Ammonia Refrigeration Safety Fundamentals: Pipe Marking and Beyond

Artificial cooling systems keep industry running, and many of these systems use anhydrous ammonia as a refrigerant. How do these ammonia refrigeration systems work? What are the hazards of ammonia refrigeration, and what can be done to keep workers safe?
Even though they both benefit from pipe marking, air conditioning (A/C) and artificial cooling systems are often used interchangeably but are different processes. A/C encompasses heating, ventilation, and humidity control, using refrigerants and a refrigerant pipe for comprehensive climate control, while cooling systems are mechanisms that focus on maintaining a desired temperature through methods like evaporative cooling.
Common types of artificial cooling systems include:
- Air conditioning systems
- Refrigeration systems
- Heat pumps
- Evaporative coolers
- Industrial chillers
Many of these systems use anhydrous ammonia as a refrigerant. How do these ammonia refrigeration systems work? What are the hazards of ammonia refrigeration, and how can pipe marking enhance workplace safety with the help of ammonia pipe labels?
Ammonia Refrigeration Systems 101
Refrigeration pipe systems use basic physics to move heat energy out of one area and into another, leaving the first area cooler than it was before. Here are some current uses for refrigeration systems:
- The refrigerator in a household kitchen does this to keep milk from souring.
- Indoor ice hockey rinks and grocery store freezer sections use the same process on a larger scale.
- Industrial facilities like petrochemical refineries and food processing plants rely on large-scale refrigeration pipe systems for their day-to-day operations.
The most common type of refrigerating system is a vapor-compression refrigerator. This approach uses a fluid called a refrigerant as the means of moving heat around. Most of the time, the refrigerant is a vapor. At one point in the system, it's compressed to become a liquid; later, it's allowed to expand and vaporize again. The process repeats on a cycle. Each time the refrigerant vaporizes, it absorbs heat energy from its surroundings, and each time it condenses, it releases that heat to its new location.
The physical properties of the refrigerant determine the pressure and temperature ranges of the system, along with the rate of cycling required for a given cooling effect. In turn, those details, often identified with piping labels, determine the efficiency of the refrigeration system.
Knowing which type of refrigerant to use is important. Many synthetic materials have been created as alternatives, however, chlorofluorocarbons (CFCs), such as Freon-12 were developed and widely used during the 20th century, until their destructive impact on the environment was discovered.
Why Ammonia Refrigeration?
In very large cooling systems, like those in food processing facilities, ammonia is a common choice of refrigerant. There are three major reasons for choosing ammonia as a refrigerant:
- Physical properties make it effective and efficient for large systems
- Breaks down quickly in the environment
- Spill or accidental release can be quickly identified
According to the International Institute of Ammonia Refrigeration (IIAR), ammonia is 3 to 10% more thermodynamically efficient than competitive refrigerants. This allows an ammonia-based refrigeration system to achieve the same cooling effect while using less power. As a result, where ammonia refrigeration is appropriate, it can offer lower long-term operation costs. Proper use of ammonia pipe labels ensures safe and efficient system operation.
Some advantages of using ammonia as a refrigerant include:
- Eco-friendly
- Uses less electricity
- Recognizable odor
Ammonia breaks down in the environment quickly, unlike synthetic refrigerants like Chlorofluorocarbons (CFCs). CFCs are nontoxic, nonflammable chemicals containing atoms of carbon, chlorine, and fluorine, and are used in the manufacturing of aerosol sprays, blowing agents, solvents, and refrigerants. CFCs are known to cause damage to the ozone layer.
Most of ammonia's potential for harm is due to there being too much of it in one place. While some refrigerants have no noticeable smell, ammonia smells pungent when it's about 20 parts per million (ppm) in the air. The detectable concentration is much lower than the concentration (5000 ppm) which will cause immediate harm.
Dangers of Ammonia Refrigeration
Ammonia’s properties are best suited for large refrigeration systems with detailed ammonia pipe labels, because there is likely to be a large amount of ammonia in any system that uses it. Any water in the system would freeze and obstruct piping, so ammonia refrigeration systems must use anhydrous ammonia (without water or other impurities).
The physics of vapor-compression refrigeration requires the system to use enough pressure to compress the gas into a liquid. Together, the refrigeration system uses a large amount of pure ammonia under high pressure.
As a result, any ammonia-based refrigeration system will present a risk of accidental exposure to high concentrations of ammonia, which could cause serious health concerns.
