OSHA Signs Regulations and Compliance: Everything You Need to Know
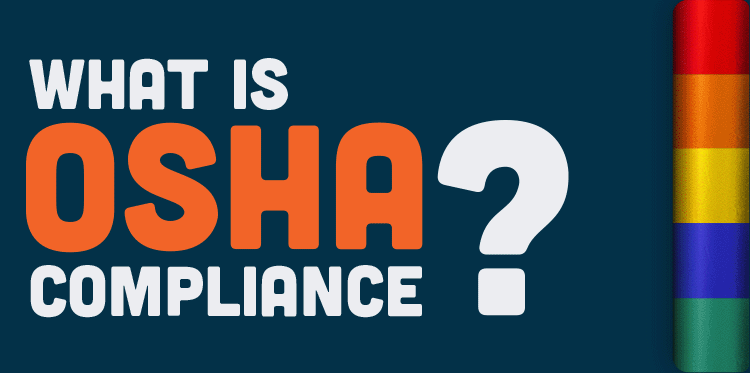
Navigating the occupational safety and health environment can feel like wading through a minefield. When dipping your toes into regulations, a vital area to watch is how to comply with OSHA for signage. For safety professionals and facility managers, staying on top of these regulations ensures a safe and responsible work environment. Here is a comprehensive list of the top 10 OSHA signs compliance factors you need to be aware of:
Overview of Regulations for OSHA Signs
Understanding the purpose and scope of OSHA signage regulations is crucial. You may ask yourself, “what does OSHA do?” OSHA uses signs to convey crucial information and instructions to workers who may be exposed to various environmental hazards. These signs need to be highly visible and provide clear and easily understood messages which can effortlessly be made by the DuraLabel Kodiak Max Industrial Sign and Label Print System.
Four main types of OSHA-mandated signs include:
- Danger Signs: Indicates that a hazard is present and that it may result in death or serious injury.
- Warning Signs: Indicates a hazard that may result in death or serious injury, but the message is less severe than for danger signs.
- Caution Signs: Indicates a hazard that may result in minor or moderate injury.
- Safety Instruction Signs: Provides information regarding health and safety procedures and precautions that do not pose a risk to personnel.
OSHA Labeling and Sign Requirements
OSHA has specific requirements regarding the design, format, and wording of safety signs and labels. These requirements are meant to ensure consistency and usability across different work environments.
You can create effective OSHA signs and labels once you have a clear understanding of the environment they will be in and the types of hazards that may occur there. Like selecting the right tools for the job, sometimes off-the-shelf signs may suffice, but custom designs are often needed to address unique hazards and operational contexts.
Key requirements that signs should include:
- Convey the right degree of hazard severity— Although the American National Standards Institute (ANSI), a private non-profit organization that oversees the development of voluntary consensus standards for products, services, processes, systems, and personnel in the United States, it is not a requirement, however, they are widely utilized to set industry standards and best practices. Utilizing ANSI standards can enhance safety sign comprehension. ANSI’s symbols serve as a universal language and aid untrained individuals in being able to obtain the message quickly.
- Use signal words—Words like "Danger," and "Caution" are considered signal words, and they are often associated with specific and consistent color codes. Examples of these words in action are red for fire-related hazards.
- Include clear symbols and messaging— Well-constructed safety signs are more than just words and symbols. They are a communication tool that ensures that the message is clear and readily comprehensible.
OSHA requires labeling hazardous materials in the workplace to improve safety. HazCom 2012 was created utilizing an international system from the United Nations called the Globally Harmonized System of Classification of Labeling and Chemicals (GHS), with the idea of providing workers with awareness of what chemicals they were being exposed to.
OSHA allows a bit of wiggle room with the signage requirements by allowing those responsible for creating them in their workplaces to create custom signage as long as they follow industry standards to meet their OSHA Hazcom labeling requirements. For example, the National Fire Protection Association (NFPA) diamond labeling system, or Hazardous Materials Identification System (HMIS) both meet those requirements. If either of these systems are used, any information unaccounted for must be addressed.
Color Coding for Clarity and Comprehension on OSHA Signs
Color associations register in the brain before words on signs can be mentally processed. Color markings were designed to improve response time, which ultimately decreases the likelihood of incidents, even from a distance. Color coding does not override the need to follow any other compliance standards and signs must not create a separate hazard that results in trips, head injuries, or cuts, scrapes, and bruising.
