DuraLabel’s Tough-Tested Process: Raising the Bar for Label Durability
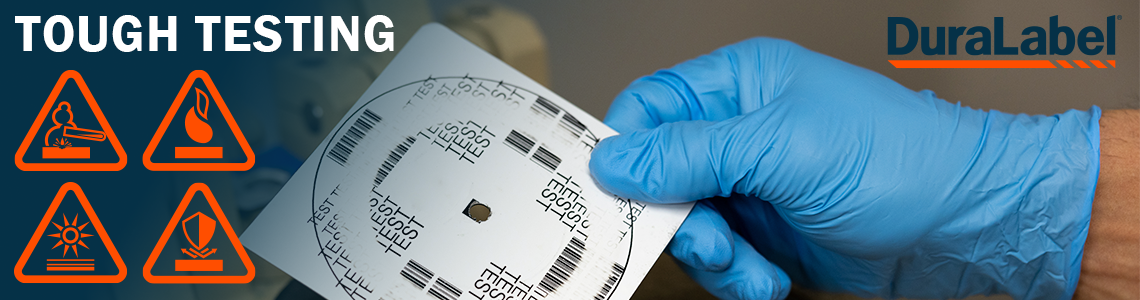
How DuraLabel's Tough-Tested Process Ensures Reliable Industrial Labeling
At DuraLabel, we are committed to providing industrial labels and safety solutions that are durable, reliable, and rigorously tested for compliance in the toughest conditions. Our tough-tested process includes environmental simulations, chemical exposure trials, and mechanical abrasion testing, methods designed to mimic real-world environments. By replicating the extreme conditions labels face in the field, we ensure that each label, sign, and floor marking product is proven to perform in tough environments.
Why We Test In-House
.jpg)
Conducting in-house testing allows DuraLabel to maintain complete control over quality assurance. By testing on-site, we can verify that each product meets our high standards and is evaluated under real-world conditions. This approach speeds up decision-making, promotes innovation, and guarantees consistent results.
Our Tough-Tested process applies to all 74,000 pre-printed signs, Pathfinder® Floor Marking Tapes, and DuraLabel Pipe Markers.
We also rigorously test our vinyl label supplies used in the Max line of print systems, including Kodiak Max, Toro Max, and Bronco Max. Every product undergoes industry-leading durability tests to confirm its reliability in the toughest environments.
Key benefits of DuraLabel’s in-house testing process:
- Control and Flexibility: Direct oversight of testing procedures ensures they meet the unique requirements of our products. For example, we replicate industrial environments by exposing labels to intense heat and cold in temperature-controlled chambers, guaranteeing reliable industrial labeling even in outdoor or manufacturing settings.
- Faster Turnaround: On-site testing delivers quick results and swift resolutions to potential issues. For instance, when designing a new floor marking tape, we can immediately test its durability by repeatedly driving a forklift over it to simulate warehouse traffic and enable fast adjustments if necessary.
- Consistency and Standardization: Our standardized testing methods guarantee uniformity and reliability across all products. UV, abrasion, and chemical-resistant labels are exposed to harsh solvents like acetone and alcohol to ensure they remain legible in facilities handling hazardous materials.
- Enhanced Expertise: Our in-house testing team continually improves methods and provides invaluable insights into product performance. By running abrasion tests with machinery parts frequently handled by workers, we ensure labels can withstand friction and remain intact.
- Integrated Development Process: In-house testing allows for seamless collaboration between product and QA teams, ensuring reliability testing for safety signage materials is incorporated early in product development.
By simulating scenarios like heavy equipment contact, chemical spills, and environmental stress, our testing process ensures DuraLabel products meet the rigorous demands of real-world demands. This commitment to quality delivers top-performing labels and signs while fostering continuous improvement in our manufacturing processes.
How DuraLabel’s In-House Testing Compares with Industry Standards
DuraLabel's testing processes don’t just meet industry standards—they raise the bar. While many manufacturers rely on generic certifications or outsourced testing, DuraLabel takes a direct, hands-on approach.
