Quick Response Manufacturing
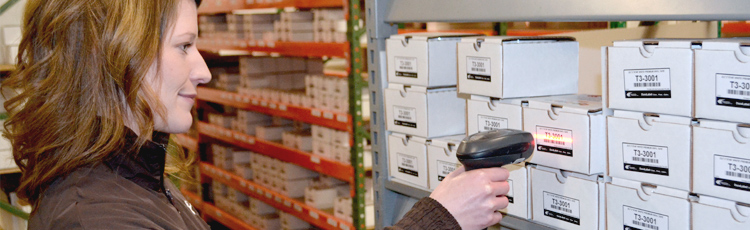
If you are familiar with lean manufacturing principles, you know that lean manufacturing is about eliminating waste. This typically results in reduced inventories and the ability to quickly respond to customer needs. Quick Response Manufacturing takes these principles a step further, putting the entire company's focus on quickly responding to customers.
What is Quick Response Manufacturing (QRM)?
The idea is simple: shorten the time between when an order is received until the delivery of the product or service. But it can go even further to include reducing the time required to bring a new product to the market, while still being able to design a product to meet specific customer needs. Essentially, Quick Response Manufacturing relentlessly pursues the reduction of lead time in all aspects of your operations. Externally, Quick Response Manufacturing means responding to your customers' needs by rapidly designing and manufacturing products customized to those needs. Equally important is what Quick Response Manufacturing means internally to your organization. Whereas JIT (or lean manufacturing) focuses on the relentless pursuit (continuous improvement) of eliminating non-value-added waste to improve quality, reduce cost (and reduce lead time), Quick Response Manufacturing focuses on the relentless pursuit of reducing lead times throughout your operation to improve quality, reduce cost, and eliminate non-value added waste.
The QRM focus is on the entire business, from purchasing through product delivery. This includes reducing the time needed to issue a purchase order, optimizing the supply chain, and reducing the time required to approve an engineering change. The objective isn't to work faster, but to eliminate waste and put priorities on the right objectives.
Moving Beyond Lean
Quick Response Manufacturing sounds a lot like lean manufacturing, and they are similar. However, lean is based on principles developed in auto manufacturing, and is best applied to high volume production of similar products. Quick response manufacturing is designed for companies with lower volume production, a production volume that varies, or manufacturers that make customized products. The leading example of quick response manufacturing is Dell computers, which became famous for quickly shipping computers made to customer's individual specifications.
Variability
One of the goals of lean manufacturing is to eliminate waste by minimizing variability. Quick Response Manufacturing refines this philosophy by distinguishing between strategic variability and dysfunctional variability.
Strategic variability adds value to the product line. Dell, for example, allows customers to select the options they want for their computers. This created a high level variability in the product, but also a high level of customer satisfaction.
Dysfunctional variability does not add value, is not desired by the customer, and so it must be eliminated. An example of dysfunctional variability would be imprecise manufacturing such that the product size varied more than customers could accept. Dysfunctional variability results in rework, product returns, and missed delivery dates.
Although Quick Response Manufacturing goes beyond lean, it does not throw out or ignore lean principles and methods. What it does is expand and refine lean principles to bring a sharper focus on reducing lead times.
How Does QRM Work?
QRM builds on the basic principles of eliminating waste and improving efficiency, while also incorporating principles unique to QRM. These include:
- Laser-like focus on lead time reduction in manufacturing.
- Rethinking the manufacturing process and equipment decisions, to put the focus on lead time reduction.
- Focusing all aspects of the organization, from the shop floor to the front office, and including vendors in the supply chain, on quick responses and reducing lead times.
- Training managers on using time-based strategies.
- Linking business strategies to functional strategies.
- Measuring performance in "time" units instead of monetary units.
- Using the principles of system dynamics to achieve quick response.
- Cell-based system of manufacturing.
- Implementing the Paired-Cell Overlapping Loops of Cards with Authorization (POLCA) planning and control method.
- A focus on implementation and sustaining changes that reduce lead times.
- Using Manufacturing Critical-path Time (MCT) to measure lead times.
