Why is Assessing Process Flow in Manufacturing Critical?
When I think of process flow, a parade comes to mind. The floats, marching bands, celebrities waving from sports cars, and giant character balloons move past without interference and appear as a well-planned process. If a car stalls, a street gets blocked, or Mother Nature gets involved-such as the downpour on the 1957 Macy's parade when a large Popeye balloon dumped gallons of water on surprised spectators-then the parade gets bottlenecked. That's a huge bummer for everyone watching. Congestion slows the process, and increases wait time for spectators. It's a dampened experience to say the least.
Similar to the bottleneck of a parade, if the process flow in manufacturing meets interference such as a machine breakdown, a flaw in raw material, or operator error-then constraints occur, causing late product delivery to customers. The end result is dissatisfaction and time and money spent on damage control which hurts the bottom line for businesses. Failure to assess your process or meet your goals is known to put companies out of business. It is critical that you plan and assess your process flow well.
Start your process flow assessment by taking a gemba walk. Observe and ask questions outlining the following seven flows identified by Japanese manufacturers:
- Flow of Raw Materials
What is the standard work? Where are the materials coming from and how are they transported? What size and type of containers are being used?
- Work-in-Process Flow
What is the standard of work? Are there any machine cycle times?
- Flow of Finished Goods
How is the transfer of material accomplished? What types of conveyors, carts and forklifts are used?
- Operator Flow
What is the operator's cycle time? What are the operator's body movements? Observe the operators' tasks. Is there visual communication to aid new operators?
- Machine Flow
What is the machine cycle time? What are the set-up requirements? What is the machine process and is it right-sized for what is required? What are the requirements of properly maintaining machines? What are the steps required to operate the machine? Are proper Lockout/Tagout tags and signs easily accessible? Observe the machine wastes.
- Information Flow
What information is needed for anyone involved in the supply chain? Where is the information available, and how does it get passed on? What are the decisions made by the operator? How many decisions are made by the operator? Who responds to the operator's needs? What information is on production control boards, production schedules, kanbans, manufacturing plans?
- Engineering Flow
What tools are required? What are the process controls and quality checks? Observe any hanedashi devices (the mechanisms to automatically eject a part from the machine to free up the operator to only load the machine.)
It's important to physically sketch out each flow. In each of the seven flows you can make improvements by:
- Identifying constraints in each process
- Determine the root cause of the constraints
- Find solutions to eliminate the root cause of the constraints
- Test the solutions to determine if they work.
Your goal should be to create a harmonious system within all seven flows. Whether implementing Total Productive Maintenance (TPM) or using kanban as your inventory system, continuous assessment of process flow in your warehouse will lower manufacturing costs and keep your customers satisfied.
Related Resources
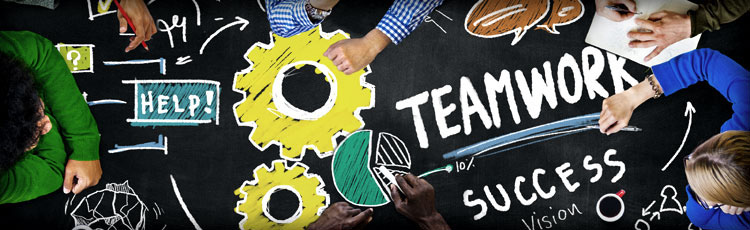
The Organizational Development Process
To understand the organizational development process, we first need to know what organizational development ...
Read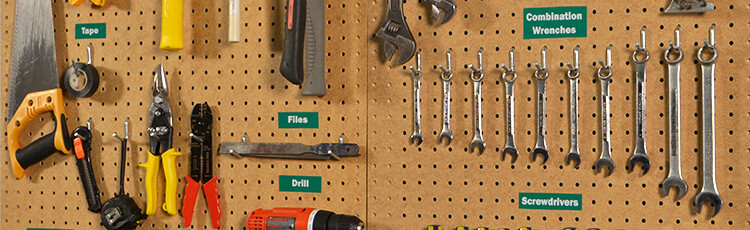
Lean Manufacturing Efficiency
Improving manufacturing efficiency requires eliminating waste. What is waste? Anything that is not adding ...
Read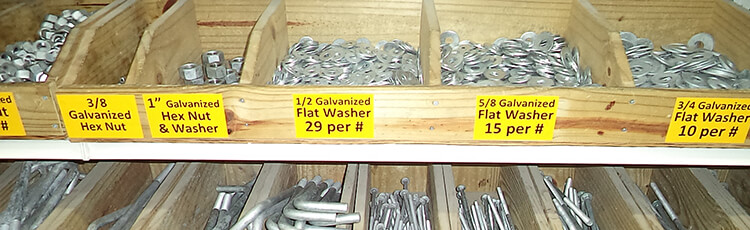
Lean Manufacturing Process
What is the Lean Manufacturing Process? The Lean Manufacturing processis a structured system for eliminating ...
Read