Color is a critical aspect of OSHA signs and labels. OSHA mandates specific colors for different types of hazards:
- Red — Designed for "danger" and is the most serious type of hazard that can result in death or serious injury to a worker. This color is often used for fire prevention devices, items used to stop a machine or process.
- Orange — Designed for "warning", a hazard that may result in injury or death if not properly avoided.
- Yellow — Designed for "caution", or “hazard”, and is used to alert workers to hazards that may result in minor to moderate injury. This color people will often see at traffic lights, crosswalks, and other areas where hazards may occur.
- Blue— Designed for "notice," and to be informative, but does not allude to threats of injury if not followed.
The NFPA created a diamond label that is broken up into four colored and numbered quadrants. Each color and number represents the level of hazard severity. The label must include a product identifier and employees must receive training in the specifics of the hazards associated with the chemicals.
HMIS is a color chart created with four colors that represent hazard information. Similar to NFPA’s diamond label, HMIS also assigned a number to three of the colors and then provided some additional information in the last box specific to personal protective equipment (PPE).
Employing proper color-coding promotes safety by warning employees and visitors of possible risks and enhances the overall understanding and response to hazards.
Consistent and Updated Signage Across All Facilities
Consistency across signage is important. It ensures that any employee can recognize the symbols and know what to do in the event of an emergency. This entails having a standardized system of signage in place and updating OSHA signs and labels as necessary to reflect changes in procedures or regulations. For multi-site facilities, it's crucial to conduct regular audits to guarantee that all locations are using the same sign standards.
The same regulations do not apply to every department. Different teams perform different duties, use different tools, and have different risk levels. Due to department differences, documentation and communication should be a priority.
When it comes to employees working on equipment that has the potential for electrical shock, it is important for employers to know where these types of electrical hazards can occur, so proper signage can be placed in those areas to warn employees.
OSHA 29 CFR 1910 Subpart S, regulations state that "Safety related work practices shall be employed to prevent electric shock or other injuries resulting from either direct or indirect electrical contacts..." Employers are responsible for:
- Creation of a facility electrical safety plan
- Documented training in electrical and arc-flash safety, for both electrical workers and any affected workers
- Conduct an arc flash hazard analysis
- Distribution of personal protection equipment (PPE) to impacted workers
- Placement of OSHA warning labels on equipment
- Provision of proper tools for safe electrical work
- Annual inspection to verify employee compliance
When referencing safety signs and labels, OSHA does not require the NFPA standards, but they often use their standards as guidelines for general rules and regulations.
However, OSHA’s §1910.303 requires employers to mark electrical equipment with descriptive markings, including the equipment's voltage, current, wattage, or other ratings as necessary, in order to meet OSHA electrical panel labeling requirements. OSHA recognizes arc flash hazards as a serious threat to worker safety and refers to NFPA 70E standards as the solution for that hazard.
According to 29 CFR 1910.145(f)(4), it requires the sign's signal words like "Danger,"and "Caution," to be readable from at least five feet away. Signs should be placed in a way where workers are aware of the hazard and able to respond appropriately prior to exposure.
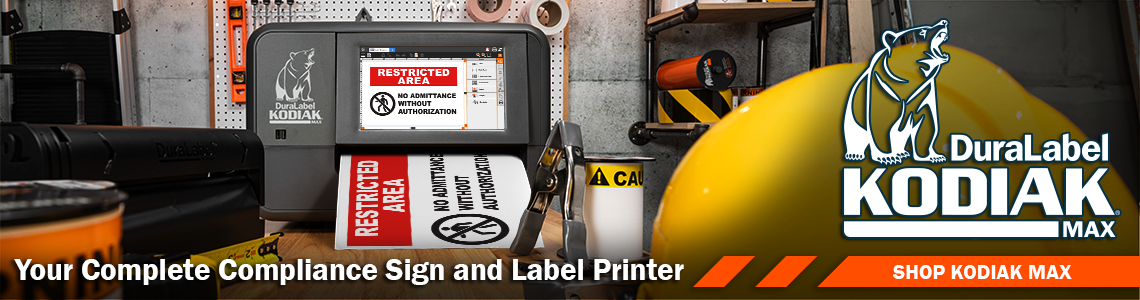
Placement and Visibility of OSHA Signs and Labels
The most clear and concise sign is ineffective if it is not seen when needed. Signs need to be placed in appropriate locations – which means they must be highly visible to the employees in the area.
