Improving Job Site Safety with an Industrial Label Printer
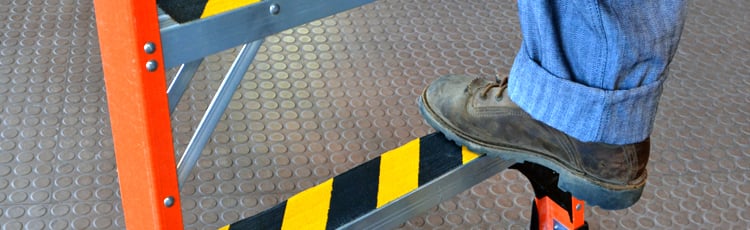
OSHA reports that nearly 6.5 million workers are employed at approximately 252,000 construction job sites in America on any given day. The sad part of the story is that the fatal injury rate on construction job sites is higher than the national average for all industries. Job site safety is important and there are countless methods, and tools, to enhance that safety. Some of those processes include properly labeling equipment with an industrial label printer, like the DuraLabel Kodiak Max Industrial Sign and Label Print System; using equipment the way it was intended to be used; and ensuring a qualified person is handling the machinery.
Defining the Hazards
Five of the OSHA safety standards that are most frequently violated on construction job sites are:
- Scaffolding Safety
- Fall Protection
- Excavation Safety
- Ladder Safety
- Hazard communication
Scaffolding Hazards and Solutions for a Jobsite Safety Plan
What are the job site safety hazards associated with scaffolding? Essentially it is all covered in one sentence, scaffolds that are not erected or used properly. This results in about 4,500 injuries and 50 scaffolding-related fatalities each year.
OSHA Recommended Solutions for Scaffolding Job Site Safety:
- Scaffolding must not be erected, moved, dismantled, or altered except under the supervision of a competent person. A "competent person" has the training and knowledge required to ensure scaffold safety.
- The scaffold must be sound, rigid, and sufficient to carry its weight, plus four times the maximum intended load, without settling or displacement. All job site scaffolding must be erected on solid footing.
- All scaffolding must have clear and visible warning labels indicating weight capacity and safety instructions.
- Unstable objects, such as barrels, boxes, loose bricks, or concrete blocks must not be used to support scaffolds or planks.
- All scaffolding must be equipped with proper guardrails, midrails, and toeboards.
- Any scaffolding accessories, such as braces, brackets, trusses, screw legs, or ladders, that are damaged or weakened from any cause must be immediately repaired or disposed of in a way such that there is no chance the damaged item might be found and used (removed from the job site).
- Scaffold platforms must be tightly planked with scaffold grade plank grade material or the equivalent. If the planking cannot be verified as scaffold grade, it must not be used.
- A competent person must inspect the scaffolding and, at designated intervals, re-inspect it.
- The rigging on all suspension scaffolds on the job site must be inspected by a competent person before each shift and after any occurrence that could affect structural integrity to ensure that all connections are tight and that no damage to the rigging has occurred since its last use.
- Synthetic and natural ropes used in suspension scaffolding must be protected from heat-producing sources and hot surfaces.
- Employees must be instructed about the hazards of using diagonal braces as fall protection.
- The scaffold can be accessed by using ladders and stairwells.
- Scaffolds must be at least 10 feet from electric power lines at all times.
Protection from Job Site Falls
Falls consistently account for the greatest number of fatalities on construction job sites. Many factors are often involved in falls, including some of the other job site safety hazards discussed here such as scaffolds and ladders. In general, job site falls most often result from unstable working surfaces, misuse or failure to use fall protection equipment, and human error. Studies have shown that using guardrails, fall arrest systems, safety nets, covers, and restraint systems can significantly reduce the number of deaths and injuries from falls. It's recommended to review your job site safety plan to confirm that these systems are up-to-date and have no faults.
OSHA Recommended Solutions for Fall Protection:
- When possible use aerial lifts or elevated platforms to provide safer elevated working surfaces.