The Occupational Health and Safety Administration (OSHA) considers anhydrous ammonia to be a serious health hazard for the following reasons:
- It is corrosive to the skin, eyes, and lungs.
- Brief exposure can result in severe chemical burns.
- Exposure to concentration levels of 300 parts per million (ppm), or 0.03% can cause death or other health concerns.
- It is flammable at concentrations of approximately 15% to 28% by volume in air.
Preventing an Ammonia Leak
A process hazard analysis (PHA) is recommended when ammonia refrigeration is present in the workplace. A PHA consists of a careful review of potential problems, such as an ammonia leak, and what steps should be taken to prevent such an outcome. Conducting this analysis may raise awareness among employees, promote a mindful attitude about safety, and engender a proactive approach to hazard and risk assessment.
Requirements for PHAs can be found in 29 CFR 1910.119, OSHA's standard for Process Safety Management of Highly Hazardous Chemicals.
A PHA should include the following:
- Identify any hazards of the process.
- Identify any previous incidents that could have had potentially catastrophic consequences in the workplace.
- Outline any engineering and administrative controls that can be taken to lessen risks associated with the hazard.
- Break down the consequences should any engineering and/or administrative controls fail.
- Address any potential safety and health effects on employees in the event of failure.
Conducting a PHA is a key component of broader process safety management efforts. Read more about process safety management.
Ammonia Refrigeration Pipe System Safety
The risks involved with ammonia refrigeration can be reduced substantially by careful management, maintenance, and pipe marking. Part of that process is clear labeling of the pipes and equipment being used. As the accepted industry experts in this field, the IIAR maintains a code of recommendations for refrigeration equipment labeling.
IIAR Bulletin No. 114 has been the main resource for the ammonia refrigeration industry since the 1990’s, however, a new standard came out in 2021 known as IIAR 2-2021 where guidance on ammonia refrigeration pipe labeling is now referenced.
According to the new standard, all piping labels should contain the following:
- The pipe marking color should be Safety Orange.
- The word ‘AMMONIA’ should be printed in black letters.
- The physical state ‘LIQ’ or ‘VAP’ should be printed in approved colors.
- The relative pressure ‘HIGH’ or ‘LOW’ should be printed in the approved colors. 70 pounds per square inch gauge (PSIG) is the cutoff between high and low pressure.
- The service abbreviation should be printed in black letters. Common abbreviations include:
- CD: Condenser Drain
- HPL: High Pressure Liquid
- HTRL: High Temperature Recirculated Liquid
- HTRS: High Temperature Recirculated Suction
- HTS: High Temperature Suction
- HGD: Hot Gas Defrost
- RV: Relief Vent
- A flow direction arrow should indicate the direction of flow in the pipe.
Ammonia Refrigeration System Pipe Marking Label Requirements
Ammonia refrigeration systems require clear and precise pipe labeling to ensure safety and compliance with industry standards. According to the ANSI/ASME A13.1 pipe marking standard, pipes carrying ammonia must feature labels with an orange background and black text, clearly indicating the contents and flow direction. These ammonia pipe labels must meet the guidelines set forth in IIAR Bulletin No. 114, which provides detailed specifications for the size, color, and placement of ammonia pipe labels. Proper labeling is crucial for the safety of personnel, enabling quick identification of hazardous contents and aiding in emergency response efforts.
This comprehensive, industry-specific pipe labeling system needs to be used consistently for the best results. DuraLabel offers an ammonia pipe marking reference chart describing the IIAR's system. Using this chart can help your facility maximize its safety and efficiency, while you take advantage of the power of ammonia refrigeration. Begin addressing hazards with IIAR standards with our free Pipe Marking chart.
DuraLabel Pipe Marking Solutions for Ammonia Refrigeration
DuraLabel offers pipe labeling solutions tailored specifically for ammonia refrigeration pipe systems. With a focus on safety and compliance, DuraLabel's products are designed to meet and exceed industry standards, including ANSI/ASME A13.1 and IIAR Bulletin No. 114. Our high-quality piping labels feature durable materials that withstand the harsh conditions typical in refrigeration environments, ensuring longevity and readability.
The DuraLabel Toro Max Orange Ammonia Pipe Marking Kit is an all-in-one solution perfect for ensuring your ammonia refrigeration system is clearly and accurately labeled. The kit includes the DuraLabel Toro Max Printer, known for its user-friendly interface and portability, making on-site label creation effortless. The ammonia pipe labels feature an orange background with black text, adhering to regulatory standards and providing high visibility for quick identification.
