5 Shocking Arc Flash Mistakes
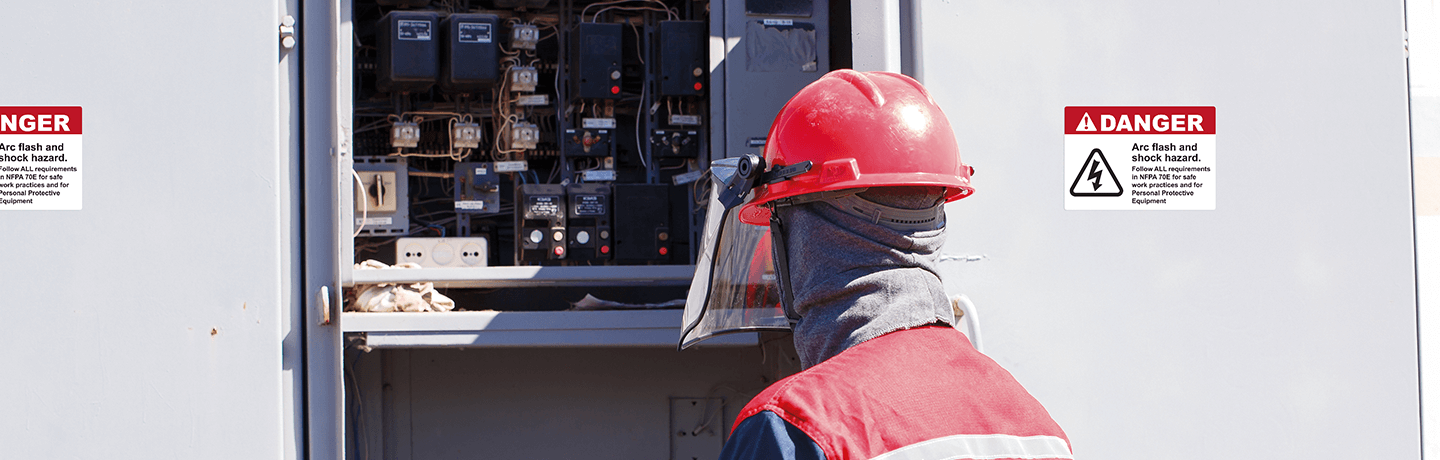
What is arc flash? Arc flash is a sudden burst of electrical energy that creates intense heat and light that can cause serious injuries and damage. The phenomenon of arc flash is a multistep process, but it can happen in a half-second and have severe and permanent consequences for a worker's life. Addressing this problem will take skill, responsibility, and expertise. Workplaces can easily start this process to master electrical safety and prevent injuries by avoiding these simple mistakes.
Arc Flash Power Points
1. Not Controlling Hazardous Energy
Taking electricity and safety for granted creates a serious risk and can spark an arc flash incident. However, it's easy to get complacent and skip important steps, such as lockout/tagout (LO/TO).
An efficient LO/TO program should include steps to follow before, during, and after work is complete. For electrical work, it should also follow the National Fire Protection Association (NFPA) 70E guidelines. What is NFPA 70E? The NFPA 70E standard covers shock and flash boundaries and gives tables for common situations to establish electrical safety in the workplace.
2. Not Updating an Arc Flash Analysis
An arc flash hazard analysis, using standardized steps, is fundamental to working safely on energized equipment. You may follow the NFPA 70 standard, or you can follow the more calculated IEEE 1584 standard. The IEEE 1584 standard offers an experimentally-derived calculation method. Even with these accepted standards, science is still improving, and professionals need to be aware of potential pitfalls.
"My major concern with the way arc flash analysis is done by most folks is that heat flux is not factored in when determining threshold incident energy to second-degree burn," said Michael Furtak, a certified engineering technologist and editor of ArcAdvisor.com.
OSHA's regulations provide the minimum acceptable arc flash requirements. For optimum electrical safety, workers should look beyond those requirements.
3. Poor Maintenance
As part of vigilant housekeeping, facilities should routinely evaluate electrical components and equipment for age, damage, and proper function. Many common pieces of equipment need periodic maintenance, which often is forgotten or ignored. Not only could sticky switches, old control panels, and loose wires be a potential arc flash hazard, they can also cause fires, short circuits, and other equipment failures.
4. Workers Lack of Training and Experience
Continuous arc flash incident training is important for any industry. Make sure electrical assessments, maintenance procedures, diagrams, and equipment specifications are up to date and easily accessible for the types of work that will be done. Make sure all workers are aware of high-voltage areas, electrical substations, and underground utility lines.
Communicate important messages through signs, labels, and employee training by using arc flash safety resources. Before any live work, have all affected workers read the energized electrical work permit; this way, they will know what tools they need for the job, including personal protective equipment, and have an opportunity to ask questions and voice concerns to be better prepared for an arc flash hazard.
A DuraLabel industrial label printer can be a very useful tool when creating tags that meet these arc flash requirements. In particular, the Toro Max and Kodiak Max can produce the right size, the right color labels, and meet the durability requirements.
