OSHA Lockout/Tagout: A Key Electrical Safety Measure Often Overlooked

Imagine crawling into a conveyor machine to get to a crucial component. If that machine isn't turned off properly, the results can be catastrophic. While OSHA lockout/tagout (LOTO) seems like a simple enough safety system to follow, there are thousands of violations each year and injuries and deaths from failure to use it. Why do these types of violations appear so frequently on the Occupational Safety and Health Administration (OSHA) Top 10 list each year? Workplaces can take better control of LOTO by understanding several key problems and how to mitigate them.
What Is OSHA 1910.147?
OSHA Standard 1910.147 outlines specific requirements for disabling machinery or equipment during maintenance or servicing to prevent the unexpected release of hazardous energy. This standard applies to a wide range of energy sources—including electrical, mechanical, hydraulic, pneumatic, chemical, and thermal—that could harm workers if not properly controlled.
Key elements of 1910.147 include:
-
Establishing and enforcing an energy control program
-
Developing machine-specific lockout/tagout procedures
-
Training employees on their roles (authorized, affected, and other)
-
Conducting periodic inspections of energy control procedures
Complying with OSHA lockout/tagout is critical not just for meeting regulations but for improving electrical safety labels use, effective electrical panel labeling, and overall safety accountability.
Lockout/Tagout Violations: What the Latest OSHA Statistics Reveal
According to OSHA’s Top 10 Most Frequently Cited Standards for 2023, Control of Hazardous Energy (Lockout/Tagout) ranked sixth with 2,539 violations. That’s a 23% increase from 2020’s 2,065 violations—showing that lockout/tagout violations are not only persistent but growing.
Many workplaces struggle with consistent training, electrical panel labeling, and clear communication. OSHA reports that proper lockout/tagout compliance can prevent an estimated 120 fatalities and 50,000 injuries each year. These numbers highlight the real-life consequences of failing to apply proper electrical safety labels and procedures.
What Do Workers and Safety Managers Have to Say About LOTO and Its Misuse?
LOTO policies and procedures often look good on paper, but what happens in the field can tell a very different story. To understand where the disconnects are, it helps to hear directly from those responsible for implementing and following lockout/tagout procedures every day.
On Profit Pressure and Shortcuts
“For a lot of workplaces, it's all about profits. In the past place where I've worked, they didn't want to stop machines or mold pours and such, and maintenance would be done while they were running. It's not efficient when you look at it from today's standards.”
—Amir Murabi, Safety Manager, Colorado
On Bureaucracy Overload
“When there is more paper than process, that is annoying. If you need to jump through two hoops vs. 10 hoops. Same goes for daily pre-shift type inspections.”
—Daniel Cardenas, Safety Manager, California
On Improper Closeout
“Deisolating equipment and closing out the paperwork but not logging it on the register. So, if it was audited, it would show still isolated in the register, but in fact, it was deisolated weeks ago.”
—Gabriel Velasco, Safety Expert, Michigan
On Confusing Rules Across Sites
“Different places have different rules, but it's really not that complicated, although they try to make it seem like it is. Partly because the places, different plants, etc. seem to make it sound like it's more complicated than it is, and the workers feel over pressured and get confused.”
—Buddy Norton, Industry Expert, Texas
On Pencil-Whipped Paperwork
“I just did an audit on our LOTO policy. I found all of the paperwork to be perfect. Almost too perfect, as if it had been pencil whipped. I spent a week following the crews around (openly) and reviewed the procedure as they were going through it. They were actually doing exactly what they were supposed to be doing. My biggest peeve is when the policy is not used as intended and the paperwork is pencil whipped.”
—Michael Hleback, Safety Expert, Ohio
These quotes offer valuable insights into the real-world challenges of LOTO compliance—from inconsistent processes and confusing rules to cultural pressures and paperwork pitfalls. Listening to those on the front lines can help shape better policies and training that truly work.
