What is HazCom? Your Guide to Chemical Labeling, GHS, & OSHA Standards
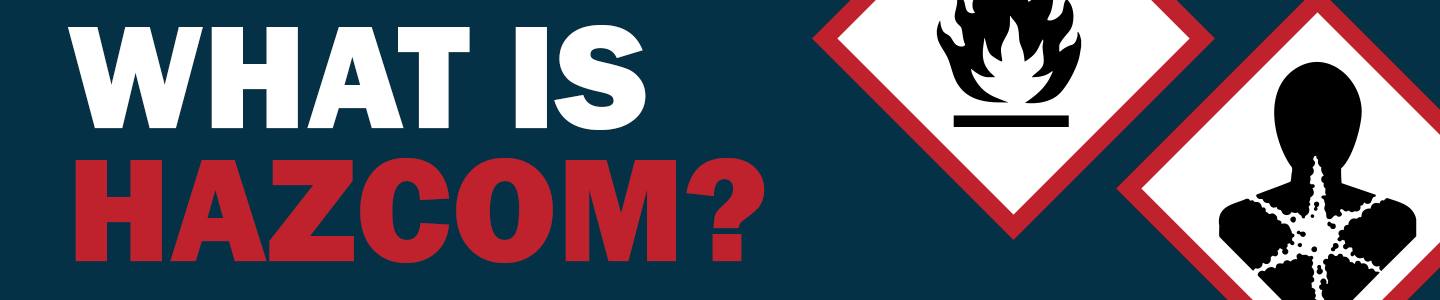
What Is OSHA’s Hazard Communication Standard (HazCom)?
"HazCom" is short for "Hazard Communication," OSHA’s framework for ensuring that employees understand the risks of hazardous chemicals in their workplace. It standardizes chemical labeling, Safety Data Sheets (SDS), and training requirements so that workers can recognize, avoid, and respond to chemical hazards effectively.
OSHA and Hazard Communication Standards
Chemical hazard violations remain one of OSHA’s most frequently cited workplace safety issues. Inadequate labeling and unclear communication expose workers to serious risk — and organizations to costly penalties. OSHA’s Hazard Communication Standard (HazCom), established under regulation 29 CFR 1910.1200, provides a structured framework for labeling, storing, and managing hazardous chemicals in the workplace. For employers building or strengthening a compliance strategy, this is the best place to start.
HazCom ensures that chemical hazard information is accessible, standardized, and actionable across all types of work environments — from factories and labs to construction sites and warehouses. It requires a written hazard communication program that includes accessible Safety Data Sheets (SDS), compliant labeling, and employee training. According to OSHA, more than 130 million U.S. workers are covered under the standard.
Did You Know? In 2023, HazCom ranked second among OSHA’s most-cited violations, with 3,227 citations issued — a 34% increase from the previous year.
This article breaks down how HazCom works, how it aligns with the Globally Harmonized System of Classification and Labelling of Chemicals (GHS), and what your organization must do to stay compliant. Whether you're launching a new program or updating an existing one, understanding HazCom is essential for both workplace safety and regulatory readiness.
HazCom: The Foundation of Chemical Safety
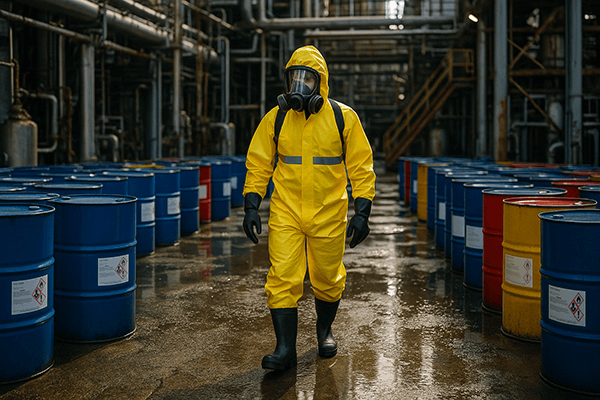
OSHA introduced the Hazard Communication Standard in 1983 to ensure workers are informed about the chemical hazards they may encounter on the job. Outlined in OSHA regulation 29 CFR 1910.1200, the standard defines how chemical hazards must be evaluated, labeled, and communicated in the workplace.
