House of Lean: Building the Lean Manufacturing Framework
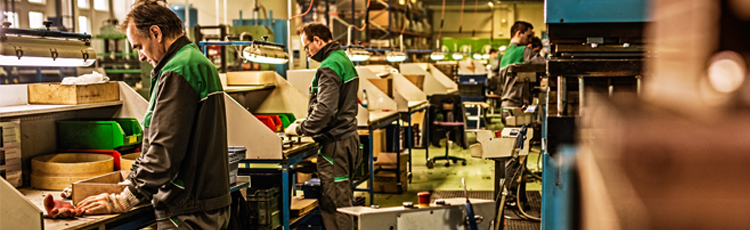
What Is the House of Lean?
The House of Lean is a useful tool that can help you understand Lean Manufacturing principles as a physical structure. It’s used to illustrate the importance of sequencing and interdependency—starting with a solid foundation, building upward through the walls (Lean tools and systems), and finishing with a roof that represents customer focus and long-term improvement.
By breaking down the structure of a Lean framework into parts like people, standardization, flow, and quality, the House of Lean becomes a practical tool for planning and assessing continuous improvement initiatives across manufacturing environments.
The Foundation in the House of Lean
A solid foundation sets up a successful implementation of lean, resulting in improved quality, delivery, and customer satisfaction. This foundation includes:
- People and Purpose
- Stability and Standardization
The first part of the foundation requires people and purpose. This includes strong leadership, employee engagement, mutual trust, and a clear goal. Without these, the foundation will crumble. Lean tools such as Kaizen, a philosophy of continuous improvement, can help you develop these elements.
The next part of the foundation, stability and standardization, will ensure that work is done the right way-every time. This is especially important because it's impossible to sustain improvements without stable processes. You may improve one aspect of your business only to have an ill-thought process negate the improvement. To help with this, use tools like control charts and value stream maps to gain a full understanding of your processes, where they fail, and how you might improve them.
To help with workplace standardization, you can use the 5S system to help create order and standardize how work is done. This powerful tool provides a proven, systematic method for reducing waste and is often the foundation of many lean systems.
The Walls in the House of Lean
The purpose of the walls is to optimize production and quality. Production optimization is essential for ensuring cost-effective, efficient operations, while quality optimization ensures that your expanded production is not wasted on bad results.
Lean tools used to form the walls include Kanban, Heijunka, Just-in-Time (JIT), poka-yoke, Five Whys, and Jidoka. Let's take a look at these lean tools that can help you optimize your production and quality.
Kanban and Production
One tool that can help optimize production is Kanban. Kanban is a system in which customer demand pulls products through the manufacturing process. Products are only made when there are orders from customers, and raw materials are only purchased when needed to produce the products customers have ordered. The result? Your business will:
- Optimize its output
- Optimize the use of workspace
- Reduce the size of its inventory
- Eliminate overproduction and underproduction
- Eliminate work in progress (WIP)
Together, these benefits optimize your production. Orders are completed as needed, eliminating waste caused by overproduction, underproduction, and slowdowns caused by too much WIP. Yet, alone, Kanban is not enough to optimize your production. Another lean tool, like Heijunka, is needed to handle orders that can drastically change from week to week or month to month.
Heijunka and Production
Heijunka is a tool for production leveling. Instead of producing goods in large batches and then becoming idle when orders slow, Heijunka enables you to produce goods at a consistent rate, ensuring that Kanban can continue to pull products through the manufacturing process. Heijunka works through a comprehensive analysis of how orders fluctuate and then planning production based on those fluctuations.
JIT and Production
Both Kanban and Heijunka augment "Just In Time" delivery. The concept of JIT is not complex. The goal is to minimize inventory so that only the absolutely necessary levels of inventory are maintained. This frees up assets that were used to store inventory. The result is that JIT reduces costs and promotes flexibility in production.
Poka-Yoke and Quality
Ensuring that your products are free of defects is just as important as optimizing your production. Defects and errors slow production and result in waste. Poka-yoke involves designing a process so that mistakes are impossible, or so that mistakes are discovered immediately as a natural part of the production process. The ideal result is perfect quality without the need for inspections.
