How to Improve Quality Control in Manufacturing with Lean and 5S
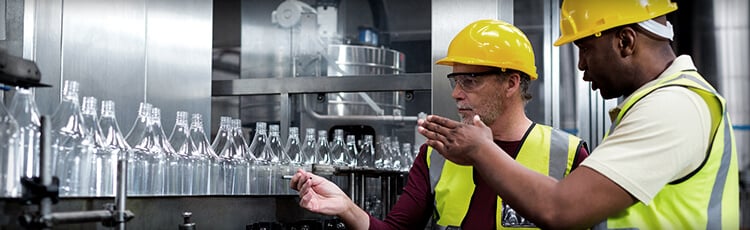
What Is Quality Control in Manufacturing and Why Does It Matter?
In manufacturing, quality control is a process that ensures customers receive products free from defects and meet their needs. When done the wrong way, it can put consumers at risk. For example, the recent defect found in Takata airbags resulted in the biggest automotive recall in history. The recall includes almost 69 million airbag inflators and may cost billions of dollars. The recall will last until the end of 2019 and take until 2020 to resolve.
Major recalls like these can be prevented through effective quality control in manufacturing. Some common tools used to support quality control include:
- Statistical process control (SPC) monitors and controls quality by tracking production metrics. It helps quality managers identify and solve problems before products leave the facility.
- Six Sigma uses five key principles to ensure products meet customers' needs and have zero defects.
When supported by lean tools like Total Productive Maintenance (TPM), 5S, and Kaizen, most if not all defects can be eliminated.
Benefits of Using Quality Control in Manufacturing
Customers expect and demand high-quality products. When customers receive quality products you will:
- Increase customer loyalty
- Gain repeat business
- Gain new customers from referrals
- Maintain or improve your position in the market
- Improve safety
- Reduce liability risks
- Contribute to overall positive branding of your product
Manufacturers with quality control procedures in place are far less likely to face product recalls or place customers at risk from poorly made products. The cost associated with these recalls can be steep. Testament to this is the Takata recall, which is estimated to cost the company between $7 and $24 billion.
Discover how you can avoid costly recalls and support your quality control system with TPM. DuraLabel Best Practice Guide to Total Productive Maintenance (TPM) will help you on the road to total quality. Improve quality, eliminate defects, and increase your profits.
Incorrect Implementation of Quality Control in Manufacturing
Quality control in manufacturing can be a little tricky. Often, it is done at the end of the production process, only catching defects after the fact.
Effective quality control is more involved and should include two levels:
- Operators monitor the manufacturing process and ensure that there is little variation.
- Engineers routinely monitor the product design for issues. When a problem is found, it is immediately fixed.
By monitoring products at the end of production as well as reviewing the products' design, companies can solve problems more efficiently, saving time and money.
Quality Assurance with Quality Control
Quality assurance streamlines production and helps to ensure that the final products meet the company's quality criteria. It ensures that the processes used to design, test, and produce products will be done correctly.
In manufacturing, quality assurance approaches, like ISO 9001, help manage and improve many processes, including:
- Acquiring raw materials
- Purchasing third-party components and sub-assemblies
- Designing and using inspection procedures
- Complying with production processes
- Responding to defects
For every business, quality assurance is different. However, ISO 9001 works for businesses both large and small and can be adapted for most any need. It provides the means for creating a lasting quality assurance program, ensuring that everything, from raw materials to inspection procedures are of the highest quality. Issues and defects from poor quality materials or third-party components are all but eliminated.
Quality Control, QA and Lean Manufacturing
Lean manufacturing tools can bolster your company's quality program. Lean revolves around improving quality and safety while increasing efficiency and profits. Some powerful lean manufacturing tools that can bolster your quality system include:
- TPM improves product quality by eliminating downtime, defects, and accidents. TPM accomplishes this through comprehensive maintenance programs and operator training.
- Kaizen helps eliminate problems at their source by empowering workers to find and solve problems on a daily basis. Download out Kaizen & PDCA Best Practice Guide.
- 5S helps organize and standardize the workplace. Take control with the 5S System Best Practice Guide, by Duralabel. Improve procedures and eliminate errors in your facility.
While every facility has different needs and may require a different lean tool, using lean to support quality control is essential. Procedures will be simplified, and the number of errors will be reduced.
Learn more about Kaizen and how it can help improve quality with this helpful video.
How to Implement Quality Control in Manufacturing
To implement an effective quality control program, first create and document your approach to quality control. This includes:
- Defining the quality standards for each product
- Selecting the quality control method
- Defining the number of products/batch that will be tested
- Creating and training employees for quality control
- Creating a communication system for reporting defects or potential issues.
Next, you will need to create procedures for handling defects. Consider the following:
- Will batches be rejected if defected items are found?
- Will there be further testing and potential repair work involved?
- Will production be halted to ensure that there are no more defective products created?
- How will new product versions be handled?
Finally, use a method like 5-Whys to identify the root cause of the defect, make any needed changes, and ensure your products are defect free.
Related Resources
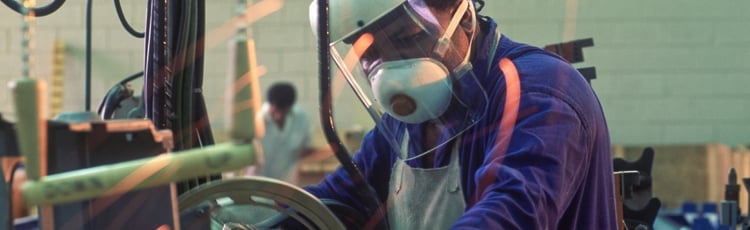
Toyota Production System
What Is the Toyota Production System and Why Does It Matter? TheToyota Production System(TPS) is a ...
Read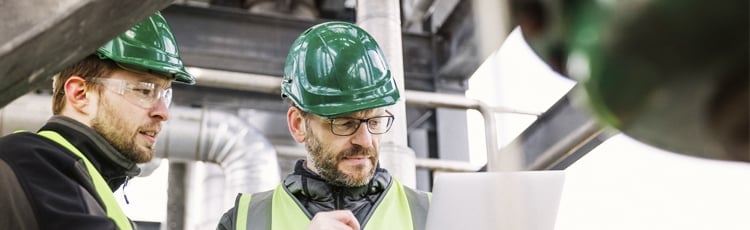
The Advantages of Lean Manufacturing: 5S, Kaizen, and TPM in Action
What Are the Advantages of Lean Manufacturing? Womack and Jones, in their book Lean Thinking, define lean ...
Read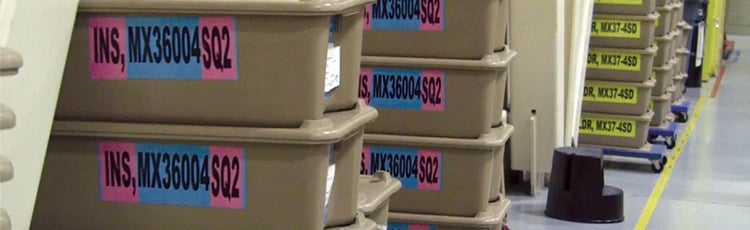
Lean Manufacturing Principles and The 5S System
What Are Lean Manufacturing Principles and Why Do They Matter? Lean manufacturing principlesare core ...
Read