Warehouse Management
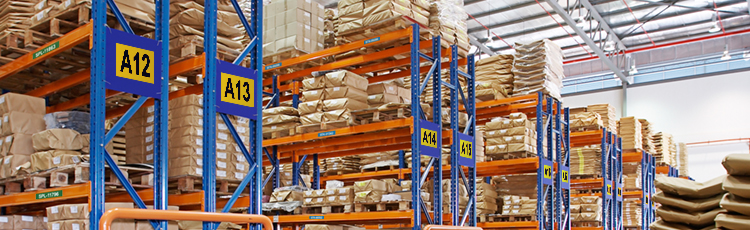
The global market is increasingly pressuring businesses to improve the efficiency of their operations. Today's warehouse management system is no exception. Using lean principles, warehouses will see a remarkable improvement in organization and product flow as well as their ability to meet the demands of customers.
What is Warehouse Management?
Warehouse management is a system that supports the daily operations in a warehouse. Today's warehouses have to manage the flow of material within the facility, as well as the flow of information throughout the supply chain. An effective warehouse management system helps businesses by:
- Supporting demand for custom orders (pick-and-choose orders)
- Resupplying stock based on customer demand
- Tracking inventory from the time it arrives at the warehouse to the time it reaches its final destination
- Maintaining the facility to protect goods
The Challenges
A growing trend for pick-and-choose orders and a fluctuating market have created new challenges for warehouse management. Warehouses can no longer stockpile products and wait for customers to purchase from their predetermined supply. Instead, warehouses must continuously move new or updated products to meet an ever-changing demand.
Challenges encountered by warehouse management may include the following:
Poor layout: Some storage areas may be overfilled while others are underused, which makes it difficult to find supplies. There can be too much space between workstations, increasing the time it takes to move an order from station to station. And workers may have to excessively reach, bend, or stretch to complete their tasks.
Ineffective storage and transfer of supplies: Fast-moving items might be stored in a tough-to-reach space, increasing the time and labor it takes to resupply picking lanes.
Ineffective processes: Frequent defects may be caused by poor inventory management, missing or damaged materials, and mislabeled supplies.
Recurring slow periods in the supply chain: Workers must wait for materials to be resupplied before shipments can be processed. Approvals for shipments and new materials can take too long to process and orders backup.
The Benefits
Warehouses will receive many benefits by implementing lean manufacturing in their management system. Warehouses will be able to meet the changing requirements of their customers by improving their efficiency, reducing errors, maximizing the space available for supplies, and by pulling supplies based on customer demand. Other benefits include:
- Reducing labor costs related to rework and inefficient handling of materials
- Reducing order processing time by standardizing workflow and limiting work-in-progress
- Reducing unnecessary transportation of supplies by storing materials based on how quickly they move
- Reducing slow periods by pulling supplies based on customer needs
Lean Solutions for Warehouse Management
While warehouses face many difficult challenges, lean manufacturing tools can be used to overcome many of them. In particular, value stream mapping (VSM), 5S, and Kanban can be used to make warehouses more efficient.
VSM
Value stream mapping is a process that enables warehouse managers to understand how things are currently working. Workflow is visually mapped out and relationships among processes are clearly identified, enabling warehouse managers to:
- Understand how various processes interact
- See how scheduling and departmental workflow affect operations
- Identify potential gaps in their processes
By creating a visual map, warehouse managers can identify materials that are being stored ineffectively or handled too often. They can also improve the warehouse layout and storage system to reduce handling and improve how items are stored. For example, fast-moving items should be easy to reach, while slow-moving items can be placed towards the back of the warehouse or at the top of the storage rack.
5S
5S is a lean manufacturing tool that can improve warehouse efficiency by systematically organizing and cleaning the workspace, as well as standardizing work practices and procedures. The system includes five guidelines (five S's) that can increase warehouse efficiency:
- Sort involves removing unneeded items from the workplace. Warehouses can maximize usable space by removing unnecessary tools, supplies, and equipment, increasing the available work area and storage space.
- Set in Order requires each unique work area to be arranged for convenience and efficiency. Work areas, tools, and supplies should be organized in a manner that will improve worker productivity; make it easier to move from one station to the next; and reduce movements like reaching, bending, and stretching.