Five Whys and Quality
Another essential tool for ensuring quality is Five Whys. As its name suggests, Five Whys involves asking "why" until the problem's root cause is found. Instead of addressing the symptoms of a deeper problem, the root cause is identified and the problem is eliminated.
Jidoka and Quality
Jidoka can be described as automation with a human touch. This is because processes include equipment that can identify defects. When defects are detected, work stops until the cause of the defect can be found and eliminated, using tools like Five Whys. Jidoka ensures that products sent to customers are free of defects.
The Roof of the House of Lean
The roof of the House of Lean is Customer Focus. This is achieved by providing the best quality, at a reasonable price, with the shortest lead time. You can focus on your customers' needs through the five principles of lean manufacturing. These principles include:
- Understanding what your customers value
- Mapping the value stream
- Creating flow
- Establishing pull
- Striving to continuously improve work processes
By focusing on what your customers need, processes will be streamlined to meet their needs, eliminating processes and features not desired by your customers.
House of Lean Solutions
Support your house by implementing 5S as an essential part of your foundation. Improve your organization and standardize your processes to ensure work is done accurately and consistently with Duralabel comprehensive 5S System Best Practice Guide.
Take Action Today
Want to implement the House of Lean in your facility? Call us today at 1-888-788-9936. One of our experts will help you apply the Lean Manufacturing framework using proven strategies like 5S, Kanban, and Jidoka, alongside DuraLabel’s visual communication tools and Lean best practice guides.
DuraLabel offers additional help with an array of best practice guides, infographics, and articles to help you establish and maintain your House of Lean.
Related Resources
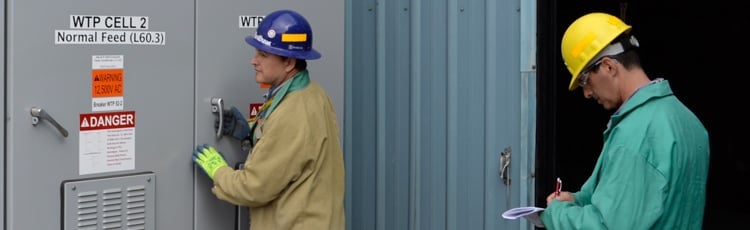
Gemba Walk: A Practical Approach to Lean Process Optimization
Gemba is one of the key principles of lean manufacturing and the Toyota Production System. Gemba is roughly ...
Read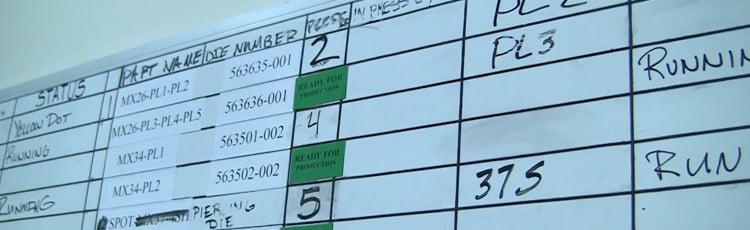
Heijunka Box for Lean Production Leveling
What Is a Heijunka Box and How Does It Support Lean Production? TheHeijunka boxis a scheduling tool used ...
Read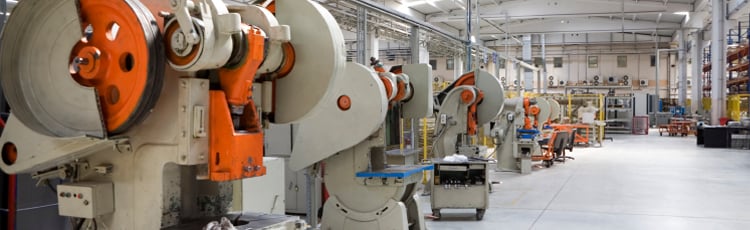
Lean Logistics Techniques
What Are Lean Logistics Techniques? Lean logistics techniqueshelp organizations streamline supply chain ...
Read