The Importance of Labeling for Safe Compliant Electrical Installations
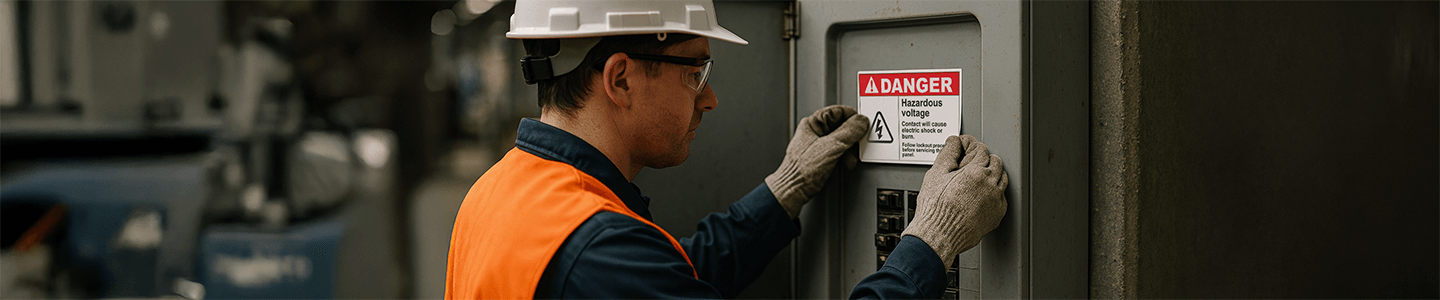
Electrical installations require more than just technical skill—they demand clarity, consistency, and compliance. One overlooked but critical component is electrical labeling. Whether working on a new build, a retrofit, or an industrial maintenance environment, using clear, compliant labels is essential for protecting workers, maintaining regulatory compliance, and improving long-term efficiency.
In 2023, the Bureau of Labor Statistics (BLS) reported 142 fatalities caused by exposure to electricity. This sobering figure underscores the need for consistent safety practices—including proper labeling. Electrical systems often span multiple panels, junctions, and disconnects, making clear identification essential. Labels guide workers, prevent errors, and reinforce hazard awareness, directly supporting Occupational Safety and Health Administration’s (OSHA) electrical safety standards.
Electrical Labeling Improves Safety
From installation to inspection and ongoing maintenance, effective electrical labeling enhances safety across every stage of a system's lifecycle. Technicians rely on labels to quickly determine which circuits are live, what equipment is energized, and where lockout/tagout procedures apply. When labels are missing, unclear, or inaccurate, workers face increased risk of electrical shock, arc flash, and equipment damage.
OSHA labeling requirements call for the clear identification of:
- Electrical hazards
- Circuits
- Disconnecting means (i.e., circuit breakers and disconnect switches)
Meeting these requirements helps prevent incidents that could lead to injury or death. Labels act as a visual safety net, providing professionals with the critical information they need to take proper precautions—especially during time-sensitive tasks or emergency shutdowns.
Electrical Panel Labels Support Code Compliance
Beyond safety, labeling plays a central role in regulatory compliance. Labeling standards such as NFPA 70E mandate specific label types, wording, and placement for electrical components. These standards require clear, durable electrical panel labels to identify service panels, circuit breakers, and disconnects.
For example, NFPA 70E requires that arc flash warnings and voltage ratings be visible and easy to understand. Likewise, OSHA requires safety signs, symbols, or accident prevention tags to warn employees of electrical hazards—such as electric shock, burns, or arc-flash risks. Following these regulations reduces the risk of fines, failed inspections, and shutdowns.
Inspectors often check labels first. Clearly marked systems streamline inspections, while unlabeled or poorly labeled systems raise red flags, even if the wiring is technically sound. Professional installers understand that labeling is a critical part of delivering a code-compliant system.
Streamlines Maintenance and Troubleshooting
Even the most well-designed electrical systems require maintenance and updates over time. That’s where electrical labeling proves its long-term value. Technicians often troubleshoot systems years after installation—sometimes with limited or no documentation. Durable, well-placed labels provide lasting guidance, helping teams trace circuits, isolate faults, and verify equipment without guesswork.
In the field, good labeling is the mark of a skilled professional—it's what separates a shortcut from a system built to last. Electricians who prioritize clear, consistent labels build trust, reduce callbacks, and protect their reputation.
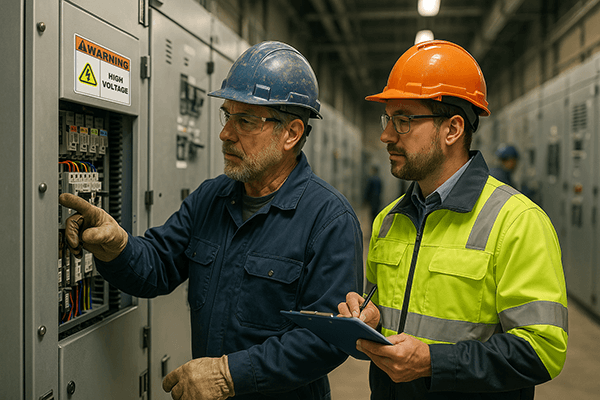
Electrical panel labels also make it easier to identify the source and load sides of a circuit, reducing the time spent opening enclosures or testing voltage. In facilities with multiple service areas or complex distribution systems, clear labeling simplifies both routine inspections and emergency repairs. It also minimizes downtime—translating to real cost savings for the business.
