Getting Started with the 5S Methodology
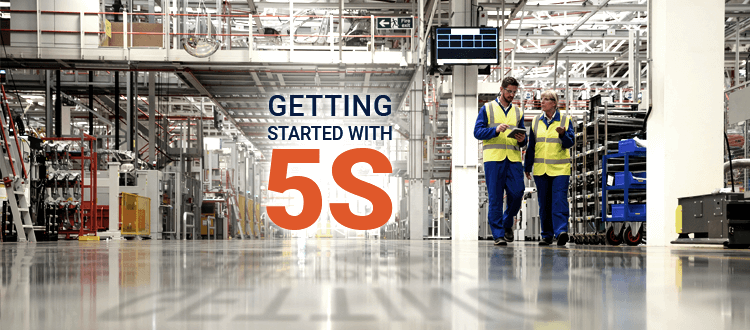
What Is 5S and Why Does It Matter for Visual Organization?
Staying on top of operational efficiency is an ongoing challenge, and getting started with 5S can be a game changer when done right. The 5S methodology is a proven Lean process that brings structure, consistency, and visual organization to the workplace. Whether you're upgrading your facility with automation or simply reorganizing the shop floor, 5S provides a framework to guide those improvements effectively.
From floor tape to custom signs, 5S labeling and marking tools help streamline operations, reduce waste, and improve communication. These visual factory tools support a cleaner, safer environment while helping teams standardize tasks, reinforce expectations, and drive long-term efficiency across the organization.
Aligning 5S Participation & Buy-in
Buy-in from management is essential for 5S implementation to take hold. Getting people to change the way they've always done things isn't easy, and it's a common root cause for new methods failing. Visible support and commitment from line managers will set the tone for a successful 5S system. Give 5S momentum by promoting it in the workplace through engaging ways including:
- Sharing success stories, testimonials, and before-and-after pictures from other companies. For instance, Toyota in Japan decreased overall assembly time by about 10% after adopting 5S, underscoring the substantial benefits organizations can achieve through active participation and buy-in to lean methodologies.
- Having a group or several groups of employees visit a company like Toyota to see the benefits of 5S and other lean programs.
- Having an expert come in to present 5S to your entire company. For example, a study by the California Health Care Foundation (2015) showed that Ravenswood Family Health Center significantly improved operational efficiency and patient care by implementing lean methodologies, including 5S. These improvements included streamlined workflows, reduced patient wait times, and higher employee engagement, underscoring the importance of organization-wide commitment to lean practices.
Next, show how the 5S principles can improve efficiency on a small scale by implementing it in an area where employees can see the process and transformation from start to finish. Choose an area that has a history of issues with productivity, organization, or quality, like an office or part of the shop floor. Map out the area's workflow, note how long tasks take to complete and take photos to document progress. Employees will see the physical transformation and actual improvements the system has on overall efficiency. Next, start establishing shared goals to work toward as a workforce.
Identifying Improvement Areas and Setting 5S Goals
5S process introduction will look different in every facility because the needs, processes, and culture vary in any given workplace. The goal is to engrain the steps of the 5S process in the day-to-day work long after the initial implementation. Identify measurable goals that will help keep your employees and program on track. Examples of common 5S goals to measure include:
Reduction of shipping times
Reduction of material handling
Improvement in the flow of materials throughout the workplace
Reduction of labor costs per project
Improvement in product quality (reducing the number of defects or rework)
These small improvements over time are inexpensive to implement, in part because many ideas result in eliminating processes instead of adding them. Let employees take the lead of their work by asking for input on ways to improve processes and how to make their jobs easier. This will allow them to directly experience the value of the changes and recognize how their efforts contribute to the common goal. Once everyone understands the goals of the system, consider various process tools that will be helpful to identify problem areas in the workplace.
sing 5S Methodology Tools for Improvement
Several 5S process tools including checklists, audits, and organizational problem-solving methods can help highlight problems in various work areas and work to continuously improve them.
5S Checklists
Promote consistency and performance improvement by keeping a general 5S housekeeping checklist for each work area. Checklists help break down 5S tasks into manageable duties and keep everyone connected with each step in the process. To create a successful checklist, organize them by each of the 5S steps.
Break down the work by when it should be accomplished and what else needs to be done before certain tasks can be st1arted. Include specific details for each task so they are more trackable, such as "Create a red tag area for unnecessary items" instead of something vague like "Sort work area." Hold everyone accountable by establishing a 5S team with worker-led routine checks so employees coordinate and collaborate. Other common types of 5S checklists that can help keep your program focused include:
5S Audit Checklists: An audit checklist will help keep your program on task by making it easy to track improvements and areas that can use additional improvements. Each department should make its checklist to best meet its needs.
Trend Charts: These charts show trends in data over time. Trend charts help managers keep track of changes in processes, outputs, and much more. These charts can help you quickly identify areas or processes that need to be improved, as well as processes that will need to be improved in the future.