- Protect workers near the edges of floors and roofs using guardrail systems with toeboards and warning lines, or install control line systems.
- Cover floor and roof holes. Pay particular attention to covering skylights, and other roof and floor openings that may not appear to be a safety hazard.
- Use safety net systems or personal fall arrest systems such as a body harness.
- Verify all equipment and machinery are properly labeled with durable safety labels to communicate potential hazards and necessary precautions.
Job Site Ladder Hazards in a Lean Manufacturing System
Ladders and stairways are another source of job site safety hazards. OSHA estimates that there are 24,882 injuries and as many as 36 fatalities per year due to falls on stairways and ladders used in construction. Nearly half of these injuries were serious enough to require time off from the job.
Ladder Safety:
- Use the correct ladder for the job.
- Have a competent person visually inspect a ladder for any defects before it is used.
- Only use a ladder that is long enough to safely reach the work area.
- Mark damaged or defective ladders for repair or replacement, or destroy damaged ladders immediately. (Use a DuraLabel label printer to make permanent, weather-resistant labels or tags for marking ladders as "Do Not Use").
- Never overload ladders. The total weight on the ladder, including the weight of the user plus any tools and materials, should never exceed the manufacturer's rated capacity.
- Do not move or use ladders with metallic components near electrical work or overhead power lines.
Job Site Trenching Hazards
Trench-related hazards, including collapses, cause dozens of fatalities and hundreds of injuries each year.
Trench Safety on the Job Site:
- Never enter an unprotected trench.
- Always use a protective system for trenches more than five feet deep.
- Employ a registered professional engineer to design a protective system for trenches 20 feet deep or greater.
- Always provide ways to exit a trench--such as a ladder, stairway, or ramp-such that no worker is more than 25 feet away from a safe way to get out of the trench.
- Ensure clear and visible wayfinding signage is installed near trench entrances to guide workers to safe exit points.
- Keep spoils at least two feet back from the edge of a trench.
- Make sure all trenches are inspected by a competent person before workers entering the trench and after any hazard-increasing event such as a rainstorm, vibrations or excessive surcharge loads.
Hazard Communication at the Job Site
Hazards associated with the chemicals on the job site must be communicated. Because work sites can be rapidly changing environments, hazard communication may be delayed or forgotten. As a result hazardous chemicals cause chemical burns, respiratory problems, fires, and explosions.
Hazard Communication Solutions:
- Make creating hazardous material labels fast, easy and convenient by having a label printer that offers countless label solutions, such as a DuraLabel TORO. When labeling can be done quickly and easily, it is more likely to be done.
- Maintain easily accessible, and understandable Material Safety Data Sheets (MSDS) for each chemical in the facility.
- Train employees on how to read, and follow the instructions of the MSDS.
- Train employees about the risks of each hazardous chemical used on the job sites. Training should cover hazardous chemicals used by clients and site owners.
- Provide SpillArrest spill clean-up kits in areas where chemicals are stored.
- Have a written spill control plan.
- Train employees to clean up spills, protect themselves, and properly dispose of used spill clean up materials.
- Provide proper personal protective equipment (PPE) and enforce its use.
- Store chemicals safely and securely.
Security on the Job Site
Job site security refers to protecting your job site from both theft losses and unauthorized intruders. Equipment and material theft from construction job sites is a major source of loss for contractors. A source of some theft is unauthorized intruders, but unauthorized people gaining access to the job site also results in safety and injury issues, liability issues, and potential equipment damage. If these job site security issues can be eliminated that directly adds profit to the bottom line.
Preventing Theft
Job site equipment and material theft has two primary sources:
- People not associated with your company or job site.
- People associated with your job site or company, such as employees, former employees, vendors, suppliers, and subcontractor employees.
For example, delivery truck drivers can be a source of theft. They have easy access to your job site, can get inside job site security fences, and it is not unusual to see them moving and loading/unloading material and equipment.