Adhesion Testing
Industry standards, like UL 969, require labels to adhere under controlled conditions, often involving set temperatures and smooth surfaces. DuraLabel testing goes beyond these requirements by simulating real-world challenges, such as high-impact vibrations from heavy machinery and exposure to grease and oil. For example, DuraLabel tests labels on uneven and textured surfaces commonly found in manufacturing environments to verify adhesion under harsher conditions.
Chemical Resistance Testing
The ASTM Standards for Label Durability focus on wear and tear, often testing resistance to a small range of chemicals. DuraLabel expands on these tests by exposing labels to a broader set of substances, including industrial solvents, cleaners, and harsh chemicals like acetone and sulfuric acid. This ensures the labels remain legible and durable even in industries like food processing and automotive manufacturing, where chemical exposure is common.
%20(1).jpg)
Weather Resistance Testing
DuraLabel's approach to weather resistance builds on industry benchmarks for UV exposure, rain, and temperature shifts. While many manufacturers simulate only a few months of outdoor wear, DuraLabel uses advanced weathering chambers to replicate years of harsh outdoor conditions. Labels are subjected to prolonged UV rays, heavy rainfall, and extreme temperatures up to 300°F, ensuring durability in environments like construction sites, transportation yards, and energy plants.
Pipe Marking Compliance
DuraLabel adheres to ANSI/ASME A13.1 for pipe labeling, which sets the standard for the size, color, and placement of pipe markers for safety and compliance. DuraLabel’s tough-tested pipe markers are evaluated for legibility, adhesion, and fade resistance in industrial settings, ensuring clear communication of hazards and pipe contents over time.
By exceeding industry requirements, DuraLabel delivers products that perform in scenarios where other labels might fail. Whether exposed to harsh chemicals or extreme weather, DuraLabel ensures your facility’s signage remains clear and durable, even in the toughest conditions.
The Benefits of Tough-Tested Products
Tough-tested products are more than just labels—they’re a long-term investment in your facility’s safety and efficiency. Here's how our testing delivers real benefits for your business:
- Cost Savings: Tough-tested labels are proven to last longer, reducing maintenance costs and minimizing the need for frequent replacements. This leads to fewer operational interruptions and less downtime.
- Risk Mitigation: Low-quality signs and labels can result in miscommunication, workplace accidents, legal issues, and Occupational Safety and Health Administration (OSHA) violations. Tough-tested labels resist wear and remain clear and legible in harsh conditions, helping prevent costly fines and accidents.
- Improved Workplace Efficiency: Reliable labels minimize confusion and delays, allowing employees to quickly locate tools, materials, and safety information. This streamlines workflows and reduces time wasted due to unclear or missing labels.
- Reduced Environmental Impact: Durable labels require fewer replacements, resulting in less waste over time. By using tough-tested labels, businesses contribute to sustainability efforts by minimizing discarded materials and packaging.
- Compliance Assurance: Under OSHA Standard 1910.335(b), which requires clear marking of electrical hazards, failure to display compliant labels could lead to penalties, with violations incurring fines up to $16,550 per incident as of 2024. DuraLabel’s tough-tested labels align with OSHA and ANSI standards, helping your facility stay compliant with safety regulations.
DuraLabel’s Tough-Tested Supplies
DuraLabel offers a wide range of industrial labeling supplies, each designed for durability and performance in challenging environments. Every one of our products undergoes rigorous testing to confirm its reliability for the most demanding of applications. Here’s a closer look at some standout supplies and their testing processes:
Premium Vinyl Labels
Tested for adhesion, abrasion, and weather resistance to confirm they withstand outdoor conditions. DuraLabel’s premium vinyl labels resist peeling and fading, even in high UV exposure, making them an excellent choice for construction sites and outdoor signage.
Metal-Detectable Labels
Ideal for food production environments, these labels are tested for their detectability by scanners to prevent contamination risks. These labels are also tested for adhesion and chemical resistance to prevent label failure.
Reflective and Glow-in-the-Dark Signs
Reflective signs are tested for visibility under low-light conditions, while glow-in-the-dark signs undergo luminance testing to verify that they provide clear readability during power outages or emergencies.