In 2012, OSHA aligned HazCom with the United Nations’ GHS, standardizing chemical classification. This alignment brought consistency to label elements, such as signal words, pictograms, and hazard statements, reducing confusion and improving both international trade and workplace safety.
HazCom applies to virtually every industry, from manufacturing and construction to healthcare and education. Any employer whose workers handle hazardous chemicals is responsible for complying with the standard and maintaining it.
Responsibilities under HazCom vary by role:
Manufacturers must: | Employers must: |
---|---|
|
|
GHS Label Requirements and OSHA Appendix C
GHS labeling is a foundational part of HazCom compliance. OSHA’s Appendix C to 29 CFR 1910.1200 outlines the specific elements required on each chemical label. These components provide an at-a-glance overview of chemical risks and how to handle them safely.
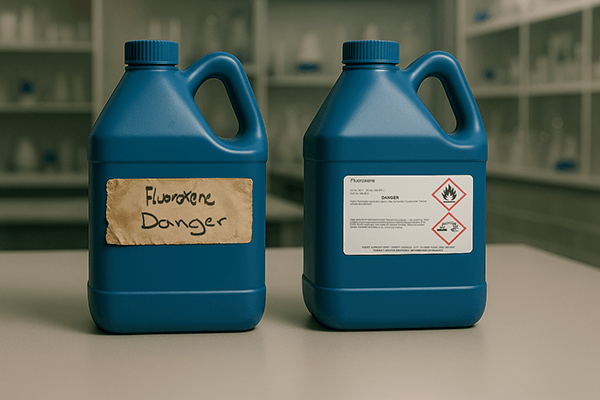
Each chemical label must include the following standardized elements:
- Signal word: Either "Danger" or "Warning", depending on severity
- Hazard statement(s): Describes the nature of the hazard (e.g., “May cause cancer”)
- Pictograms: Red-diamond shaped icons representing different hazard categories
- Precautionary statements: Instructions for prevention, response, storage, and disposal
- Product identifier: A unique ID or name for the chemical
- Supplier identification: Contact details for the manufacturer or importer
Regulatory Note: Appendix C.4 lists more than 30 hazard classifications, each with exact phrasing and required pictograms. For example, a chemical labeled “Acute Toxicity–Oral, Category 1” must display the signal word “Danger,” the hazard statement “Fatal if swallowed,” and the skull-and-crossbones pictogram.
GHS labels are required for all shipped containers and workplace labels, unless a specific exemption applies. Labels must remain legible, written in English, and firmly attached to the container throughout its use.
Tools That Support GHS Labeling and HazCom Compliance
To meet chemical label compliance requirements, many organizations rely on industrial labeling systems and label design software. Together, these tools enable safety teams to produce durable, GHS-compliant labels on demand, improving both accuracy and efficiency across departments.
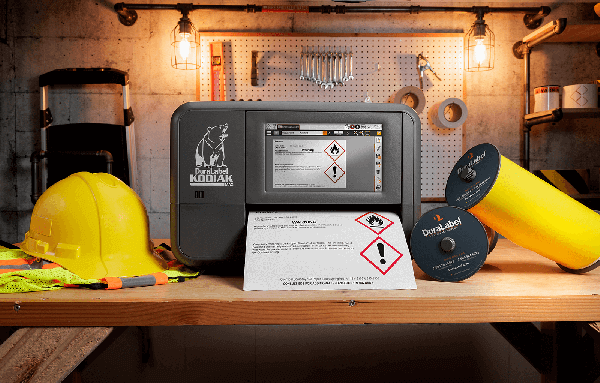
How Industrial Printers Streamline Chemical Labeling
Industrial printers for HazCom labels, such as the DuraLabel Kodiak Max Industrial Sign and Label System, are built for high-volume, high-performance environments. With two-color thermal transfer capability and a user-friendly interface, the Kodiak Max printer supports the creation of OSHA signage, GHS labels, and custom visuals in a single system.