The Role of Labels and Signs in Job Site Security
The basics of job site security involve installing a security fence around the job site to restrict access and marking it with the appropriate outdoor labels. This includes establishing a "clear zone" for at least five feet inside the fence. No equipment or materials should be placed within the clear zone. The fence should be marked with signs identifying the job site as "No Trespassing" or "Danger - Keep Out" and directing people to the location of gates that allow access.
Thieves are lazy and will go where theft is easy and the risk low. Make sure thieves know your job site is not easy pickings. Use signs around your job site to point out obvious security measures such as "Site Monitored By Security Cameras" and "Reward For Stolen Equipment Tips."
Job Site Equipment and Tools
Job site security involves making it obvious to thieves that your equipment, tools, and materials will be easy to identify and recover. Equipment and tools should be marked with highly distinct bright colors making it easy to identify them as belonging to your company. Also, mark everything with highly visible ID numbers using permanent labels made using a DuraLabel label printer and supplies. You'll have tough-tested outdoor labels that survive in a construction environment and are guaranteed for five years.
In addition to providing a theft deterrent, ID labels are also used to track tools and equipment on the job site. barcodes on the labels makes it easy to "check out" and "check in" equipment and tools. They are also used for conducting inventories, verifying storage locations, and ensuring all equipment and tools are properly locked up or secured at the end of the day. barcode labels can also be used to verify security guards have checked on equipment by requiring specific equipment labels to be scanned during each shift.
DuraLabel also makes unique labeling supplies specifically for security purposes, such as custom UV watermark labels. This DuraLabel supply allows you to make custom labels that have an invisible watermark that is only visible under UV light.
In addition to the labels, bead weld identifying information onto major equipment. This provides a permanent identifying mark that cannot easily be removed. On smaller equipment and tools the ID number can be stamped into the tool, in a hidden location if possible, in addition to the ID label.
To further enhance job site security, in addition to ID numbers, mark equipment and materials with rewards labels. These are labels that offer a reward to anyone reporting the equipment in a location other than your job site.
Marking Materials and Supplies
Materials and supplies should be treated the same way as tools and equipment. Whenever possible they should be stored in locked areas. Be sure that locks are protected so they cannot be cut using bolt cutters. Labeling equipment is crucial; mark your materials and supplies so that it is obvious they can easily be identified. And restrict access to materials and supplies to only those who specifically need access.
Security Signs
Another part of job site security is to ensure employees are doing what they are supposed to do and are only where they are supposed to be. Use job site security signs to remind your employees, and sub-contractor employees, about security and the steps they need to be taking to ensure job site security. Use signs to identify restricted and dangerous areas. Signs can also be used to mark off specific project work areas and identify pathways to and from work areas. Consider utilizing outdoor labels to enhance visibility and durability of signage in outdoor environments.
Any person coming into the job site from the outside is a security threat. Develop a system to verify the identity of people who deliver packages, materials, and equipment. For example, require at least three forms of identification, such as:
- Driver's license
- Company ID card t
- Credit card
as checking in with security when they arrive. As the job progresses you may want to direct different types of deliveries to different areas. This can be done with large custom signs made using your DuraLabel Kodiak Max industrial label and sign printer. Don't just use a single sign to point in the general direction, use a series of signs that mark the path you want deliveries and visitors to follow.
Large Job Site Signs for Visual Factories
In a constantly changing, sometimes noisy environment in which workers come and go, and where multiple languages may be spoken, visual communication is important. That's why job site signs are important.
Job site signs are more than signs to identify your company as the contractor doing the work. On large job sites, signs provide a means of visually communicating important information.
- Job site signs warn employees, sub-contractors, vendors, and visitors about hazards on the job site.
- Job site signs enhance security, identify restricted areas, and direct people and vehicles to follow approved paths.
- Job site signs identify equipment, tools, materials, storage areas, work areas, and offices.
- Job site signs help ensure compliance with OSHA, EPA, NFPA, and other federal, state, and local regulatory agencies.
- DuraLabel job site signs can be printed in multiple languages and using both standard and custom pictograms, symbols, and messages.