Labeled systems also promote consistency across departments. Maintenance personnel, electrical contractors, and safety officers all benefit from standardized labeling that supports a shared understanding of the system layouts and component functions.
Reduces Installation Errors and Rework
Misidentifying wires, terminals, or circuits can lead to costly mistakes or dangerous conditions. Using clear, durable labels helps contractors reduce the risk of errors during system commissioning and installation. Each label acts as a checkpoint for quality, supporting accuracy at every stage of the process.
Following best practices for electrical labeling helps:
- Verify component function
- Reduce confusion during panel layout
- Simplify circuit tracing
For example, clearly marking all breakers in a panel with permanent electrical panel labels helps avoid cross-wiring and overload conditions. In commercial and industrial settings, OSHA regulations require contractors to maintain a safe working environment by identifying and addressing electrical hazards. Proper labeling plays a direct role in meeting these obligations.
It’s easier to deliver a safe, reliable installation when all team members work from the same visual cues.
Supports Long-Term Facility Growth and Efficiency
As buildings evolve, so do their electrical systems. Moves, additions, and system upgrades are common—especially in facilities with expanding equipment needs or changing production lines. Clear electrical labeling supports these transitions by providing a roadmap for future expansion.
When consistent labels are in place, new contractors and internal maintenance crews can easily interpret system layouts. That reduces onboarding time and speeds up the installation of new components. Facilities that implement best practices for electrical labeling also benefit from:
- Easier asset tracking
- Efficient recordkeeping
- Improved load management and electrical capacity planning
In critical environments—such as manufacturing, data centers, and healthcare—clear labeling supports operational continuity. Accurate electrical panel labels help prevent unnecessary shutdowns and ensure that system changes do not compromise safety or compliance.
Best Practices for Electrical Labeling
Meeting labeling standards involves more than just using a label maker. High-quality, application-specific materials are essential for durability. Depending on the environment, labels must resist heat, moisture, chemicals, and UV exposure. Smudged, peeling, or faded labels fail to meet OSHA labeling requirements and undermine electrical safety. Smudged, peeling, or faded labels do not meet OSHA labeling requirements or support OSHA electrical safety.
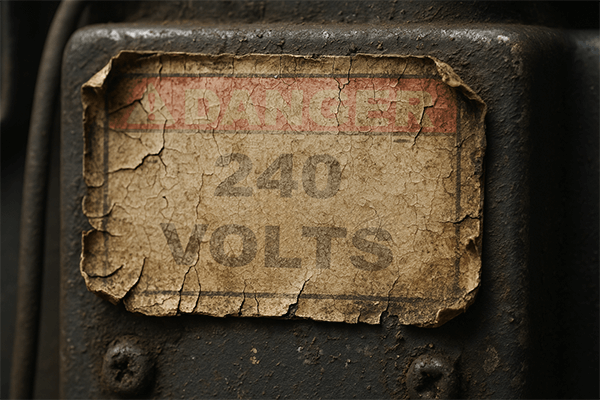
To support compliance and improve usability, follow these best practices for electrical labeling:
- Use permanent, legible print with standardized language
- Include voltage levels, source/destination info, and hazard warnings
- Follow color-coding and sizing standards for readability and consistency
- Update labels after modifications or repairs
- Place labels where they are clearly visible and unlikely to be obscured or damaged
To support compliance and improve usability, follow these best practices for electrical labeling:
- Use permanent, legible print with standardized language
- Include voltage levels, source/destination info, and hazard warnings
- Follow color-coding and sizing standards for readability and consistency
- Update labels after modifications or repairs
- Place labels where they are clearly visible and unlikely to be obscured or damaged
Organizations should also train their teams on proper label placement and content. When everyone follows the same standards, labeling remains consistent—even as systems change over time.
Electrical Labeling DuraLabel Resources
Whether you’re installing new panels, upgrading circuits, or maintaining high-voltage equipment, durable, compliant labels help reduce risk and support long-term performance.
Electrical labeling requires more than a basic label maker. You need materials engineered to last—and a system that keeps up with your schedule. DuraLabel Premium Vinyl Label Stock delivers a tough-tested solution for creating clear, long-lasting electrical panel labels, conduit markers, voltage warnings, and more. These labels resist heat, moisture, and abrasion, supporting both OSHA electrical safety and NFPA 70E labeling standards.
