The Benefits of OSHA Requirements and Compliance
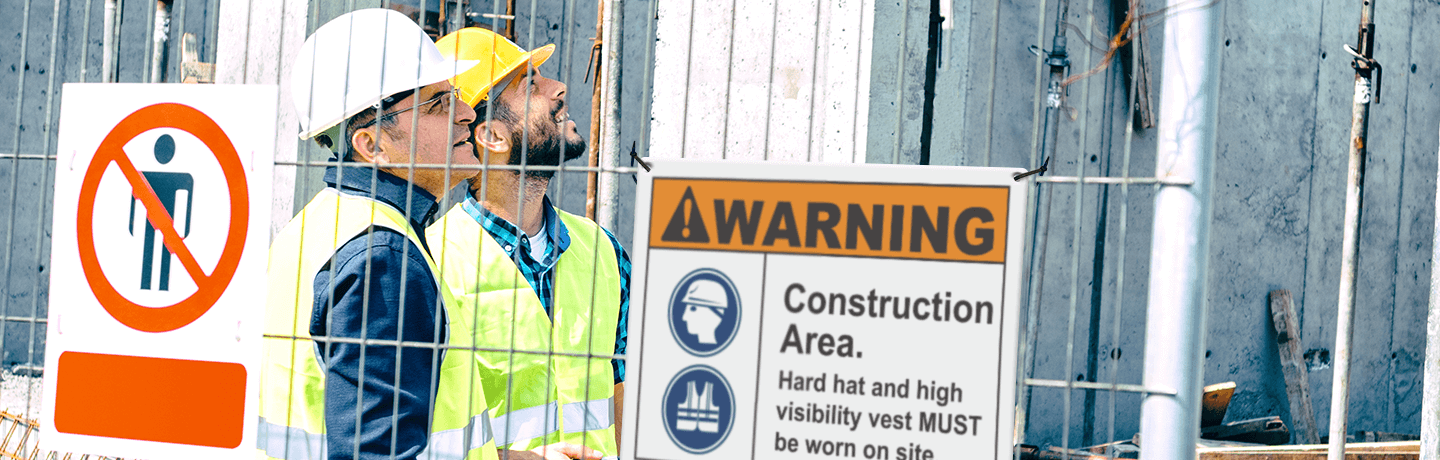
The Occupational Safety & Health Administration (OSHA) is dedicated to ensuring the safety and well-being of 130 million workers throughout the United States. Its regulations cover nearly every aspect of worker safety, from construction workers using fall protection to welders selecting new eyewear.
Numerous rules, regulations, and standards have been developed over the years to minimize the risks faced by workers. Specifically, the Department of Labor's rules for worker safety, including OSHA's regulations, are found in Title 29 of the Code of Federal Regulations.
Within Title 29, OSHA's regulations govern numerous industries. Part 1915 of Title 29 covers shipyard safety, for instance, while Part 1926 covers construction worker safety. The agency's broadest collection of regulations, however, are its standards for general industry; these rules can be found in 29 CFR 1910.
OSHA regularly inspects job sites throughout the country to ensure employers follow regulations and offer a safe workplace. Failing to comply with these regulations may lead to severe consequences, including serious injuries and costly citations. It's vital for employers to understand and comply with OSHA regulations.
How Can Employees Comply with OSHA Requirements?
Every year, OSHA's top 10 violations show where employers can better comply with OSHA regulations and take steps toward safer workplaces. Here are a few common violations-and how employers can address those compliance issues:
- Fall Protection: OSHA's most-cited violation for five years running, fall protection is also the leading cause of death in the construction industry. 29 CFR 1926.501 lists the agency's requirements for fall protection, and this article lays out OSHA's guidelines for ladders, construction sites, general industry practices, and more.
- Lockout/Tagout: The procedures to protect employees from the unexpected startup of machinery, lockout/tagout (LO/TO) is a mainstay on OSHA's list of most common violations. 29 CFR 1910.147 lists the agency's requirements for ensuring employee safety while servicing or performing maintenance on dangerous equipment; OSHA estimates that compliance with the standard could prevent an estimated 120 fatalities and 50,000 injuries each year. Learn more in Graphic Product's free Best Practice Guide to Lockout/Tagout.
- Hazard Communication: As of June 1, 2016, all United States employers should be in compliance with HazCom 2012, OSHA's regulations that govern the labeling of chemical hazards in the workplace. Employers can gain a better understanding of the regulation and take steps toward compliance with Duralalbel' Best Practice Guide to HazCom 2012 Labeling.
Benefits of OSHA Compliance
There are numerous benefits to complying with OSHA regulations, and promoting a culture that emphasizes safety can have far-reaching impacts throughout a company. Here's why it helps to ensure OSHA compliance:
- Save money: Investing in a safer workplace might mean some up-front costs, but the benefits pay off in the long-term. Employers who comply with workplace regulations can avoid costly OSHA citations, and save money on worker compensation and other insurance costs.
Even small businesses may benefit from implementing a safety plan and complying with key standards. According to OSHA, implementing a safety and health program can save small businesses $4 to $6 for every $1 invested. - Ensure a safer facility: Compliance with OSHA regulations lessens the risk of accidents and injuries, which leads to a safer facility. For instance: U.S. employment has doubled since OSHA's formation in 1970, yet workplace fatality, injury, and illness rates have dropped by roughly two-thirds in that same stretch.
- Improve morale: You can send a clear message to your employees through a strong dedication to safety. Even in risky environments and occupations deemed as dangerous, workers will feel more productive and less distracted knowing their employer understands and abides by the relevant regulations.
Following OSHA Requirements with Visual Communication
Employers looking to better understand OSHA regulations can start with 29 CFR 1910.145, the agency's requirement for signs and labels that recognize workplace hazards. The standard improves safety by outlining design requirements and when to use safety signs; given that almost every facility can benefit from suitable signage, the standard outlines a clear path forward for ensuring that hazards, risks, and warnings are properly communicated.
DuraLabel industrial label and sign printers by DuraLabel can help you develop visual communication that complies with OSHA regulations. DuraLabel printers can be used with more than 50 application-specific supplies, including abrasive or irregular surfaces, saltwater environments, low-light settings, greasy equipment, and more.
Learn lean manufacturing techniques, establish and reinforce industry best practices. Download our free OSHA Safety Signs Guide for an overview on OSHA and ANSI standards, instructions for creating custom signs, and more.
Read Next:
Related Resources

HazCom Basics: Chemical Labeling 101
In the regulatory-driven healthcare environment, proper chemical labeling is required to ensure safety and ...
Read
Hazardous Chemicals Overview
In the eyes of OSHA, hazardous materials run the gamut from household cleaners to deadly gasses. Effects can ...
Read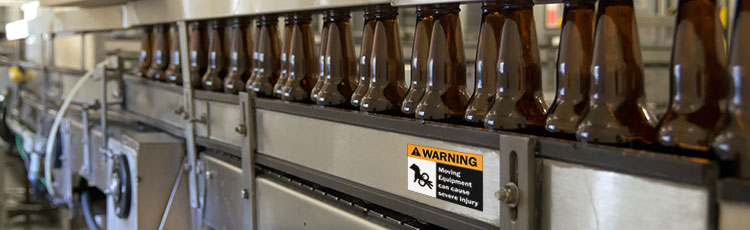
Brewery Safety: Common OSHA Violations and How to Stay Safe
Beer has never been a bigger business in the United States than it is today. The Brewers Association reported ...
Read