Machine Guards and Amputation Hazards
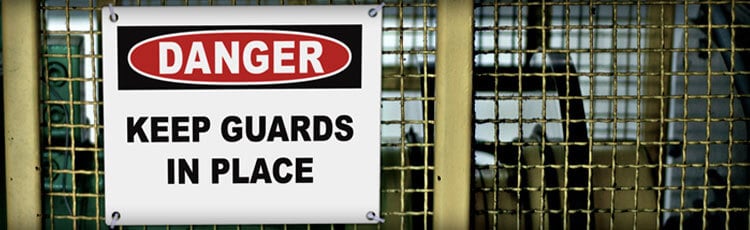
One of the first facets of workplace safety to be regulated by the Occupational Safety and Health Administration (OSHA) in 1971 was operating or maintaining industrial machinery due to the high risk of injury. To emphasize the importance of machine safety, OSHA launched a nationwide emphasis program on machine-related amputations and how to prevent them.
OSHA's machine safety standard focuses on protecting workers from the hazards associated with machinery operation. The standard requires employers to implement proper machine guarding to prevent injuries from moving parts, such as amputations or crushing incidents. These safeguards, along with clear safety signs and labels, ensure that workers are aware of potential dangers and understand how to operate machinery safely. Compliance with OSHA's machine safety standard helps reduce the risk of accidents and maintain a safer work environment.
Accidents resulting from machinery are common and often result in death or amputation. According to OSHA, each year approximately:
- 18,000 incidents that result in amputation
- 800 workers are killed from encountering objects and equipment
Machine guarding accidents carry a distinct stigma, the knowledge that a worker's life was needlessly taken or will be irreversibly changed by the absence of a simple lock or piece of metal or plastic. Take the recent story of Kim Duong. Duong worked for the steel fabricating company John Crowley Inc. off and on for six years. He was well-known around the company, and revered for his work ethic and safe practices.
Duong was crushed by two six-hundred-pound machine guards earlier in the year. He was operating a shot blaster, a machine used clean, peen, or polished metal, when he climbed underneath the guards and bumped them causing the guards to fall. This story leaves questions unanswered, such as, were the guards properly installed if a slight bump could cause the two six hundred-pound guards to fall? Death is only one of the undesirable outcomes of machine-guarding accidents. Amputation is one of the most severe and crippling types of injuries a person can sustain, and it often results in permanent disability or mental trauma. These incidents occur more often when workers operate unguarded or inadequately safeguarded machinery.
Kina Repp is a woman who sustained an injury on her first day on the job that resulted in the amputation of her left arm. Her life was never the same and she had to adapt, and relearn basic skills and now helps promote worker safety, empowering employees to take responsibility themselves. Her message is awareness and education, urging those working in dangerous conditions to stay safe and assuring workers who have sustained amputations that their lives can be full and rich. Repp exemplifies that you are only as limited in life as you believe yourself to be.
What Is an Amputation Hazard?
With proper training and protective measures, there's always a way to effectively use any machine. OSHA defines an amputation hazard as any moving machine parts that have the potential to cause severe workplace injuries, such as crushed fingers, amputations, burns, or blindness. Amputation hazards fall under the arena of safety known as machine guarding because the best way to prevent these injuries is by adding safeguards to known hazards. As a general rule of thumb, whenever a machine uses reciprocating, rotating, and transverse moving parts, there's a high chance it is a hazard. Here are some more specific mechanical components that, when exposed, often create amputation hazards:
- Flywheels
- Pulleys
- Belts
- Chains
- Couplings
- Spindles
- Cams
- Gears
- Power Transmission Apparatuses
Some machines are labeled more dangerous than others, as they are the machines that create the highest risk of amputation. Here is a short list of some of the most prevalent machines that are at greater risk of amputation:
- Power Presses
- Power Press Brakes
- Powered and Non-powered Conveyors
- Printing Presses
- Roll-forming and Roll-bending Machines
- Food Slicers
- Meat Grinders
- Meat-cutting Band Saws
- Drill Presses
- Milling Machines
- Shears
- Grinders
- Slitters
These machines do not need to be operating to create a hazard. Often workers sustain injuries from improper cleaning or maintenance procedures. Lockout/Tagout (LOTO) is the best way to assure worker safety during maintenance and should always be present when machines create such serious hazards. It should also be noted that amputation hazards can be present, even when large machinery is not used. There is a connection between amputations and material handling activities, such as the presence of forklifts, or the use of handheld power tools.
User-Built vs. Producer-Built Guard
The most efficient way to reduce and eliminate amputation hazards is through machine guarding. Guards designed and installed by the machine producer are always preferred because they fit the exact design and function of the machine. User-built guards are sometimes necessary but can have some advantages.
User-built guards are the only practical solution with older machinery, due to the mechanical power transmission apparatuses in older plants. User-built guards can be designed and built to fit unique and changing situations and can be installed to eliminate specific hazards that present issues. When workers are aware of the design and how the machine guard is, they gain a better knowledge of those guards and how they work.
There are some disadvantages. User-built guards might not conform well to the machine, or be effective and might be poorly designed or built. Always consult the manufacturer, even when building a machine guard yourself, to ensure that you aren't overlooking any potential hazard, or creating a new one.
