Why Every Workplace Safety Plan Must Address Electrical Hazards
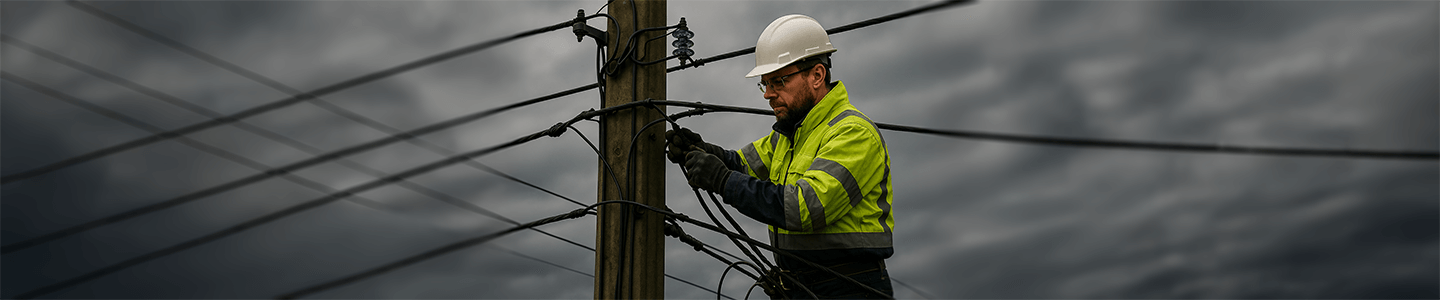
What Threatens Workplace Safety in Electrical Jobs?
Electrocution, arc flash, contact with energized conductors, and overhead line accidents—these aren’t rare events. They are routine failures in environments where workplace safety should be embedded into every process.
And they are still happening far too often.
Electrical work is among the most hazardous occupations. According to the Electrical Safety Foundation International (ESFI), the job roles with the highest number of electrical fatalities include:
-
Electricians: 195 fatalities
-
Construction laborers: 119 fatalities
-
Laborers (except construction): 117 fatalities
-
Electrical power installers and repairers: 109 fatalities
-
Tree trimming occupations: 94 fatalities
-
HVAC and refrigeration mechanics: 42 fatalities
Many of these fatalities are preventable with stronger procedures, better training, and more effective safety signs and labels. If a facility has not evaluated its electrical safety practices this year, they are already behind.
How Do Current Electrical Standards Strengthen Workplace Safety?
The National Electrical Code (NEC) is updated every three years to incorporate new protective technologies and best practices. But many facilities still operate under outdated versions—or don’t fully adopt the most recent code. This disconnect puts employees at greater risk.
Out-of-date compliance leads to dangerous assumptions and poor equipment identification. And in high-risk environments—electrical rooms, confined spaces, industrial control panels—those assumptions can be fatal.
Organizations committed to safety compliance regularly review electrical system layouts, signage, and labeling. They prioritize updated procedures that reflect current standards—not last decade’s playbook.
Which High-Risk Zones Rely Most on Safety Signs and Labels?
Some of the most common electrical hazards exist in places workers pass through every day:
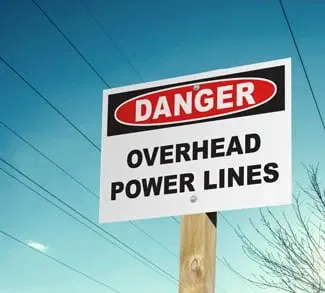
-
Unlabeled circuit breakers or transformer panels
-
Improper or missing arc flash hazard warnings
-
Confusing or outdated conduit markings
-
Lack of visible lockout/tagout instructions
-
Water-adjacent equipment without Ground Fault Circuit Interrupter (GFCI) labeling
Overhead lines remain a leading cause of electrical fatalities—especially among telecom and utility workers. Many of these incidents happen because of unclear communication or missing visual warnings.
Labeling is often the last line of defense. Without clear, durable safety signs and labels like those made with DuraLabel Premium Vinyl Supply, even well-trained employees can make dangerous mistakes.
What are the Highest-Risk Jobs for Workplace Safety?
Electrical hazards don’t affect only licensed electricians. A wide range of job roles involve direct or incidental contact with energized equipment, and many of these workers operate in environments where risks can change by the hour. The following occupations consistently face the highest exposure to electrical hazards, often with limited warning and few visual safeguards in place.
