Performance Improvement Plan
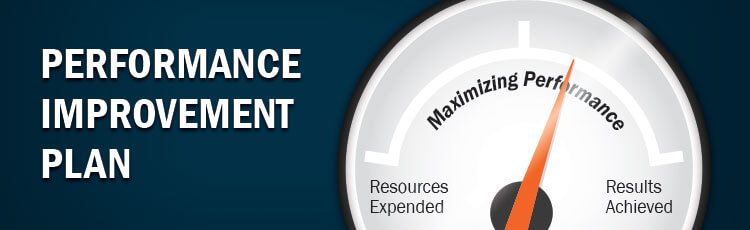
Performance is the level of achievement reached under defined conditions. Performance improvement means achieving those results more efficiently, achieving better quality results, or producing more of the same result (greater quantity). A performance improvement plan is an approach to help achieve any of these results and do so whether it is the performance of an athlete or the performance of an industrial process that needs improvement. In this case, we'll be looking at creating a performance improvement plan in a business setting.
Performance Improvement Plan For Maximizing Performance
Performance is a measure of the results achieved. The objective is to maximize performance using the minimum amount of resources. How well this is accomplished is called performance efficiency, and it is measured by the ratio between the resources expended and the results achieved.
There is a theoretical limit on how much performance can be improved. The difference between current performance and the theoretical limit is called the performance improvement zone. Reducing the size of that zone, by improving performance, is accomplished through a performance improvement plan.
Performance improvement plans are best known as an approach for improving the performance of individuals. But performance improvement plans can be used for processes, projects, work teams, departments, or entire organizations. However, the greater the number of people covered by the performance improvement plan, the more complex it becomes. When implementing a performance improvement plan at group and organizational levels, it is very helpful to keep in mind the words of Field Marshal Ferdinand Foch from the first World War: 'No plan survives contact with the enemy.' The complex realities of organizations with their internal inter-relations combined with the highly changing external environment in a steadily globalizing economy make 'dead accurate and thoroughly complete' performance plans at group and organizational levels an unachievable ideal. The larger the entity of focus, the greater the flexibility required for success when implementation begins.
Improving Performance
The first step is to set goals. The goals should be realistic, achievable, and measurable. Next, determine what will be done to achieve those goals. This is easy to say, but how do you determine what needs to be done?
A common approach to identifying what needs to be done is using lean manufacturing techniques such as 5S, Kaizen, TPM, SMED, and Kanban to determine inefficiencies. Lean techniques are based on eliminating waste and focusing on activities that deliver value to the customer. The result is improved performance.
For example, Kaizen involves using employee suggestions for small ways to make improvements. The process of improvement is continuous, resulting in the cumulative effect of many small improvements quickly adding up to significant results. In this way, Kaizen generates multiple answers to the question "what do we need to do to improve performance."
As the quote above points out, creating a large performance improvement plan, addressing performance objectives throughout the company, usually runs into problems and may quickly be derailed. Kaizen solves this problem by using continuous small changes instead of attempting a few major changes. Let's look at some other advantages of using Kaizen to drive performance improvement.
The Kaizen Performance Improvement Plan
To create a major performance improvement plan requires identifying problems, analyzing those problems, identifying solutions, implementing the solutions, and finally evaluating the results to determine if the problem was fixed. When done on a large scale, with costs usually in the millions of dollars, careful (and costly) upfront analysis and evaluation is critical to ensure the large investment will have a good ROI. In addition to the cost, an extensive amount of time and man-hours are required. In the end, it may take several years to complete the performance improvement project, and in the end, the result still may not be as planned.
Kaizen provides a better way that reduces costs and speeds the implementation of changes that result in significant performance improvement. Instead of a single, large overall performance improvement plan, Kaizen is a continuous process of small changes. Using suggestions from employees, small improvements are identified and quickly implemented. Since changes are made in small steps, if changes result in an undesirable outcome, the problem can be quickly identified and corrections made.
How Are Large, Critical Problems Addressed by Kaizen?
Not every performance problem can be addressed through a series of small changes. What if your competitors are beating you on the price by 20%? On top of that, they are producing better quality and shipping orders faster. You'd like to get back in the game. So what do you do? A Kaizen Event, or Kaizen Blitz, is the Kaizen approach used to make significant changes quickly. What it does is use a multidisciplinary team, typically brought together for less than a week that is targeted at solving a specific problem. The team will have goals such as:
- Create 80 to 100 productivity-increasing ideas, with an 80% implementation rate
- Decrease die change times by 50%
- Reduce inventory by 33%
- Decrease defects by 90%
- Identify and implement at least 10 safety improvements
During the week the team may come up with 100 to 150 changes that will contribute to achieving the goals of the Kaizen Event. They will also implement many of them on a small scale, evaluate the results, and make further changes if needed.
Performance Improvement Plan ? Other Lean Methods
While Kaizen forms the foundation of lean manufacturing, other lean methods and techniques are often used to implement the suggestions and ideas generated as a result of Kaizen.