Anti-Slip Floor Markings
Designed for high-traffic areas like warehouses, these markings are tested for abrasion and chemical resistance. They also undergo traction testing to confirm safe performance in slippery environments.
High-Temperature Labels
Created to withstand extreme heat and cold, DuraLabel’s specialty labels perform in temperatures ranging from –320°F to 300°F. Tested for adhesion and legibility in demanding conditions, they resist cracking, peeling, and discoloring, even when applied to hot surfaces like furnaces, boilers, and motors.
By tailoring testing processes to specific supply needs, DuraLabel ensures each product delivers unmatched quality and durability. Whether your industry requires contamination prevention, heat resistance, or advanced workplace safety measures, DuraLabel supplies are built to perform.
OSHA Compliance and Labeling Standards
At DuraLabel, we understand the importance of staying compliant with OSHA standards. Safety is paramount in every workplace, and proper signage and labeling play a critical role in preventing accidents by clearly communicating hazards.
DuraLabel products meet or exceed OSHA’s labeling and signage requirements, which includes clear visibility, proper hazard identification, and adherence to specific color codes. From pipe markers to safety signs and hazard labels, DuraLabel solutions align with OSHA’s guidelines for visual communication.
Our labels and signs are designed to endure harsh industrial environments while maintaining legibility, helping businesses avoid OSHA violations, fines, and, most importantly, reduces the risk of workplace accidents.
DuraLabel also offers customizable products, allowing businesses to create labels and signs tailored to their specific safety needs. Whether marking emergency exits, warning of hazardous chemicals, or identifying equipment, DuraLabel supports compliance while enhancing workplace safety.
Case Study: IPG Photonics Corp. & DuraLabel
Client’s Background
Michael Hoffman is the Production Manager at IPG Photonics Corp., a leading provider of laser systems. The company needs reliable, durable labels for safety and product identification in their manufacturing process.
The Challenge
Before switching to DuraLabel, IPG Photonics struggled with finding labels that could resist oils and adhere well to their products. "We were exploring other options, but we were not satisfied with their final product," Hoffman said.
The Solution
DuraLabel’s tough-tested labels provided the perfect solution. They adhered securely to products, resisted oils, and maintained their legibility. "We use DuraLabel products to print various safety and identification labels for our products," Hoffman said.
The Results
Since using DuraLabel, IPG Photonics has seen increased reliability in their labeling system, with fewer replacements needed. "We just had more reliability in the decals adhering to the products," Hoffman said.
DuraLabel’s Tough-Tested Processes
At DuraLabel, we don’t just rely on standard tests—we push our labels to the limit to make sure they are ready for the most challenging environments. Here’s how we do it:
Adhesion Test
Adhesion tests verify that labels stick securely, even under high-stress conditions. This ensures that labels stay intact during the toughest use cases, such as large-scale machinery in the manufacturing industry, where constant vibration and heavy use demand durable labeling solutions.
Steps:
1. Apply the label to a surface, such as an aluminum plate.
2. Use a shear strength tester to apply a specified weight.
3. Measure the duration the adhesive can hold before failure (minimum 15 minutes).
Evaluation: Labels must remain adhered for the full duration without lifting or peeling.
Chemical Test
Labels must resist various chemicals like oils, solvents, and cleaners. This test checks that labels remain legible and intact when exposed to substances commonly found in industrial settings, such as chemical plants or automotive repair facilities, where labels often face exposure to harsh cleaning agents or lubricants.
.jpg)
Steps:
1. Apply the label to a surface like stainless steel.
2. Use a Q-tip dipped in chemicals (e.g., isopropyl alcohol, acetone) and rub it on the label.
3. After 24 hours of submersion, assess any signs of degradation.
Evaluation: The label fails if it becomes illegible or loses adhesion.
Accelerated Weather Test
Our accelerated weather test simulates long-term outdoor exposure to UV rays, moisture, and humidity. It ensures that labels can endure the toughest weather conditions without fading or deteriorating.