With the DuraLabel Toro Max Industrial Sign and Label System—a portable, all-in-one industrial sign and label printer—contractors can print compliant labels on demand. Whether it’s for circuit ID, arc flash warnings, or multi-language safety signage, Toro Max makes it easy to produce exactly what your project requires, right on-site.
For large-scale projects or standardized systems, DuraLabel also offers a custom sign and label service. Simply upload your job site specifications, and our team will create professional-grade labels tailored to your exact needs.
Learn how better electrical labeling can reduce installation errors, support safety, and streamline inspections. Download DuraLabel’s free Facility Signage Handbook, or call 1-888-342-3164 to speak with a safety and efficiency professional about the right labeling solution for your next electrical project.
Read Next:
Why Custom Industrial Labels Matter for Mechanical Job Sites
Keep Job Sites Safe: How Custom Labels Change the Game for Contractors
Related Resources
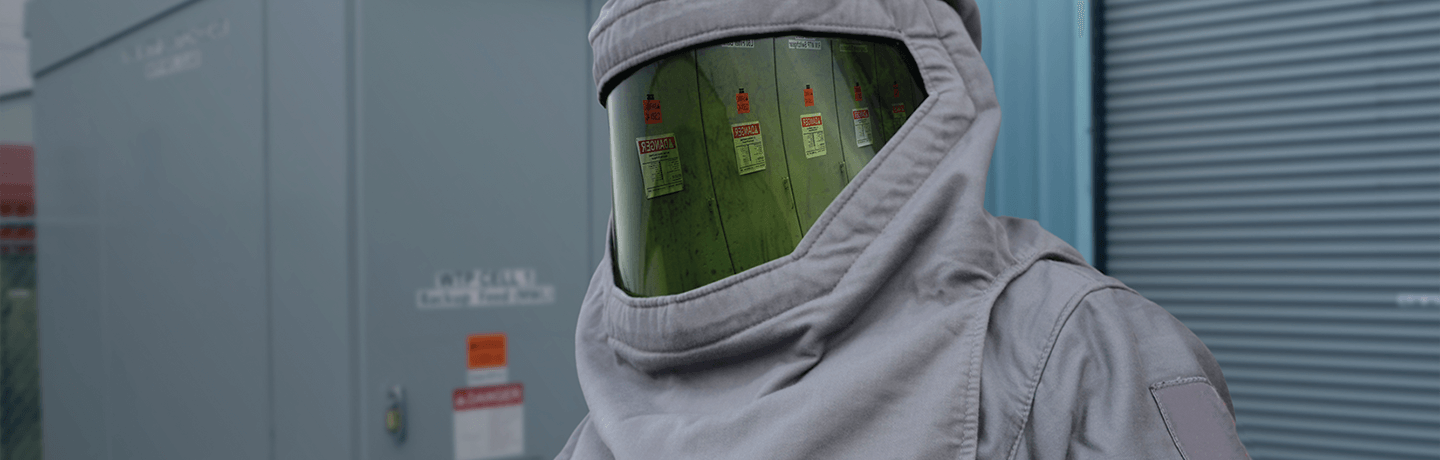
NFPA 70E Arc Flash with OSHA Signs
What is NFPA 70E? NFPA 70E, or the NFPA's Standard for Electrical Safety in the Workplace, outlines specific ...
Read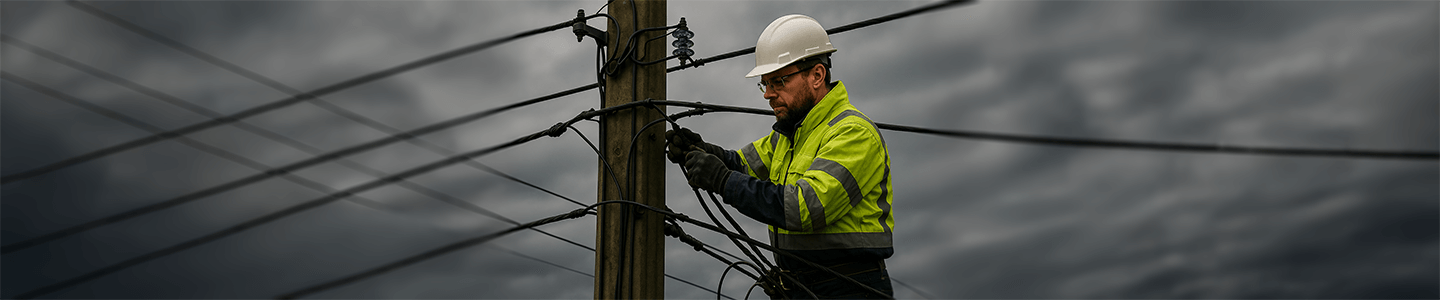
Why Every Workplace Safety Plan Must Address Electrical Hazards
What Threatens Workplace Safety in Electrical Jobs? Electrocution, arc flash, contact with energized ...
Read
OSHA and Workplace Safety: A Right for Every Worker
The U.S. Bureau of Labor Statistics (BLS)shared its workplace fatality statistics for 2022. The bureau ...
Read