system can be daunting. However, without an effective analysis, potential hazards may not be discovered before they result in injuries and loss. The cost of an accident is often many times greater than the cost of the analysis that could have stopped it. It's the old proverb: "An ounce of prevention is worth a pound of cure."
There are many ways to assess a process or workplace for hazards, and each approach has strengths and weaknesses. For example, the worker-focused Job Hazard Analysis (JHA) is particularly effective for protecting workers, because it considers each task that a worker must perform and the warehouse safety signs that may be beneficial to prevent risk.
However, if you need to assess a long and complex system, rather than individual workers' safety needs, a broader hazard analysis method may be needed. OSHA lists several common methods of finding the potential hazards in these systems, including:
- What-If Analysis
- Hazard and Operability Studies (HAZOP)
- Failure Mode and Effects Analysis (FMEA)
- Fault Tree Analysis
HAZOP is a common hazard analysis method for complex systems. With the help of the right industrial label printer, it can be used to identify problems even during the early stages of project development, as well as identifying potential hazards in existing systems.
Exploring the HAZOP Study Process
A Hazard and Operability Study systematically investigates each element in a process. The goal is to find potential situations that would cause that element to pose a hazard or limit the operability of the process as a whole. There are four basic steps to the process:
- Forming a HAZOP team
- Identifying the elements of the system
- Considering possible variations in operating parameters
- Identifying any hazards or failure points
Once the four steps have been completed, the resulting information can lead to improvements in the system, such as adding caution signs or wayfinding signs. The best way to apply the results of a HAZOP study will depend on the nature of the system.
1. Form a HAZOP Team
To perform a HAZOP, a team of workers is formed, including people with a variety of expertise such as operations, maintenance, instrumentation, engineering/process design, and other specialists as needed. These should not be "newbies," but people with experience, knowledge, and an understanding of their part of the system. The key requirements are an understanding of the system, and a willingness to consider all reasonable variations at each point in the system.
2. Identify Each Element and its Parameters
The HAZOP team will then create a plan for the complete work process, identifying the individual steps or elements. This typically involves using the piping and instrument diagrams (P&ID), or a plant model, as a guide for examining every section and component of a process. For each element, the team will identify the planned operating parameters of the system at that point: flow rate, pressure, temperature, vibration, and so on.
3. Consider the Effects of Variation
For each parameter, the team considers the effects of deviation from normal. For example, "What would happen if the pressure at this valve was too high? What if the pressure was unexpectedly low? Would the rate of change in pressure (delta-p) pose its own problems here?" Don't forget to consider the ways that each element interacts with others over time; for example, "What would happen if the valve was opened too early, or too late?"
4. Identify Hazards and Failure Points
Where the result of a variation would be a danger to workers or to the production process, you've found a potential problem. Document this concern, and estimate the impact of a failure at that point. Then, determine the likelihood of that failure; is there a real cause for the harmful variation? Evaluate the existing safeguards and protection systems, and evaluate their ability to handle the deviations that you've considered. Perhaps you need to update your labeling system to ensure all of your equipment is labeled to meet the latest requirements.
Results of a HAZOP Study
Because HAZOP is a mental exercise, it can be implemented as part of the planning of a new work process that meets OSHA's processes, even before a facility is built. Existing facilities and processes can also be assessed with a HAZOP analysis.
Where a HAZOP study is performed in the planning stage of a new process, completing the study means that all potential causes of failure will be identified. The HAZOP team will write an assessment weighing the potential deviations, their consequences, their causes, and the protection requirements. From this point, changes to the plan can be made to prevent problems from occurring, or to mitigate their effects.
In existing facilities, a HAZOP may be ongoing, working to improve the process without any specific end date. Instead of a single, large assessment, the study's results will be released as a stream of action items, as each problem is identified and a solution is created. One example of an action item could be something like creating pipe marking labels.
In both cases, when a hazardous condition is identified, recommendations may be made for process or system modifications, or further study by a specialist may be required. A HAZOP study might recommend these typical actions:
- A review of existing protection system designs by a specialist
- Adding or modifying alarms that warn of deviations
- Adding or modifying relief systems
- Adding or modifying ventilation systems
- Increasing sampling and testing frequency
Each of these steps might be recommended as part of the overall Hierarchy of Controls. This way of addressing hazards is intended to prioritize the most effective steps.
The Role of Labeling in HAZOP with an Industrial Label Printer
In the complex processes where the HAZOP approach is most effective, the size and intricacy of the system can be overwhelming. Analysis and maintenance, as well as ordinary, day-to-day operations, require workers to navigate these systems. To allow effective work, system components such as pipes, valves, instruments, and vessels must have OSHA compliant labels.
Often, safely maintaining a system will require monitoring. When measurements must be taken at the same point in a system, it makes sense to clearly mark that point with an indication of the test to be performed. Bad data will ruin the usefulness of any monitoring system.
Opening the wrong valve, or cutting into the wrong pipe, have often been the causes of serious accidents. That's why the ANSI/ASME A13.1 standard is a trusted labeling system for pipes; it requires clear, bold labels in a highly-visible placement scheme.
Whether you need safety signs, pipe markers, or equipment labels—Toro Max and Kodiak Max are ready to transport anywhere you are. Get help crafting a system that will provide the safety communication you need. Call 1-888-897-5580 and one of our experts will guide you through the process.
Learn more about our free HazCom Labeling Instant Action Guide. It gives workers the information they need to be safe, and effective labeling serves that goal.
Read Next:
Related Resources
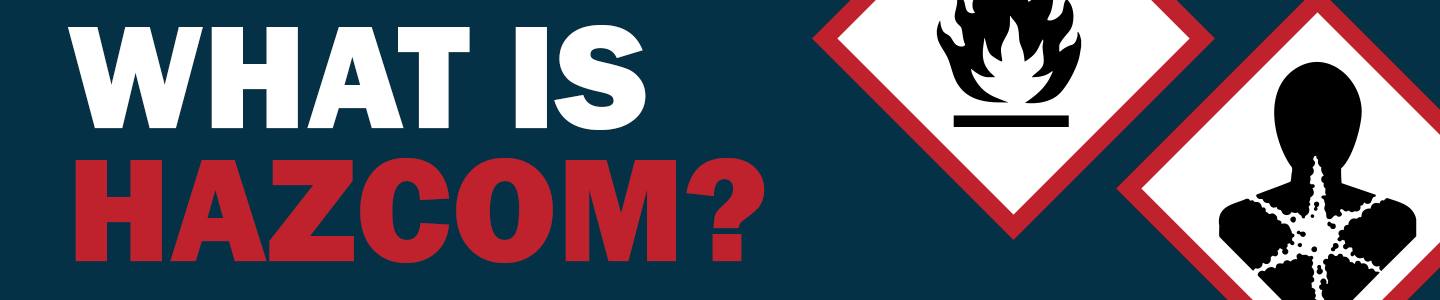
What is HazCom? Your Guide to Chemical Labeling, GHS, & OSHA Standards
What Is OSHA’s Hazard Communication Standard (HazCom)? "HazCom" is short for "Hazard Communication," OSHA’s ...
Read
GHS-Compliance: Safe and Effective Storage of Hazardous Chemicals
The Importance of the GHS When working with and storing hazardous chemicals, steps must be taken to ensure ...
Read
OSHA Rules for Hazardous Chemicals
When dealing with hazardous chemicals, safety is key. However, the steps necessary to keep workers safe will ...
Read