DuraLabel Sign and Label Systems empower teams to print labels in-house, reducing lead times and enabling quick adjustments as chemicals or regulations change.
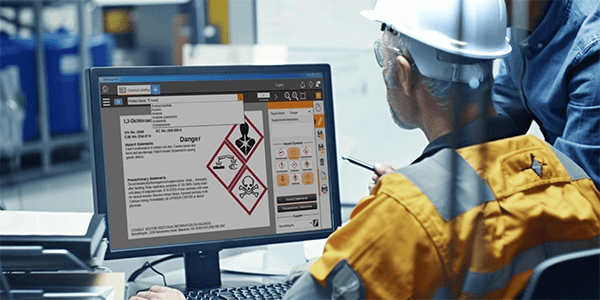
LabelForge PRO Software and Template Automation
Complementing the hardware, LabelForge PRO offers thousands of preloaded GHS label templates, compliant symbols, and formatting tools aligned with OSHA’s Appendix C. The software automates layout formatting, text alignment, and pictogram placement, dramatically reducing design time and human error. With multi-language support and seamless integration across DuraLabel printers, it’s an ideal solution for diverse, multi-site operations.
By standardizing visual communication across containers, workstations, and storage areas, LabelForge PRO and Kodiak Max provides a scalable solution for building a compliant, resilient HazCom labeling system. They help organizations stay audit-ready, minimize labeling errors, and maintain consistency, even in fast-paced or highly regulated environments.
These tools simplify:
- Creating GHS labels for complex or custom chemical products
- Updating label formats to reflect regulatory or procedural changes
- Integrating label data into broader safety and compliance workflows
HazCom Beyond Labels and How to Store Chemicals Safely
Chemical labeling is just one piece of the HazCom puzzle. Proper chemical storage is equally critical for maintaining compliance and ensuring worker safety. For example, OSHA regulation 29 CFR 1910 Subpart H outlines requirements for the safe handling and storage of flammable liquids, gases, and other hazardous materials.
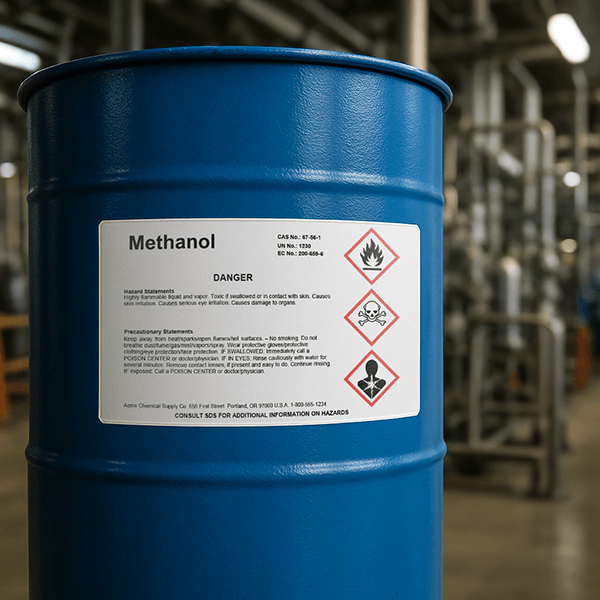
Facilities are required to:
- Store incompatible chemicals separately
- Provide proper ventilation fin storage areas
- Use corrosion-resistant, sealed containers
- Maintain clear hazard signage and emergency labeling
HazCom labeling is only effective when supported by proper storage practices and emergency preparedness. A well-known incident illustrating this need occurred in Alabama, when an explosion killed a pipeline installer. OSHA determined that flammable welding gases were stored without proper ventilation, and improper storage was the root cause.
“This tragedy could have been avoided if the employer had followed required procedures for storing dangerous gases,” said OSHA officer Ramona Morris.
In critical moments, GHS labels help first responders identify hazardous materials and locate storage points quickly. Pairing these labels with OSHA-compliant safety signs and pictogram posters enhances situational awareness for employees and visitors alike.