With a DuraLabel printer, such as the Kodiak Max, you'll be able to make all of the job site signs and labels you need. Your DuraLabel printer can easily make small wire marker labels and a large job site sign. You can print pipe marker labels, window decals, and OSHA-compliant safety signs. The versatility of a DuraLabel custom sign printer is amazing and that means it delivers a very fast ROI.
Whether you need safety signs, pipe markers, or equipment labels—Toro Max and Kodiak Max are ready to transport anywhere you are. Get help crafting a system that will provide the safety communication you need. Call 1-888-326-9244 and one of our experts will guide you through the process.
Learn lean manufacturing techniques, and establish and reinforce industry best practices. Download our free OSHA Instant Action Guide.
Read Next:
Related Resources
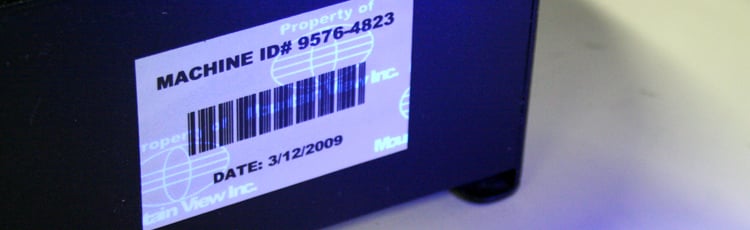
Product Identification
Product identification is a broad category of labeling that includes functions such as product traceability, ...
Read
OSHA and Workplace Safety: A Right for Every Worker
The U.S. Bureau of Labor Statistics (BLS)shared its workplace fatality statistics for 2022. The bureau ...
Read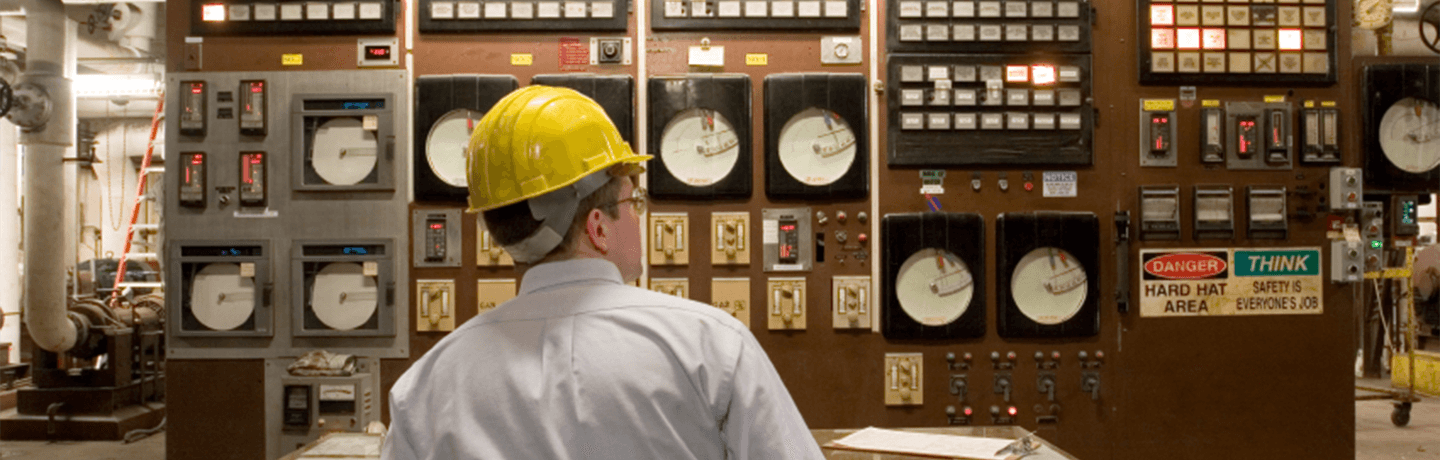
4 Electrical Hazards of the Power Industry: OSHA Signs for Safety
OSHA Signs to Increase Safety in the Electric Power Industry In the high-risk environment of the electric ...
Read