According to OSHA’s rule for when and where signs should be placed. 29 CFR 1910.145(f)(3) states safety signs, labels, and tags “shall be used as a means to prevent accidental injury or illness to employees who are exposed to hazardous or potentially hazardous conditions, equipment or operations which are out of the ordinary, unexpected or not readily apparent. Tags shall be used until the identified hazard is eliminated or the hazardous operation is completed.”
Once the safety signage is determined necessary, those signs must be placed close to the nearby hazard. OSHA said safety signs should not produce a hazard, meaning they should not have sharp edges, splinters, or block the view of incoming traffic. Corners should have rounded or blunt corners.
Visibility also pertains to the font size and the contrast between backgrounds and letters, ensuring that signage is not only seen, but can be read easily from a distance under various lighting conditions.
NFPA 70E is the standard followed in the United States to encourage safe electrical work. These NFPA guidelines define three protective boundaries specifically around electrical equipment.
- Arc flash boundary— Designed to protect workers from burns if such an accident occurs by creating a safe distance from the worker to the charged equipment, based on if the Incident Energy of an arc flash would be 1.2 cal/cm.
- Limited approach boundary— Designed to protect workers from electric shock. Trained personnel may cross this boundary and escort untrained workers through the area.
- Restricted approach boundary—Designed to protect workers from electric shock. Workers who have been trained may cross this boundary. There are additional requirements for workers in these areas, which include a specific plan of action, a list of protective steps to be taken, and supervisory approval.
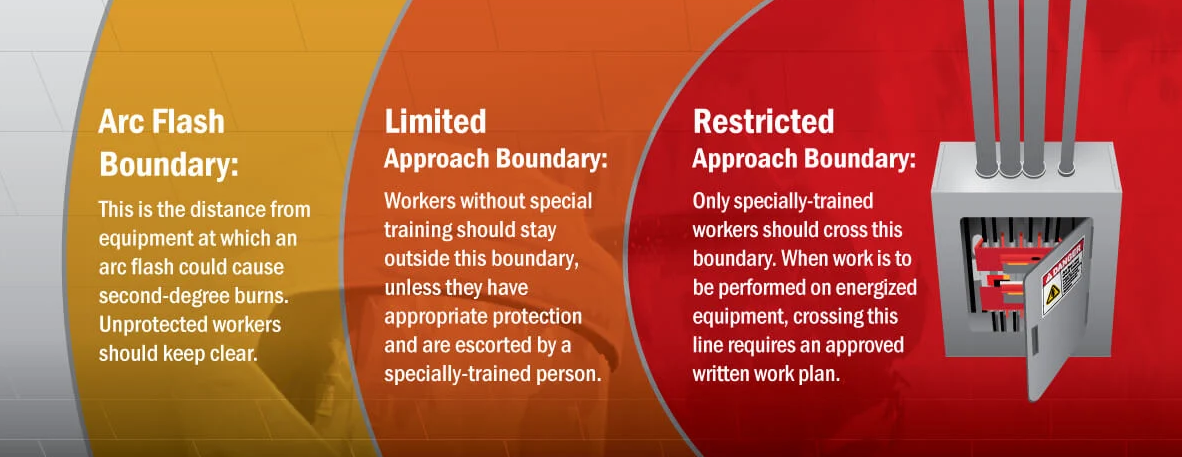
In terms of narrowing down arc flash boundaries, performing an arc flash hazard analysis is designed to determine the location and severity of arc flash hazards and to suggest appropriate courses of action to minimize them. IEEE 1584 provides a formula for conducting an arc flash study. Other methods exist as well, including calculations based on the formulas presented in NFPA 70E. Various methods have been used for the study and produced similar findings.
The data collected and calculated during the study is put to various uses that include:
- Printing OSHA warning labels for equipment
- Determining required PPE
- Training workers
Discovering where the boundaries are is a crucial step to preventing death from an arc flash occurrence. The arc flash boundary will not prevent an incident, but it can minimize the severity of damage should one occur.
Similar to electrical hazards, when dealing with chemical hazards, place hazard warnings, operating information, and safety reminders in a place where workers can easily view them. Low-charge anhydrous ammonia is a favorite for manufacturers, suppliers, and end-users in refrigeration and HVAC, because not only is it one of the safer chemicals for workers to handle, but it is also cost-effective and efficient in small quantities.