Electricians
These workers routinely interact with energized equipment, high-voltage systems, and confined electrical spaces. Even minor oversights—like a missing arc flash label or outdated panel marking—can result in serious injury. Ladder safety, fall protection, and energized work protocols play a critical role, but without clear signage and consistent procedural training, they’re not enough.
Construction Workers
Construction laborers face constant exposure to temporary power, open circuits, and incomplete electrical systems. They often work in dynamic, fast-paced environments where wires, panels, and access points are moved or modified daily. High-visibility signage and custom label systems help communicate real-time hazards and prevent accidental contact with live components.
Laborers (Except Construction)
Laborers outside the construction industry—such as those in warehousing, landscaping, or general maintenance—often encounter electrical hazards unexpectedly. These workers may not be trained to recognize or respond to those risks, which makes clear labeling and hazard identification even more important. Safety signs and labels provide essential context in mixed-use or high-traffic areas where temporary power or buried lines may go unnoticed.
Don’t Wait for an Accident to Improve Workplace Safety
An effective electrical safety program goes beyond compliance checklists. It requires a proactive approach that combines physical protections, training, and clear visual communication.
Here’s what to implement now:
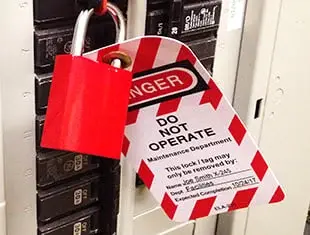
-
Routine Training: Train employees on current NEC standards, PPE protocols, and arc flash risk assessments. Make refresher courses part of your annual calendar.
-
Visual Standards: Audit your facility’s signage. Replace any label that’s outdated, worn, or missing. Use a consistent format for high-voltage, GFCI, and lockout/tagout zones.
-
Emergency Planning: Power surges, natural disasters, and unexpected failures should already have a response protocol in place. Conduct drills to reinforce readiness.
-
Proper Equipment Usage: Use products certified by Nationally Recognized Testing Laboratories (NRTLs) and test fault currents regularly.
-
Smart Labeling Systems: Deploy safety label software like DuraLabel LabelForge PRO to streamline labeling across departments and ensure consistency.
Customizing your visual system with the right safety label software can reduce confusion, prevent shortcuts, and improve audit readiness.
Why Is Labeling an Ongoing Pillar of Safety Compliance?
Labels are more than reminders. They are tools for hazard prevention, especially when they're part of a broader safety compliance strategy.
Outdated or handwritten labels create inconsistencies that erode trust in your safety program. A standardized approach using custom label templates, built through modern safety label software like LabelForge PRO, gives safety teams control over the messaging, placement, and durability of all critical signage.
This isn’t just about passing inspections. It’s about making sure the next decision a worker makes—at a panel, near a line, in a confined space—is the right one.
DuraLabel Resources to Enhance Workplace Safety
A successful workplace safety program depends on clear, consistent communication, especially when it comes to electrical hazards. As equipment changes or safety standards evolve, your labeling must adapt just as quickly.
DuraLabel provides the tools needed to create and maintain compliant electrical signage across any facility. The DuraLabel Toro Max Industrial Sign and Label System delivers a rugged, all-in-one solution for printing safety signs and labels on site. It eliminates delays caused by outsourcing or returning to a central office for label production.
Built for tough environments, the Toro Max comes equipped with LabelForge PRO. This intuitive safety label software includes preloaded templates, built-in compliance standards, and customizable options for voltage markings, arc flash warnings, lockout/tagout procedures, and other critical visuals.
When you need reliable labeling solutions to support safety compliance across multiple departments or locations, DuraLabel makes it simple to create, update, and standardize your custom label system.
To begin improving your facility's electrical safety communication, contact a DuraLabel representative at 1-888-788-9936. You can also download the free Electrical Safety Quick Start Guide for step-by-step labeling strategies and practical tips that support safer, code-compliant facilities.