- Shine requires employees to clean their work area after every shift. This step is designed to help workers spot potential issues by removing clutter, debris, and other items that may make it more difficult to find problems. A clean warehouse will make it easier to find excessive wear caused by faulty equipment; faulty packing systems, for example, can damage goods and increase rework.
- Standardize consists of documenting successful improvements, so they can be more easily applied in other work areas. Warehouses can optimize the efficiency of each workstation by applying consistent improvements throughout the workplace.
- Sustain requires each step in 5S to be repeated on a daily basis. This will ensure that warehouse management systems can improve work practices on a daily basis.
Visual communication is a key element for any lean warehouse management system. Labels and signs can be used to help organize the warehouse's storage system and provide essential information, while floor marking can be used to designate where tools, equipment, and supplies should be placed. This creates a visual map that helps workers quickly find and store supplies and tools.
Kanban
Kanban is a "pull system." It pulls supplies to the warehouse floor based on what customers have ordered, as well as the work that has been completed. Kanban uses visual cards to control the workflow within a supply chain.
In a warehouse management system, Kanban can improve processing time by creating an orderly and consistent flow of materials from picking to packing and shipping. Picking stations receive materials in a timely manner because the supply department sends additional supplies when it receives a Kanban card, signaling that the picking station needs more supplies. Instead of providing materials based on a rough guess, materials are provided in the exact number that is needed. Orders cannot pile up in the packing area, and they cannot overwhelm the shipping area.
Kanban's pull system also helps reduce errors in processing because it limits work-in-progress. New work cannot start until the current job is completed and moved to the next workstation. If a worker at the packing station notices that the items do not match the order, the packing station does not receive additional orders until the problem is fixed. This helps workers identify issues and prevent errors from being repeated.
Not sure where to start? Duralabel offers a free 5S System Guide as well as an in-depth Best Practice Guide for Kanban that can help you apply lean principles to your warehouse management system. These guides break down how to apply lean principles in nearly any workplace.
Related Resources
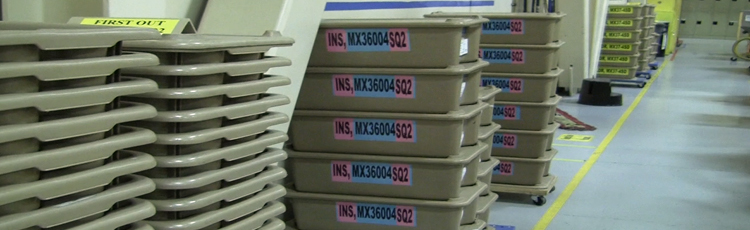
Start a Workplace Kanban Board
Efficiency is a necessity in business and life. Increasing efficiency saves time and money, which in turn ...
Read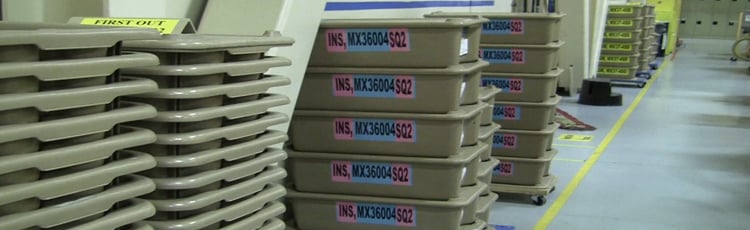
What Is Kanban?
In the face of declining sales and profits during the 1950s, Eiji Toyoda began looking for ways to improve ...
Read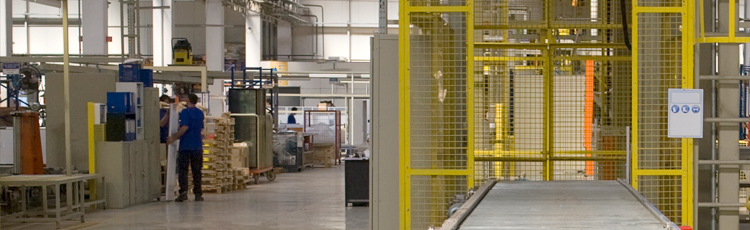
Understanding the 5 Lean Tools: Kaizen, 5S, and More
Five of the Most Helpful Lean Tools from 5S to Focus PDCA Lean manufacturing uses many lean management tools ...
Read