Preventive Maintenance Checklists: A preventive maintenance checklist ensures that maintenance is done on time and new maintenance requirements are known. Preventive maintenance is what keeps operations running smoothly to prevent unexpected downtime.
Plan-Do-Check-Act (PDCA) Cycle for the 5S System
The Plan-Do-Check-Act (PDCA) approach is a simple four-step method that's made to help continually improve processes, avoid recurring mistakes, and support the 5S principles. PDCA is a powerful counterpart of the 5S system because it ensures that each step in the process is applied to address specific problems. Using a PDCA template, workers won't simply begin removing tools and organizing equipment without first creating a plan to ensure the change will be positive.
Plan: In this first step, identify an area that needs improvement then develop a plan with workers from other areas that may be affected by any change.
Do: Implement the 5S in a pilot area so it does not disrupt the workplace. Keep track of what has been done and its impact.
Check: Review the change and its impact. Did the change produce the expected results? Did it impact any areas or processes that were not supposed to be affected?
Act: If the change produces an improvement, begin incorporating it throughout the facility-one area at a time. If the improvement does not work in other areas, identify gaps and restart at the ?Plan' phase for those areas.
Each change will help make work easier, reduce costs, and improve quality throughout the workplace.
Visual Management Tools and Supplies for 5S
More than half of the brain is devoted to processing visual information. Visual management uses instinctive visual cues to communicate key information about performance, expectations, standards, and warnings in the workplace. The goal is for everyone to see and understand the current state of work, navigate areas, and track progress at a glance, even if they aren't familiar with the facility. Various types of visual management boards are commonly made for continuous improvement, project status, and point-of-use tools for a visual workplace. Visual management provides transparency between management and workers to communicate and align your organization.
Labeling and marking are key to visual management and have an important, foundational role in 5S. Labeling helps streamline organization and efficiency by identifying items and their proper locations. A successful 5S system will require the right visual communication supplies.
Before you begin, do a walkthrough of your facility to assess existing identification. It's important to consider the conditions your visuals will face in the work environment, including the types of surfaces, extreme temperatures, chemicals, moisture, and more. Choosing the right material and strength of an adhesive is critical to ensure visuals remain intact and legible long term. Here are the most effective ways to incorporate signs, labels, tags, and floor marking to support 5S functions.
5S Signs & Labels
Determine where and when people need information the most. Look for outdated and damaged signs and labels that need replacing, missing signage, and where additional visuals could be added to help increase understanding or awareness. Common visual factory examples that use 5S labels and signs include:
Organization and general identification
Organize and identify items in the workplace using labels with text, numbers, symbols, and barcodes. Mark locations of inventory on shelving, bins, and storage units. Communicate startup, shutdown, inspection, and other important information on machinery and equipment. Include labels with additional information like maintenance details at the point of need. You can quickly and easily install a variety of safety notices and warnings that meet OSHA general safety standards using premade safety signs and labels.
Site-specific hazards
Since every facility and work area will have different needs, draw awareness to site-specific hazards and procedures, especially for those who may not be familiar with the facility. Utilize custom banners and signs with images, symbols, and other visual components to help messages quickly resonate with employees. Address hazards that may require extra attention, like PPE reminders before entering certain work areas.
Tags
Make it easy for employees to identify the status of tools, supplies, and equipment with bright red tags. These are a helpful way to communicate items to discard, put in storage for later use and where they can be stored, and to identify the location of items so employees know where to return them.
When new work improvements and modifications are made, update labels and signs to reflect changes. Get a general overview of key areas in a typical facility to cover and the supplies you'll need with a handy facility visual communication checklist.
Floor Marking Supplies to Support 5S
Floor marking is a quick and easy way to support your overall safety program and improve the workflow. Multipurpose floor tape is ideal for accomplishing a variety of organizational tasks that align with these lean principles. Mark aisles, hazard boundaries, and color code. Here are the most effective ways to use floor marking to support 5S:
Wayfinding
Help everyone easily and safely navigate the workplace and locate important safety equipment and areas like eyewash stations, fire extinguishers, and emergency exits using floor signs, shapes, and bold-colored lines. Improve visibility and traction in indoor and outdoor areas like loading docks and stairs with reflective and anti-slip floor tapes.
Color-coding
Create a cohesive color-coding system that compliments your facility signs and labels. Mark a variety of items, areas, and surfaces like walls, pipes, equipment, and work areas or boundaries. Apply bold-colored tapes to designate work areas so employees can quickly identify their purpose, such as various stages in the QA process and inventory and storage locations. Organize and design tool shadow boards with colorful tape and mark tools with colors that correspond to the work area to which they belong.