However, just because it is safer does not mean risk assessments, emergency planning, or safe ammonia management should not be implemented. According to the Centers for Disease Control and Prevention the top five chemicals causing injuries in acute incidents:
- 2,364 carbon monoxide
- 1,153 ammonia
- 763 chlorine
- 326 hydrochloric acid
- 318 sulfuric acid
HMIS, developed by the National Paint Coatings Association (NPCA), now known as the American Coatings Association (ACA), employs color bar labels to signify and convey information about chemical hazards. The number ratings range from 0 to 4.
Each color represents a different description:
- Blue — health hazard
- Red — flammability
- Orange — physical hazard
- White — personal protection
Complementing HMIS, OSHA signs play a pivotal role in alerting individuals to potential dangers and safety protocols within workplaces.
Three HMIS standards have been issued by NPCA. For the HMIS I and II standards, the criteria for the numerical values in the red bar are the same as for the NFPA diamond. For HMIS III the criteria are the OSHA label standards.
Multilingual OSHA Signs
There are over 350 languages spoken in the United States, according to the US Census Bureau, with some of the most widely spoken being Spanish, Chinese, Tagalog, Vietnamese, and Arabic.
It is important to be able to effectively communicate with your employees, and in industries like health and safety, the demographics vary significantly from industry to industry. The demographics across all sectors of the health and safety industry comprise of:
- 62% White
- 7% Hispanic or Latino
- 1% Black or African American
With many companies seeking workers from vast cultures and backgrounds, language barriers are a common occurrence. Language barriers can lead to miscommunication, decreased productivity, and difficulty during group collaboration.
A good way to fix the language barrier issue is to create a level playing field with proper signage in the languages spoken by workers at your facilities. OSHA recognizes that language can be a safety barrier and requires that signs must be posted in both English and the primary language spoken by the workforce if English is not the primary language. This extends to phrases like, "Keep Out," "Fire Exit," and "Danger" to maintain the same level of comprehension and safety communication.
Bilingual OSHA signs and labels make information accessible to a wider audience. They cater to speakers of both the dominant language and minority languages, ensuring that everyone can understand important messages, instructions, and information. For workplaces where employees speak multiple languages, multilingual signage is helpful.
When creating signage, OSHA often looks to the ANSI for guidelines. ANSI Z535.1 sets forth the technical definitions, color standards, and color tolerances for safety colors, while its extended version ANSI Z535.2 regulates requirements for design, application, and use of safety signs in facilities.
Multilingual sign layouts are generally formatted such that a safety pictogram symbol panel is positioned, so it is clearly associated with and shared by both the first and second language headers and word message panels.
When it comes to guidelines for multilingual signage, there is no difference between the guidelines for any other type of safety signage.
Clean and Maintained Signage
A cluttered or grimy sign can be just as dangerous as no sign at all. For signage to be effective, it must be clean and in good condition. Employees can receive a false sense of safety when signs are damaged, broken, illegible, and outdated.
Regular maintenance should be part of routine safety checks to ensure signs remain an accurate and reliable source of information for workers. You should keep a record of the installation, inspection, and replacement of safety signs for reference and compliance purposes.
Signage with Employer Information
In certain situations, OSHA regulations also demand that signs include the name, address, and telephone number of the employer responsible for the work. This ensures clear lines of communication for emergencies and helps in identifying and addressing specific workplace hazards and their prevention.
Implementing Digital Signage Systems
In a world that has become increasingly more digital, it is not a bad idea to consider digital signage solutions. These types of signs can replace physical signage in some instances by offering dynamic and immediate updates to information where physical signage cannot.
A digital system also provides the flexibility to include more detailed and variable information, such as:
- Real-time threat assessments
- Changes to operating procedures
- Updated information across the facility
However, it's crucial to consider the potential for technology failures, and ensure there are backup systems in place and that the digital signs are placed in areas where they are as noticeable as traditional OSHA signs and labels.
Staff Training and Familiarity with Signage
OSHA requires employees to be familiar with the meanings and applications of the safety signs in their workplace. This can be achieved through thorough NFPA 70E training and ongoing awareness programs.
Employers should train all employees on the signs they use in the workplace, including:
- Sign type — Workers may be working with various types of hazards that can include chemical and electrical, so knowing what these OSHA signs look like, and the content provided, will help them recognize potential hazards and what to do to avoid them.