Facilities are also encouraged to conduct regular Job Hazard Analyses (JHAs), inspect chemical storage areas, and ensure that GHS-compliant signage is prominently displayed. These proactive steps help prevent incidents and support a coordinated emergency response.
HazCom Training and Employee Awareness
Training is a core requirement under HazCom. Per 29 CFR 1910.1200(h), employers must train workers on chemical hazards, how to read GHS labels, interpret SDS, and follow emergency procedures. This training must take place during onboarding and whenever new chemical hazards are introduced.
A written HazCom plan must be maintained and should outline:
- The complete chemical inventory
- Procedures for maintaining chemical label compliance
- Methods for communicating hazards in non-routine tasks
- A documented employee training strategy and schedule
Effective HazCom training goes beyond checking boxes. It must be practical, engaging, and continuous. Facilities handling corrosives, flammables, or reactive substances should tailor training to their specific operations, covering PPE requirements, eye wash stations, emergency response procedures, and chemical spill kits.
Ongoing training, toolbox talks, and hands-on walkthroughs help employees stay informed about chemical inventory changes or updated GHS label requirements. Using visual aids like pictogram charts, safety posters, and sample labels can significantly improve clarity and retention.
Emergency Preparedness and Prevention Through Visual Communication
Effective emergency planning goes hand-in-hand with visual hazard communication. According to the U.S. Chemical Safety Board (CSB), many chemical incidents stem from gaps in emergency planning and poor communication between facilities, workers, and emergency responders. A complete HazCom system supports preparedness by incorporating clear, consistent visual cues throughout the facility, including:
- Clearly marked exits and emergency routes
- Properly labeled valves, tanks, and shutoff devices
- Strategically placed SDS stations and emergency equipment
- Visible reminders of PPE requirements and hazard zones
SDS stations should be located in accessible, high-traffic areas near chemical handling zones. These stations should be clearly marked with signage such as “SAFETY DATA SHEETS” or “CHEMICAL INFORMATION CENTER” to avoid confusion during a critical moment.
Additional visual indicators, such as high-visibility arrows, floor markings, and signs for “emergency shutoff” valves, can support faster response and safer evacuation. Color-coded pipe markings, emergency labels, and visual safety signage provide instant hazard identification, helping employees and first responders act quickly and appropriately.
Employers are also encouraged to conduct JHAs to identify task-specific chemical risks and ensure that visual communication tools are placed strategically to support both prevention and emergency response.
The Value of a Compliant HazCom Labeling System
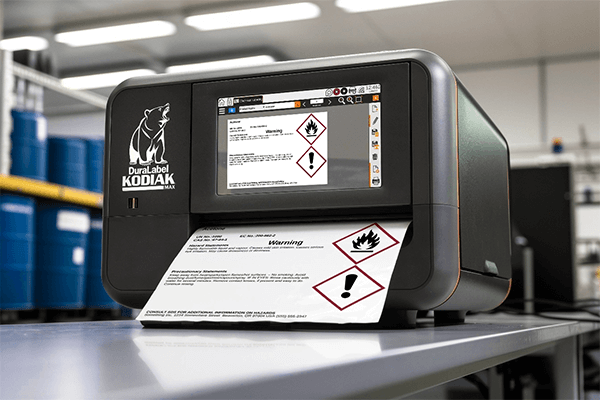
A fully implemented HazCom labeling system offers benefits that go well beyond regulatory compliance. It supports a proactive safety culture, improves operational efficiency, and contributes to long-term business resilience.
According to OSHA, for every $1 spent on workplace safety, companies can save $4 to $6 in reduced injury claims, insurance premiums, and lost productivity. Key benefits of a compliant HazCom system include:
- Reduce injury and illness rates
- Fewer OSHA citations and lower insurance costs
- Improve employee confidence and morale
- Accelerate onboarding for new staff
Standardizing chemical labels across departments and locations helps organizations scale compliance and reduce confusion. Consistent labeling supports rapid hazard identification and ensures employees can rely on visual information in real time.
