Lean Manufacturing and the 5S System
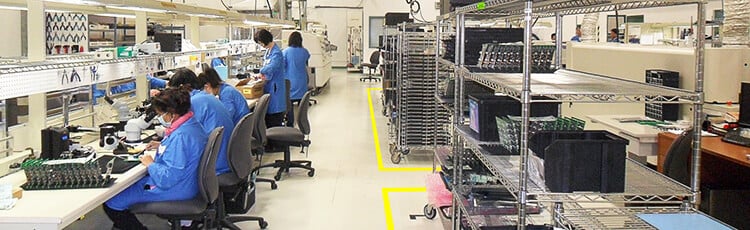
What is 5S in Manufacturing?
5S is a lean manufacturing method used to eliminate waste, improve workplace efficiency, and create visually organized environments. It includes five structured steps—each starting with the letter “S”—designed to build sustainable, productive workflows.
How does 5S work in real-life workspaces?
Look around you. Is your desk a little cluttered? Is there something nearby that is not necessary for your space? A half-eaten muffin, a few piles of paperwork, a wall of sticky notes, and maybe the TV remote somewhere.
Now, think about your work as a whole. Do you have unnecessary items in your workspace? What about the warehouse or shop floor? Are some items in the wrong place, unorganized, or not even needed?
Having items that are in the wrong place, unorganized, or unnecessary contributes to downtime and waste, and lowers worker efficiency. However, a simple method can improve things dramatically: The 5S System Explained.
What are the five steps of 5S?
The 5S system is a lean manufacturing tool that improves workplace efficiency and eliminates waste. There are five steps in the system, each starting with the letter S. These steps feed into each other, so the sequence is important.
- Sort (seiri 整理)
- Set in order (seiton 整頓)
- Shine (seiso 清掃)
- Standardize (seiketsu 清潔)
- Sustain/self-discipline (shitsuke しつけ)
How does each step in 5S support the next?
Clearing out unnecessary materials in step 1 (Sort) will provide the space needed to organize the important items in step 2 (Set In Order). Then, once the workspace is de-cluttered and organized, dirt and grime can be removed in step 3 (Shine).
These changes to workers’ job duties and work environment should be reflected in updated procedures through step 4 (Standardize). Finally, those new procedures won’t amount to much unless the responsibility is assigned and progress is tracked—as required for step 5 (Sustain). And with responsibility and tracking, workers will continue to apply the steps, returning to step 1.
Why is 5S important for workplace productivity?
5S provides a systematic framework for visual workplace organization and cleanliness. It helps facilities avoid lost productivity from delayed work or unplanned downtime. DuraLabel customers like Ruby Rusine, of Social Success Marketing, attest to the organizational power of the 5S Method.
“Clutter definitely affects productivity. Less is more,” said Ruby Rusine of Social Success Marketing. “I can, surprise, think better when there is less stuff on my table or less tabs open. However, some people thrive with clutter around. I live with one here.”
How to Sustain 5S in Lean Manufacturing Programs
There are some helpful tools for 5S lean manufacturing that can make the process easier. These tools include process tools, 5S checklists, and visual communication tools like labeling and floor marking supplies.
“I find labels to be super helpful.” Rusine said.
5S can be used in any industry. Why do you think it would or wouldn’t work in your workplace? How can your facility get started with 5S? 5S can fail sometimes if there is no worker/top-level buy-in. There also needs to be a commitment to make 5S a long-term success. Be sure to track the details of the cost-savings from 5S. For some businesses, Sustain seems to be the hardest step. Manage strategies for sustaining 5S practices and maintaining focus.
“There is the word commitment to sustain this,” said Rusine.“This is a great habit to carve because the cue or the motive is right. I need to change my routine to improve on getting my table clutter-free from one day to two days.”
Free 5S Resources and Tools
Need help? Download our free 5S System Best Practice Guide or a free 5S Color Code Chart to help you start or sustain your 5S program with actionable 5S implementation tips.
Related Resources
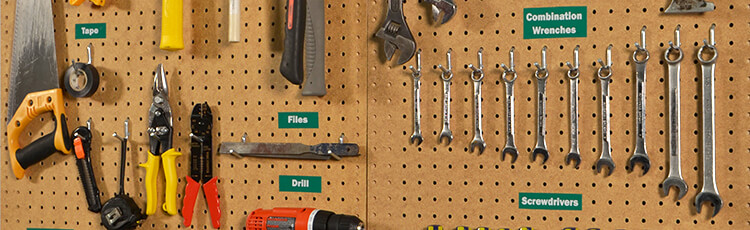
Tools for 5S Lean Manufacturing
The 5S systemis a lean manufacturing tool that helps to clean and organize the workplace, as well as improve ...
Read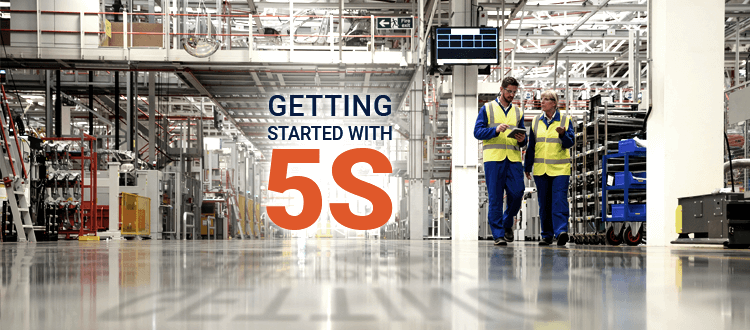
Getting Started with the 5S Methodology
What Is 5S and Why Does It Matter for Visual Organization? Staying on top of operational efficiency is an ...
Read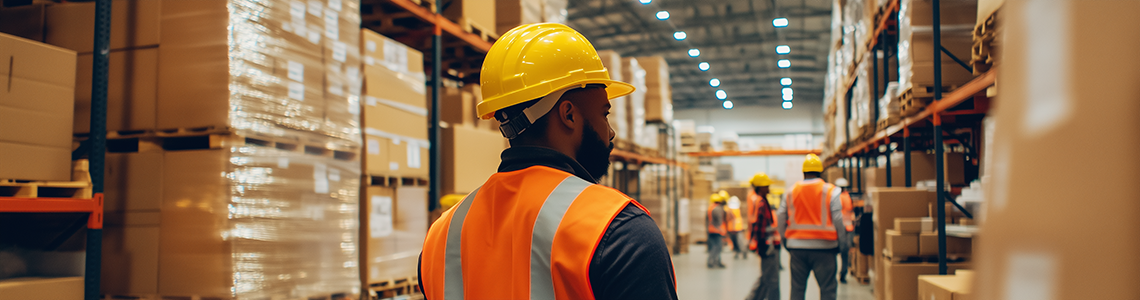
How to Build a 5S Implementation Team for Lean Success
What is a 5S Implementation Team? A 5S implementation team is a group of individuals empowered to make quick ...
Read