- Specific hazards — Not all hazards should be treated the same. Some require special PPE to even share the same space with them, while others require the worker to keep their distance.
There are OSHA signs and labels for various industries. When it comes to hazard communication, employers and employees need to be trained on the Safety Data Sheet (SDS), because they need the information provided on those sheets to protect themselves from hazardous chemical exposures and to work safely with chemical products.
According to OSHA’s HazCom requirements, an SDS sheet must be given:
- Within first shipment of materials to recipient
- When significant new information has been identified
- When the recipient requests the sheet
Periodic reviews and evaluations can help ensure that employees are maintaining their knowledge and are responding to signs appropriately. Compliance with OSHA's signage rules is a vital part of maintaining a safe and healthy work environment. By ensuring that each of these areas is addressed, you not only fulfill regulatory requirements, but you also significantly enhance the overall safety and well-being of your team.
OSHA Signs with DuraLabel Resources
OSHA signs can provide workers with important safety instructions and guidelines based on the facilities they are in. For instance, signs remind workers to wear protective gear, such as hard hats and safety glasses, or to watch out for specific hazards, such as heavy machinery or heavy traffic areas.
Whether you need safety signs, pipe markers, or equipment labels—Toro Max and Kodiak Max are ready to transport anywhere you are. Get help crafting a system that will provide the safety communication you need. Call 1-888-902-2148 and one of our experts will guide you through the process.
Learn more about how to stay up to speed on hazard communication messaging that can be used to help create a safer environment that leaves workers at ease knowing management cares. Download our free HazCom Instant Action Guide today.

Read Next:
Guidelines for OSHA's Fall Protection Standards & Compliance
Related Resources

OSHA and Workplace Safety: A Right for Every Worker
The U.S. Bureau of Labor Statistics (BLS)shared its workplace fatality statistics for 2022. The bureau ...
Read
Creating Compliant OSHA Signs: Tips and Best Practices
What are the Benefits of CreatingOSHA Compliant Signs and Labels? Creating compliant Occupational Safety and ...
Read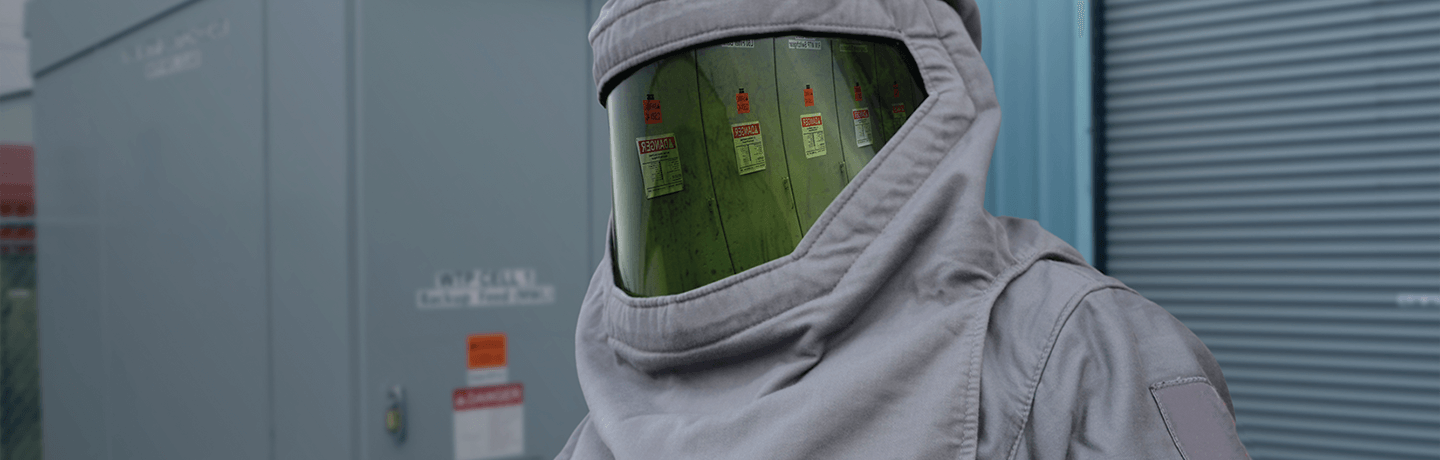
NFPA 70E Arc Flash with OSHA Signs
What is NFPA 70E? NFPA 70E, or the NFPA's Standard for Electrical Safety in the Workplace, outlines specific ...
Read