In one example, a global manufacturing company improved its chemical labeling workflow by transitioning in-house printing processes. The shift to a standardized visual labeling system reduced inconsistencies, improved clarity, and enhanced site-wide hazard communication. Tools used in that transition include thermal transfer printers designed for industrial labeling needs, which support durability, regulatory alignment, and flexibility in label design.
When chemical label compliance is treated as a core element of workplace operations, organizations can streamline audits, strengthen training programs, and build a culture where safety is both visible and actionable.
The Role of Industrial Label Printers in HazCom Compliance
Implementing an effective HazCom labeling system requires more than regulatory knowledge—it requires the right tools. Industrial sign and label printers ensure that every hazardous material in a facility is properly marked with durable, on-demand labels that meet HazCom and GHS label requirements.
The DuraLabel Kodiak Max offers high-quality, two-color thermal transfer printing suitable for a wide range of applications. It’s built for GHS and HazCom labels, OSHA/ANSI safety signage, and more. Its rugged design, intuitive interface, and support for large label rolls make it a strong fit for dynamic industrial environments that demand flexibility and performance. When paired with DuraLabel’s tough-tested, chemical-resistant label stock, the system delivers long-lasting performance. Labels remain legible and compliant even in harsh conditions with exposure to solvents, abrasions, and extreme temperatures.
Industrial printers help reduce errors by ensuring consistent formatting across shifts and departments. By bringing GHS-compliant label production in-house, organizations can minimize lead time, eliminate outsourcing, and support real-time adjustments as regulations evolve. Whether updating hazard statements, modifying pictograms, or adjusting label sizes, industrial printing solutions give teams full control over their HazCom labeling system.
DuraLabel HazCom Labeling Resources
HazCom is more than a labeling protocol, it is an ongoing system of communication, preparation, and accountability. By aligning with GHS, maintaining accessible training, and using reliable tools, employers can build safer workplaces and stronger compliance frameworks.
For operations that handle hazardous materials daily, the tools used to communicate risk truly matter. A dependable industrial labeling system helps ensure every label meets compliance standards without slowing down productivity. When paired with durable supplies and purpose-built software like LabelForge PRO, organizations can maintain clear, legible, and long-lasting hazard communication.
If you are building or updating your hazard communication program, the free HazCom Labeling Quick Start Guide is a great place to start. It simplifies HazCom and GHS requirements, provides OSHA-compliant examples and use cases, and offers guidance for choosing the right materials and labeling tools. This guide is designed to help teams meet the standard and maintain it over time.
Whether you're starting your compliance journey or improving existing processes, this guide helps ensure your labeling strategy aligns with OSHA standards and industry best practices.
Have questions about HazCom or other compliance projects? Feel free to contact us at 1-888-789-7964 to speak with one of our safety and compliance specialists. We’re here to help guide you through the process.
Read Next:
HVAC Installation Done Right: 8 Essential Tips to Prevent Costly Mistakes
Related Resources

GHS-Compliance: Safe and Effective Storage of Hazardous Chemicals
The Importance of the GHS When working with and storing hazardous chemicals, steps must be taken to ensure ...
Read
What is HAZOP? HAZOP Analysis and Industrial Label Printer Insights
Workplace safety should always be at the forefront of your mind. Many recommendations exist on how to go ...
Read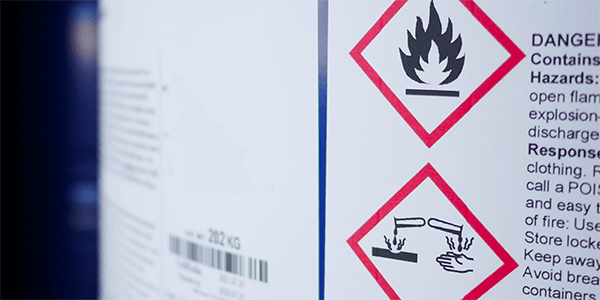
How DuraLabel Systems Improve GHS Labels for Compliance and Safety
How DuraLabel Printers Simplify GHS Labeling for Compliance and Safety In regulated industrial environments, ...
Read