Read Next:
Essential Electrical Labeling for Contractors and Facility Managers
Miswired and Mislabeled: The Electrical Errors That Could Cost You
Related Resources
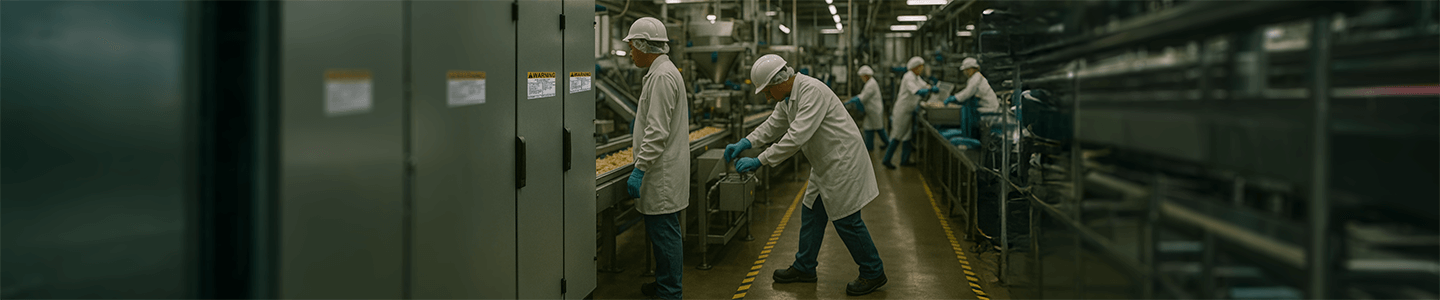
How Visual Tools Improve Electrical Safety in Food Processing Plants
Visual Tools That Improve Electrical Safety in Food Processing Plants Electrical safety is a high-stakes ...
Read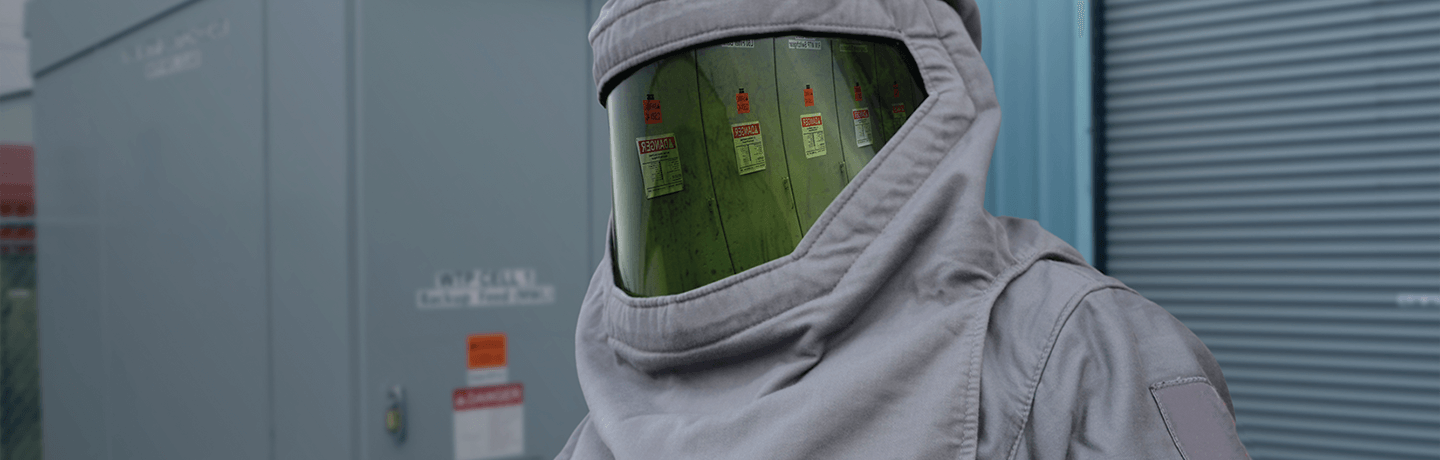
NFPA 70E Arc Flash with OSHA Signs
What is NFPA 70E? NFPA 70E, or the NFPA's Standard for Electrical Safety in the Workplace, outlines specific ...
Read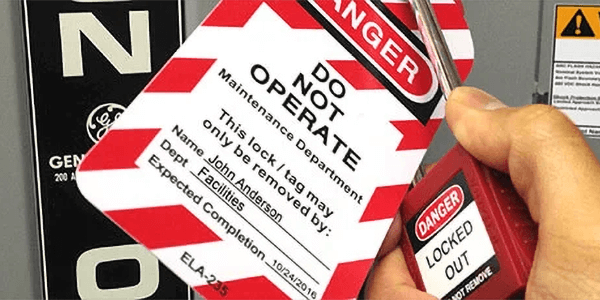
How to Prevent Arc Flash with Lockout Tagout Signs and Safety Labels
What Are the First Steps to Preventing Arc Flash in the Workplace? In the realm of electrical safety, the ...
Read