Durable Labels Built for the Skies: Weatherproof Aviation Solutions
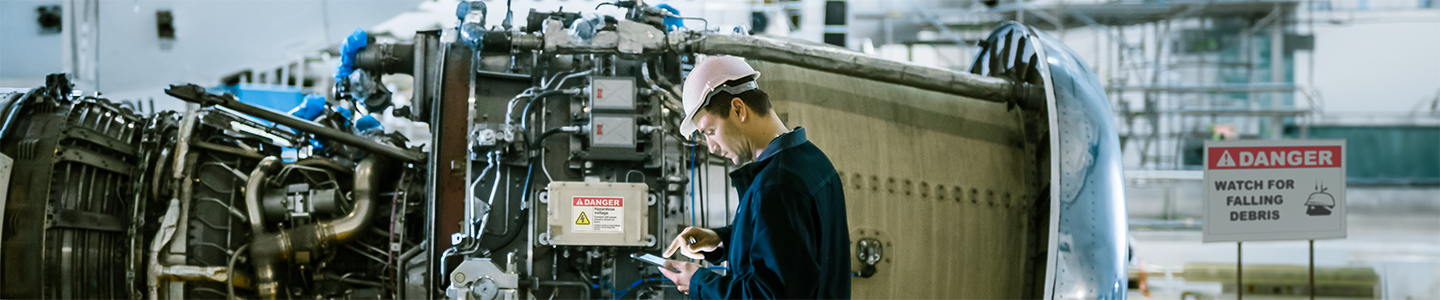
Aircraft components, parts, and equipment often face extreme weather conditions, including high altitudes, temperature fluctuations, humidity, and chemical exposures. As a result, the labels used to mark and identify equipment must remain legible and intact despite these challenging environments. As materials and technologies evolve, manufacturers have developed specialized labels that are built to meet the aviation industry’s tough standards for durability, visibility, and resistance to all kinds of weather challenges.
The Importance of Weather-Resistant Labels in Aviation
The Federal Aviation Administration (FAA) along with the American National Standards Institute (ANSI), and the Occupational Safety and Health Administration (OSHA) set the labeling standards for aviation in the United States.
On top of needing to know what type of label fits in what condition, aviation labels must also adhere to stringent regulatory standards. The FAA and other global regulatory bodies require labels to be clearly legible, durable, and compliant with safety guidelines. This includes ensuring that labels can withstand the physical stresses of air travel, such as vibration, pressure changes, and mechanical abrasion.
Durable labels in the aviation sector serve several essential roles, including identifying components, systems, and equipment. They also provide critical details like maintenance instructions, safety guidelines, and regulatory compliance marks. However, the challenge lies in ensuring that these labels remain legible, intact, and functional despite the demanding conditions they face.
In addition to durability requirements set by the FAA and ANSI, aviation labels must also meet OSHA’s standards for hazardous communications under 1910.1200: Hazard Communication. These standards focus on ensuring labels effectively communicate hazards though clear and consistent signal words. Concise messaging about risks and safety measures must also be included. Together, these regulatory frameworks guarantee that aviation labels are not only physically resilient but also provide critical information for workplace safety.
Key Requirements Under 1910.1200:
- The signal word must be "Danger," "Caution," or "Biological Hazard"
- The major message must indicate the hazardous condition or instruction
Aircraft are exposed to some of the most extreme weather conditions that range from freezing cold temperatures at cruising altitudes to sweltering heat on the tarmac. Labels must maintain their integrity in a wide range of environments, and exposure to jet fuel, oils, de-icing agents, UV radiation, and other chemicals can degrade standard labels. Without durable labels, safety, maintenance, and operational processes can be compromised, potentially leading to costly mistakes and safety risks.
Safety Signage Material for Extreme Conditions
Modern durable labeling for aviation is manufactured from advanced materials specifically designed to withstand the harsh conditions encountered in flight. The choice of substrate, adhesives, and printing technologies plays a key role in ensuring long-lasting durability.
- Aluminum and Metal Tags: Aluminum and other metal tags are considered the gold standard for durability in extreme aviation environments. These tags excel in resisting physical wear, UV radiation, saltwater, and corrosive chemicals. Their unmatched resilience comes from a process known as photo anodization, where the text is embedded directly into the aluminum's oxide layer. This process protects labels from fading, abrasion, and environmental degradation, making it ideal for critical applications such as part numbers, serial numbers, and permanent equipment identification.
- Polyester (PET): Known for flexibility and chemical resistance, polyester labels perform well in fluctuating temperatures and high-humidity conditions. They can also withstand UV rays, and most chemicals found in aviation settings while maintaining their adhesion and readability.
- Vinyl: Valued for flexibility and durability, vinyl labels resist moisture, UV radiation and environmental damage. They are commonly used on aircraft surfaces exposed to direct sunlight or outdoor conditions.
- Polyimide (Kapton): Engineered for extreme temperature resistance, polyimide labels function in a range spanning -270°C to 400°C (-454°F to 752°F). They are commonly found in engine components and other high-heat areas where thermal stability is critical.
While polyester, vinyl, and polyimide labels offer excellent durability, aluminum tags will remain unmatched in the long-term UV and environmental resistance due to the photo anodization process. Over time, other materials may succumb to photodegradation, losing clarity and adhesion, whereas aluminum labels retail their legibility for decades.