With its focus on reducing lead times, manufacturing critical-path time is one of the key metrics used to measure success. This is the total time from when a customer creates an order, through the critical path, until the first part of the order is delivered. Notice that the clock starts when the customer creates an order. How quickly that ordered is received, processed, and moved into the manufacturing process is a part of the critical path. If orders come through an order desk, that includes sales people manually entering the order, manufacturing may not start until the next day. If the customer enters the order directly into an automated online system, manufacturing may start within minutes after the order was created.
By focusing on reducing the manufacturing critical-path lead time, waste is identified with the result that overhead costs are significantly reduced. The goals of the organization become unified around reducing lead time, with activities that increase lead-time being eliminated or redesigned.
Benefits of Quick Response Manufacturing
There are a number of significant benefits resulting from implementing quick Response Manufacturing. Three of the most important are:
- Increased customer satisfaction - We're in a highly competitive world in which waiting time is wasted time. If you can reliably deliver the products the customer wants, and do so quickly, you'll have happier customers who return to buy from you again.
- Increased cash flow ? By delivering products to customers quicker, you get paid quicker and your overall cash flow increases. This gives you more flexibility and a greater ability to respond to market changes.
- Beating the competition ? Quick Response Manufacturing drives innovation and prevents a company from resting on its laurels while a competitor innovates and steals away customers. The relentless focus on further decreasing lead times pushes an organization to continually be innovating, which results in improved quality, new product features, and a focus on being close to and serving customers.
For medium and small businesses focused on delivering customized products to their customers, Quick Response Manufacturing provides framework and methods to drive success. It's not an easy path, as it requires a relentless commitment to reducing lead times, but the rewards are well worth the effort.
If you're ready to take your business to the next level, download our free 5s System Best Practices Guide for actionable, expert advice on implementing 5s for your organization. Get your copy below.
Related Resources
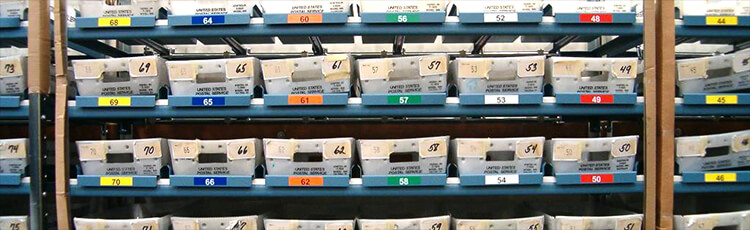
What Is Lean Manufacturing
Lean is an efficient approach to running a process, business or organization to minimize waste, lower lead ...
Read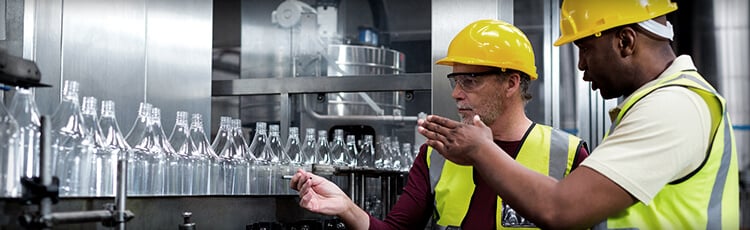
How to Improve Quality Control in Manufacturing with Lean and 5S
What Is Quality Control in Manufacturing and Why Does It Matter? In manufacturing, quality control is a ...
Read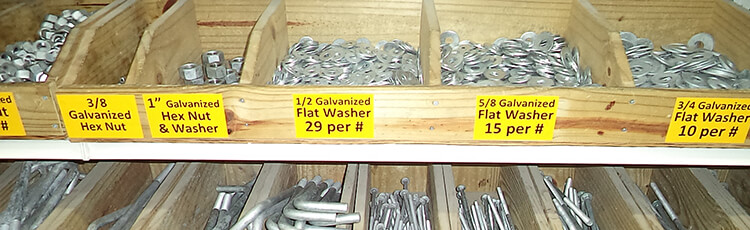
Lean Manufacturing Process
What is the Lean Manufacturing Process? The Lean Manufacturing processis a structured system for eliminating ...
Read