In the example above one of the goals was to reduce the die change times by 50%. A lean method called SMED (Single Minute Exchange of Die) is used to minimize die changes times. The concept behind SMED is to do as much of the die change work ahead of time so that the work required during the downtime for the die change is minimized.
Another lean method that helps provide the foundation needed for larger improvements is 5S. The idea behind 5S is to get the workplace cleaned up and organized. But, 5S is more than housekeeping; it involves organizing the workplace visually. What does this mean?
5S Visual Communication
Visual communication is the fastest, most reliable means of communication. For example, how do you ensure a tool, such as a hammer, is always returned to the correct storage location? You could make a rule about always putting the hammer into the 23B toolbox. But, when someone forgets to put it away, it's just out there, forgotten, and no one else knows where it belongs.
Using visual communication anyone can return the hammer to its correct storage location. For example, the hammer may have a green band on the handle. This identifies the hammer as belonging to the green storage area where there is a tool shadow board with the shape of each tool applied to the board. It's simple for anyone to place the hammer in the location of the green hammer shape. We now have a system in which tools are properly returned to their correct storage location. Anyone, speaking any language, knows where every tool belongs.
Performance Improvement Plan ? Implementing Visual Communication
Visual communication should be a part of a performance improvement plan. Improvement means changes. Those changes should be incorporated into the standards used by employees to get their jobs done. They may involve changing the way things are done; changing how machines are operated or maintained, and even changes to equipment design. Visual communication, in the form of labels and signs, is used to provide the new procedures, machine operating instructions, and equipment maintenance requirements at the point where the information is most needed... right on the machine or equipment.
Changes also impact safety, especially when employees need to change existing habits. Also, there are many safety signs and labels that are required by OSHA. Also, some temporary signs and labels may be appropriate while employees adjust to new procedures. Many of the signs and labels need to have custom messages or pictograms so that they address the specific changes being made. That means standard, pre-printed labels and signs won't do.
Where do these needed signs, labels, tags, and other visual communication tools come from? The answer is a DuraLabel custom label printer and tough-tested DuraLabel supplies. With a DuraLabel printer handy you can quickly make whatever custom labels and signs you need, as well as any needed standard OSHA signs, labels, or tags. That's because DuraLabel is the industry leader for quality, advanced technology, and ease-of-use. On top of that, you also get the best warranties in the industry. Call 888-342-3164 for more information about DuraLabel printers and supplies, or download your free copy of our Kaizen Best Practices Guide below.
Related Resources
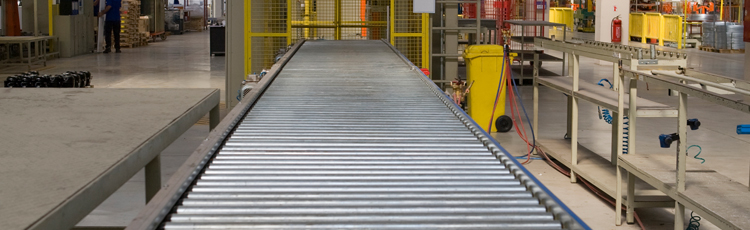
Calculating Overall Equipment Effectiveness (OEE)
What Is Overall Equipment Effectiveness and How Is It Calculated? Overall Equipment Effectiveness (OEE) is a ...
Read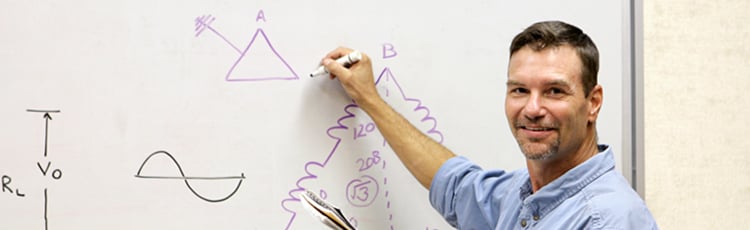
DFSS (Design For Six Sigma): A Customer Centered Process
What Is Design for Six Sigma and How Does It Improve Product Design? Design for Six Sigma (DFSS) is a ...
Read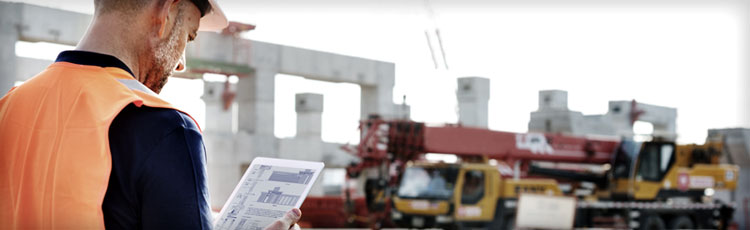
Lean Construction
What is Lean Construction? A term that is coming into common use is "lean construction." Lean construction ...
Read