Steps:
1. Apply the label to a test surface.
2. Place the sample in a weathering chamber for 360 hours (equivalent to one year of outdoor exposure).
Evaluation: The label is considered to have failed if it shows significant degradation or becomes illegible—critical for the trucking and railroad industries, where labels must withstand constant exposure to sun, rain, and extreme temperatures.
Abrasion Test
DuraLabel’s abrasion test ensures that labels retain readability even after repeated handling or contact with abrasive surfaces. It's particularly important in warehousing and logistics, where labels on pallets and storage bins face constant handling, scraping, and movement across surfaces.
Steps:
1. Attach the label to a surface and subject it to rotational abrasion using a Taber Abraser.
2. Perform up to 50 cycles of abrasion.
Evaluation: Labels fail if the text or barcode becomes unreadable after abrasion.
DuraLabel’s Tough Tested Label
These processes guarantee that the products are thoroughly tested through various elements. This provides a detailed assessment of their durability under different conditions, so facilities can have confidence in the quality of the products they buy.
DuraLabel Tough-Tested Solutions
A deteriorated sign can cause confusion, delay, and harm. Workers can even get injured from managing a container with worn-down handling instructions. By utilizing durable, OSHA-compliant signs, you can provide your team with important safety instructions and guidelines based on the facilities they work in.
Whether it’s safety signs, pipe markers, or equipment labels—DuraLabel’s tough-tested floor marking and safety signs are ready to protect workers throughout the workplace. Get help crafting a system that will provide the safety communication you need. Call 1-888-965-3359 and one of our experts will guide you through the process.
Learn more about how to stay up to date on OSHA signage requirements that can be used to help create a safer environment that gives workers peace of mind. Download our free Facility Signage Handbook today.
Read Next:
How Sun Exposure Affects Pipe Labels
Creating a Visual Factory with the 5S System
Related Resources
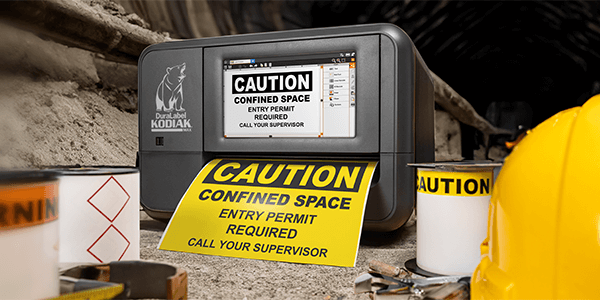
Why Upgrade to the DuraLabel Kodiak Max Industrial Sign & Label System
Why Choose the DuraLabel Kodiak Maxfor Industrial Labeling Upgrades? Managing a complex facility comes with ...
Read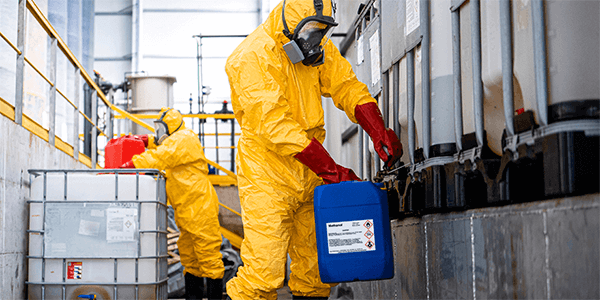
Choosing Outdoor Labels That Withstand Harsh Environments
How to Label for Extreme Environments and Maintain OSHA Compliance Labeling for extreme environments while ...
Read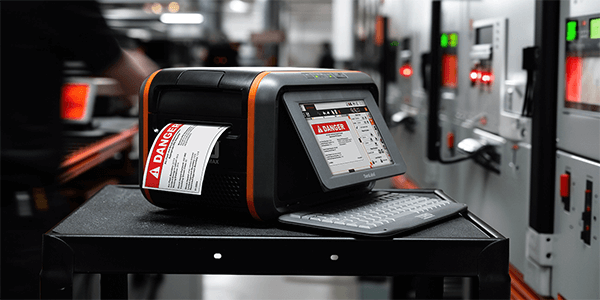
Top 10 Uses for DuraLabel Industrial Label Printers
How DuraLabel Printers are Used Across 10 Key Industrial Applications DuraLabel printers are built to solve ...
Read