Pro Tip: Here are a few traits of successful shadow boards:
- Clear: Shadow boards should clearly indicate, through both background "shadows" and text, which tools go in each position
- Accessible: Shadow boards should be placed in a common area where numerous workers can access the board, move freely, and easily see what's missing
- Clean: Shadow boards reduce clutter and offer plenty of space, so workers can quickly see which tools are stored on the board
Traffic Flow
Guide vehicle operators and pedestrians safely throughout the facility using aisle marking tape and printable floor tape for directional arrows. Mark off certain areas to caution against a specific hazard. Alert to speed limits, crossing areas, and restricted areas with floor signs. Designate locations for equipment storage and parking for forklifts. In areas with constant foot and vehicle traffic, use a heavy-duty aisle marking tape for long-term use.
To execute all of your 5S visual needs, investing in an on-demand labeling system will allow you to quickly and easily maintain visuals and print in bulk when work processes change. Updating visuals is crucial to sustaining the 5S methodology and your visual management strategy.
Industrial Labeling Systems for 5S
An in-house industrial printing system—like the DuraLabel Kodiak Max Industrial Sign and Label Print System—is a cost-effective solution that gives you the freedom to tackle a wide range of facility labeling projects at your convenience. In addition to 5S labels, you can produce signs for a variety of needs to meet popular regulatory requirements for arc flash labeling, GHS/HazCom 2012 chemical labeling, pipe marking, and more. Labeling design software makes it that much easier and more convenient to produce the signs you need on various supplies. Have the ability to design and print custom labels from scratch or utilize premade templates to create standardized labels that meet regulatory requirements.
Sustaining 5S in Your Facility
The 5S process is continuous and there will be trial and error on the way to achieving your goals. Practicing each of the five steps of 5S each day and identifying corrective actions will bring real change over time. You will start to see improvement in productivity, cost savings, and employee morale and profitability. As your goals and priorities change, you can strengthen your 5S system by putting Sustain into action with a comprehensive 5S Quick Start Guide. This is an excellent training tool with sample evaluations and other tools to measure success.
Improvement steps you discover can open the door to more open communication and feedback. Workers may be more prone to speak up about issues and improvements to prevent downtime down the road. Regular support and reassurance from management to workers will always be crucial to help better visualize goals and feel they are achievable.
Take Action Today
Want to learn how to apply 5S labeling and marking in your facility? Call us today at 1-888-788-9936. One of our experts will help you integrate visual factory tools into your workflow using proven Lean strategies and DuraLabel industrial labeling tools.
You can also use our free 5S resources, such as guides webinars like implementing 5S in your workplace. Understand how to apply each of the five steps into your unique space, how they tie together, and products to help form a cohesive program.
Read Next:
Related Resources
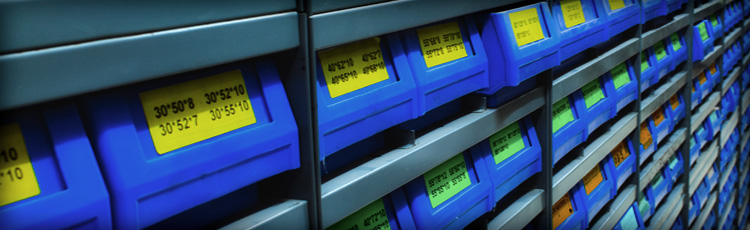
Creating a Visual Factory with the 5S System
What Is a Visual Factory with the 5S System? The term "visual factory" refers to an approach to lean ...
Read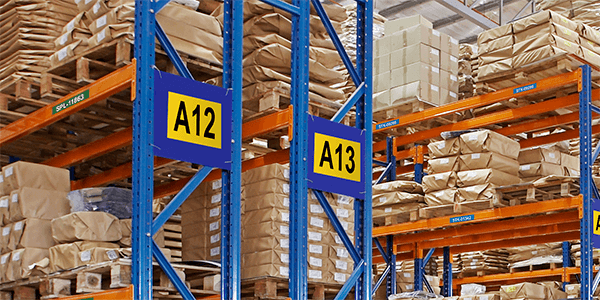
5S Examples in Action: The Good, the Bad, and the Successful
Can 5S Improve Efficiency and Engagement Across Industries? The 5S systemis a proven method for improving ...
Read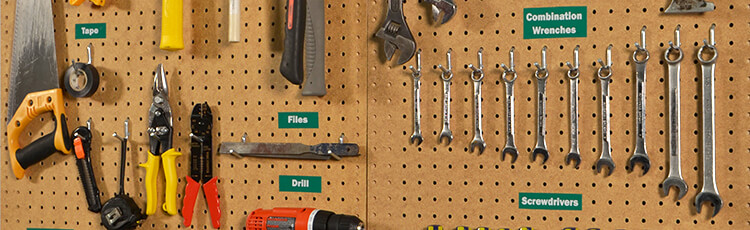
Tools for 5S Lean Manufacturing
The 5S systemis a lean manufacturing tool that helps to clean and organize the workplace, as well as improve ...
Read