5. Improper PPE and Communication
While personal protective equipment is the last line of defense for an arc flash incident, it's necessary to protect workers from electric shock and burns. Be sure it meets or exceeds the minimum arc rating (AR) for the situation, as assessed by your arc flash hazard analysis, and posted on your arc flash labels. Other signs and labels can help provide key information and reinforce safety in the face of electrical hazards. For example, mark arc flash boundaries and the clearances for electrical control panels by using floor tape.
DuraLabel Resources to Amplify Arc Flash Safety
Workplaces small and large can improve their electrical safety program with a few simple steps. Defending against electrical hazards such as arc flash requires attention to details, communication, and an ongoing commitment to safety best practices. Having preventative safety measures for electrical work in place optimizes total facility safety and efficiency.
Employers can improve their workplace arc flash safety signage with expert help from DuraLabel’s portable label printer Toro Max. It gives you the freedom to create signs compliant with industry standards and design custom labels to meet site-specific needs.
Whether you need safety signs, pipe markers, or equipment labels — the Toro Max Industrial Label Printer is ready to transport anywhere you are. Get help crafting a system that will provide the safety communication you need. Call 1-888-788-9936 and one of our experts will guide you through the process.
Learn more about electrical safety with the DuraLabel Electrical Safety Instant Action Guide. This guide will improve your warehouse electrical safety by meeting OSHA/NFPA arc flash requirements and utilizing visual communication. Download our free guide on electrical safety below.
Read Next:
Related Resources
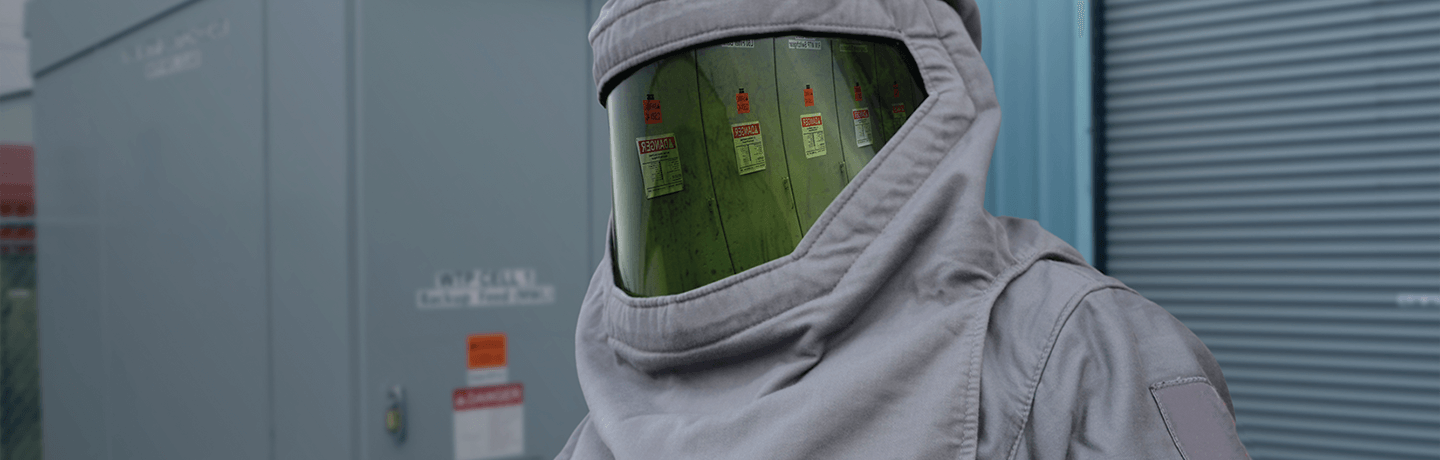
NFPA 70E Arc Flash with OSHA Signs
What is NFPA 70E? NFPA 70E, or the NFPA's Standard for Electrical Safety in the Workplace, outlines specific ...
Read
From Flash to Ash: Understanding Arc Flash Hazards and Prevention
What is Arc Flash? When it comes to electrical safety, arc flash is one of the most dangerous—and most ...
Read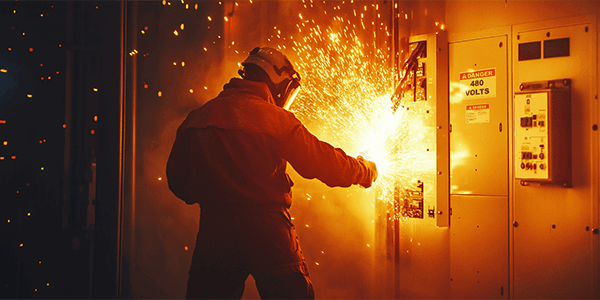
Arc Flash Labeling Essentials for Industrial Facilities & Field Teams
What Makes Arc Flash Labeling Essential for Electrical Safety? A loud explosion. A sudden flash of blinding ...
Read