The DuraLabel Toro Max Orange Ammonia Pipe Marking Kit is equipped with labels that resist chemicals, moisture, and extreme temperatures, ensuring they remain legible and intact over time. The software, LabelForge PRO, included with the Toro Max streamlines the label creation process, allowing for customization to meet your specific pipe labeling needs.
Not sure how to begin labeling your ammonia refrigeration pipe system? Contact a DuraLabel representative at 1-888-402-8820 and they can help you get started.
Read Next:
Related Resources
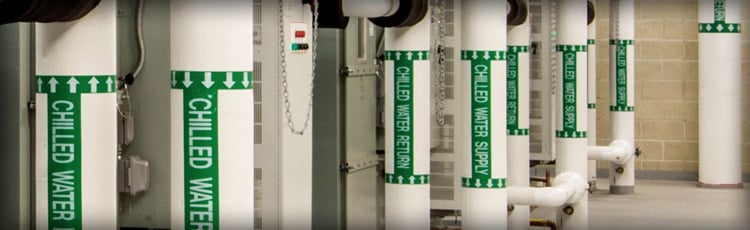
Modern HVAC Safety and Efficiency Essentials
The heating, ventilation, air conditioning, and refrigeration industry is heating up as demand grows, new ...
Read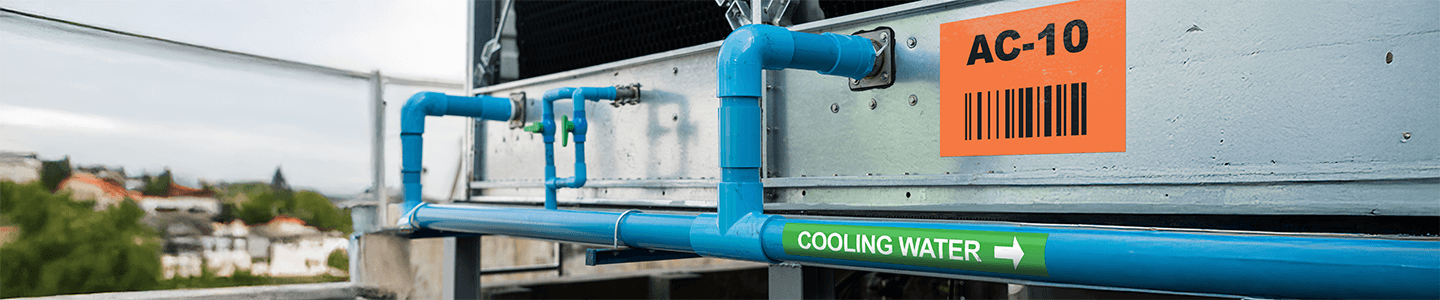
8 Essential HVAC Installation Tips to Prevent Costly Mistakes
HVAC Installation Done Right: 8 Essential Tips to Prevent Costly Mistakes A poorly installed heating, ...
Read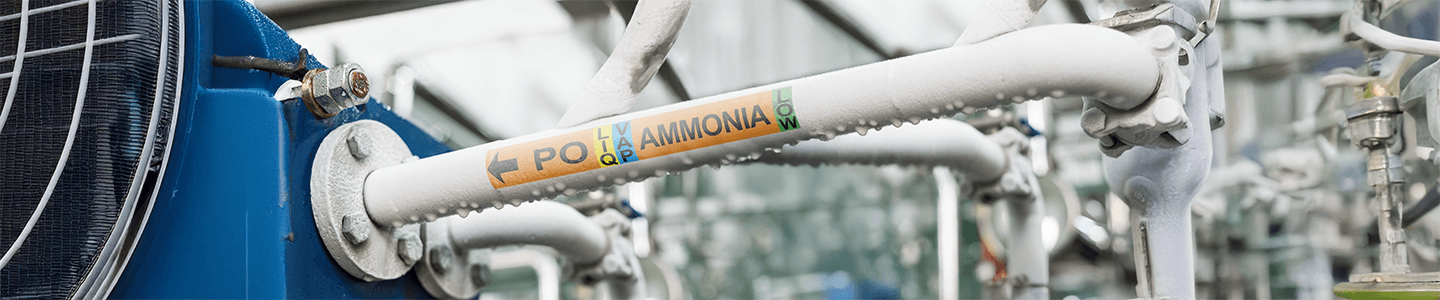
What New HVAC Codes Means for A2L Refrigerants in 2025
What Are A2L Refrigerants? A2L refrigerants are a class of chemicals defined by ASHRAE Standard 34 as having ...
Read