Guards are constructed from metal, plastic, and wood. In many circumstances, because of its strength, durability, and longevity, metal is the best material for guards. Plastic guards are primarily used when higher machine visibility is required. Guards made of wood are not compliant in most cases because of wood's flammability, lack of strength, and often flimsy nature. Wood guards are only preferred in industries that utilize chemicals, gases, or vapors where manufacturing conditions would quickly deteriorate metal guards. Wood guards also may be used in construction work and in outdoor locations where extreme cold makes metal guards undesirable.
Types of Machine Safeguards
Safeguards can be grouped under four general classifications:
- Fixed guards - Permanent parts of a machine, these guards are preferable because they're simple and permanent.
- Interlocking Barrier Guards - Automatically shuts off or disengages a machine through a tripping mechanism or power when the guard is opened or removed.
- Adjustable guards - Useful because they accommodate various sizes of stock.
- Self-adjusting guards - Allows the opening of the barrier to be determined by the stock. As the operator moves the stock into the danger area, the guard is pushed away, allowing entrance
Here is a table for quick reference when deciding what type of guard to use at your facility:
Type | Safeguarding Method | Advantages | Limitations |
---|---|---|---|
Fixed | Barrier that allows for stock feeding but does not permit the operator to reach the danger area. |
|
|
Adjustable | Barrier that adjusts for a variety of production operations. |
|
|
Self-Adjusting | Barrier that moves according to the size of the stock entering point of operation. A guard is in place when a machine is at rest and pushes away when the stock enters the point of operation. |
|
|
Interlocking Barrier Guards |
Shuts off or disengages power and prevents machine start-up when the guard is open. Should allow for inching of the machine. |
|
|
Prevent Catastrophic Accidents with DuraLabel Solutions
Preventing injuries starts with clear communication. DuraLabel signs and labels provide essential visual cues that help reinforce machine safety protocols. With highly visible and durable designs, these labels can mark hazards, identify machine controls, and display critical safety instructions. By implementing DuraLabel solutions, you create a safer environment that minimizes risks and helps ensure employees are protected from dangerous equipment.
The DuraLabel Kodiak Max Industrial Sign and Label Print System takes machine safety to the next level by giving you the ability to create custom signs and labels on demand. Its two-color printing and high-quality materials allow you to produce durable, customizable safety signs that stand up to harsh environments. Whether you need labels to mark emergency stops, warning signs for hazardous areas, or instructional labels for machinery, the Kodiak Max offers a versatile and efficient solution for keeping your workplace safe.
Want to learn more about how to be compliant with OSHA signage? DuraLabel’s free OSHA Signage Quick Start Guide helps you create OSHA/ANSI-compliant safety signs. The free guide helps readers understand the appropriate regulations and standards and improve safety and efficiency. You can also contact DuraLabel at 1-888-695-5670 and a dedicated rep will help you create a visually-safe facility.
Read Next:
Related Resources
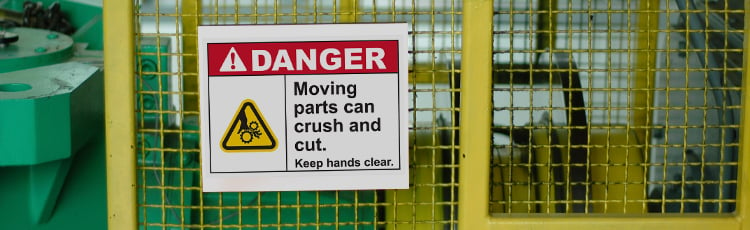
Avoiding OSHA Fines: Machine Guarding
OSHA produces an annual list of the Top 10 Most Frequently Cited Standards and year after year, machine ...
Read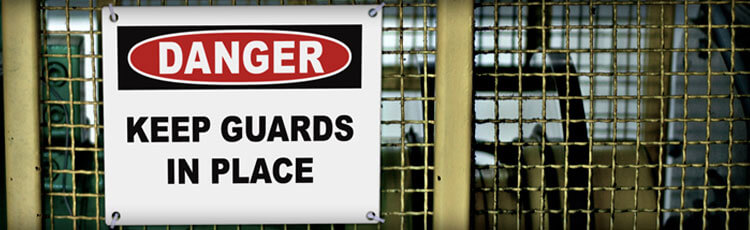
Cutting Corners on Machine Safety a Common Problem
Machine guarding violations are consistently among the OSHA top 10 violations. There are several common ...
Read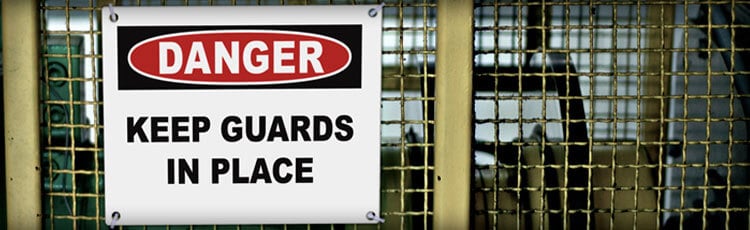
Worker Injuries Have Long-Lasting Effects
When a worker is injured on the job, the effects go beyond a simple report. Incidents can make tremendous ...
Read