Adhesive Technologies for Maximum Outdoor Label Durability
When it comes to labeling aircraft, the adhesive plays a critical role. It must create a secure and long-lasting bond across a variety of surfaces while withstanding extreme environmental conditions. In aviation, there are two common types of labeling adhesives that provide long-lasting reliability and performance:
- Acrylic Adhesives: Known for their strength and versatility, acrylic adhesives excel in high heat, chemical exposure, and prolonged UV radiation. They offer exceptional durability, making them ideal for critical aircraft components exposed to outdoor conditions.
- Rubber-Based Adhesives: Rubber adhesives are valued for their high flexibility and initial tack, performing well in humid environments, fluctuating temperatures, and water exposure. These adhesives are commonly used in fuel tanks and pressure cabins, where secure bonding is essential.
Not all materials are created equal. Aircraft face a range of environmental challenges, which is why durable labels are essential to hold up in these tough conditions. Even the best adhesives have to cope with three main factors that affect label durability in aviation: UV exposure, temperature extremes, and chemical exposure. Each of these presents its own challenges, and the adhesive’s ability to handle them is just as important as the material and printing technology used.
UV Resistance and Anti-Fading Technology
UV radiation is one of the leading causes of label degradation, particularly when labels are exposed to direct sunlight for extended periods of time. This is a common concern for aircraft that spend a lot of time in the sunlight, whether in the air or on the tarmac.
Modern labeling materials incorporate UV-resistant coatings and inks to prevent fading and ensure long-lasting readability. UV-resistant labels can withstand prolonged exposure to sunlight without losing their legibility, making them ideal for external surfaces of the aircraft, such as wings, fuselage, and landing gear.
Additionally, anti-fading technologies, such as UV-cured inks and coatings, help maintain the clarity and contrast of the printed information, even after exposure to intense sunlight. This is particularly important for labels that display critical safety and maintenance information.
Temperature Resistance and the Impact of Altitude
Aircraft undergo significant temperature variations throughout a flight. While the outside temperature at cruising altitude can plummet to -60°F (-51°C), temperatures on the tarmac or inside the aircraft may soar to over 100°F (38°C) during summer months. As a result, outdoor labels must be able to resist both extreme cold and heat without losing their adhesive properties or becoming unreadable.
Outdoor labels, such as those made from polyimide, are designed to function in both high and low temperatures. These materials are often used in areas of the aircraft exposed to high heat, such as engines and auxiliary power units. Other materials, such as polyester and premium vinyl, can also withstand temperature fluctuations and are used for general applications across the aircraft.
Chemical Resistance for Harsh Environments
Aircraft are exposed to various chemicals, such as jet fuel, oils, lubricants, and de-icing agents. These substances can break down adhesives and damage surfaces, highlighting the importance of using labels specifically designed to resist chemicals.
To protect against chemical exposure, materials like polyester, vinyl, and metal are commonly used in aviation labels because of their durability. These materials stand up to challenges like fuel spills and harsh de-icing agents, keeping labels clear and intact. They also resist staining, fading, and deterioration over time, ensuring long-lasting readability.
DuraLabel Aviation Labeling Resources
As aircraft continue to soar through varying climates and demanding environments, the importance of weather-resistant labeling will remain a cornerstone of aviation safety and reliability. There have been many advancements in material science, adhesive technology, and printing techniques, so much so that it has become easier to create durable and versatile labels to maintain labeling compliance within the aviation industry. Weather-resistant labels that can endure tough conditions are critical to maintaining the safety, efficiency, and operational integrity of aircraft.
To guarantee the integrity of our premium vinyl labels, DuraLabel puts all products through a rigorous tough-testing process to ensure they can withstand the harshest of conditions. These tests measure adhesion, chemical resistance, accelerated weathering, and abrasion to provide customers with peace of mind that the labels they receive are quality-assured.
Ensure that your signs and labels are compliant with DuraLabel's free LabelForge PRO software. It comes preinstalled on the DuraLabel Toro Max and Kodiak Max Industrial Sign and Label Print System. The software allows users to design and print custom signs and labels in-house for any situation.
Learn more about DuraLabel’s free OSHA Safety Signage Quick Start Guide. It provides users with best practices for labeling under OSHA and ANSI requirements and standards. The guide also includes a facility site inspection checklist to help ensure compliance when creating OSHA/ANSI-compliant safety signs. Download your free guide today and call 1-888-820-4631 to speak to a safety professional who can guide you through the process.
Read Next:
Overcome Aviation Safety Top Challenges: Runway Incursions with FAA
10 Tips for Staying Current on Safety Regulations
Related Resources

Efficient Use of Barcoding Labels for Smarter Facility Management
With today’s technological advancements, much of the work force is searching for ways to become more ...
Read
5 FAA Safety Signage Tips for Aviation Facilities
Ensuring the safety and efficiency of an aviation facility relies heavily on the quality and effectiveness of ...
Read
Overcome Aviation Safety Top Challenges: Runway Safety and Incursions with the FAA
In February 2023, the Federal Aviation Administration (FAA) issued a Safety Call to Action to take a critical ...
Read