Addressing Human Factors in OSHA Lockout/Tagout Failures
Even well-written OSHA lockout/tagout procedures are vulnerable to human error. Workers may skip steps, mislabel energy sources, or rely too heavily on memory—risking serious LOTO violations. Common issues include:
Common behavioral pitfalls:
-
Time pressure or unrealistic expectations
-
“Shortcut” culture driven by past habits or peer influence
-
Overconfidence in one’s ability to safely work around energized equipment
-
Lack of engagement due to dry, repetitive training sessions
What helps:
-
Build a culture where stopping for safety is respected and rewarded
-
Include real-world examples and consequences in training
-
Use interactive, hands-on demonstrations and site-specific scenarios
-
Encourage peer accountability and feedback
How Electrical Safety Labels and Electrical Panel Labeling Support Compliance
Clear communication tools—such as durable electrical safety labels, electrical panel labeling, custom signage, and floor markings—help workers identify energy sources quickly and comply with OSHA LOTO standards.
Benefits of visual communication tools:
-
Reinforces proper lockout/tagout steps at the point of use
-
Reduces confusion around which energy sources need to be isolated
-
Helps temporary or rotating staff follow correct procedures
-
Supports ongoing training and quick visual audits
Workplaces can even add QR codes to equipment labels to link directly to LOTO procedures or video demonstrations.
DuraLabel Resources for LOTO Safety and Compliance
Lockout/tagout violations continue to rank among OSHA’s most cited workplace safety issues. DuraLabel offers industrial solutions that simplify compliance with OSHA LOTO through durable electrical safety labels, reliable electrical panel labeling, and easy-to-use industrial labeling software.
For worksites that need rugged, on-the-spot labeling, the DuraLabel Toro Max Industrial Sign and Label System delivers unmatched versatility and power. This all-in-one, portable thermal transfer printer lets teams create custom lockout tags, warning signs, and equipment labels right at the job site—no PC connection required. With its upgraded performance and durability, Toro Max keeps your labeling program compliant and adaptable wherever work happens.
LabelForge PRO, DuraLabel’s powerful industrial labeling software, comes pre-installed on the Toro Max to give teams everything they need for fast, compliant labeling. With built-in templates, compliant symbols, and flexible layouts, it lets users create custom LOTO tags, equipment-specific procedures, and safety signage directly from the system—streamlining energy control communication and helping reduce lockout/tagout violations.
Want to improve safety and compliance? Explore LabelForge PRO industrial labeling software, or download the free Arc Flash Labeling Quick Start Guide today. Call 1-888-965-3359 to speak with a safety professional about your labeling needs.
Read Next:
From Flash to Ash: Understanding Arc Flash and Preventing Them
Miswired and Mislabeled: The Electrical Errors That Could Cost You
Related Resources
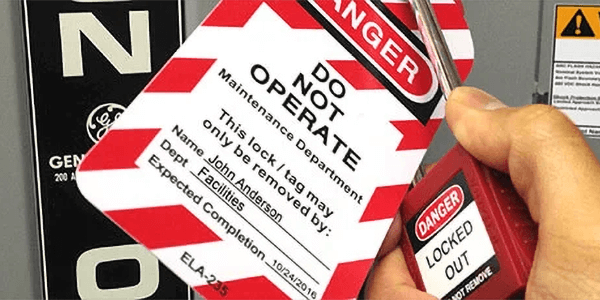
How to Prevent Arc Flash with Lockout Tagout Signs and Safety Labels
What Are the First Steps to Preventing Arc Flash in the Workplace? In the realm of electrical safety, the ...
Read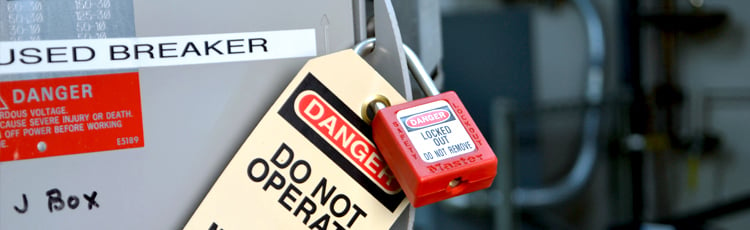
Lockout Tagout (LO/TO) Program
The numbers are staggering: Lockout-Tagout (LOTO) violations are consistently among OSHA's 10 most common ...
Read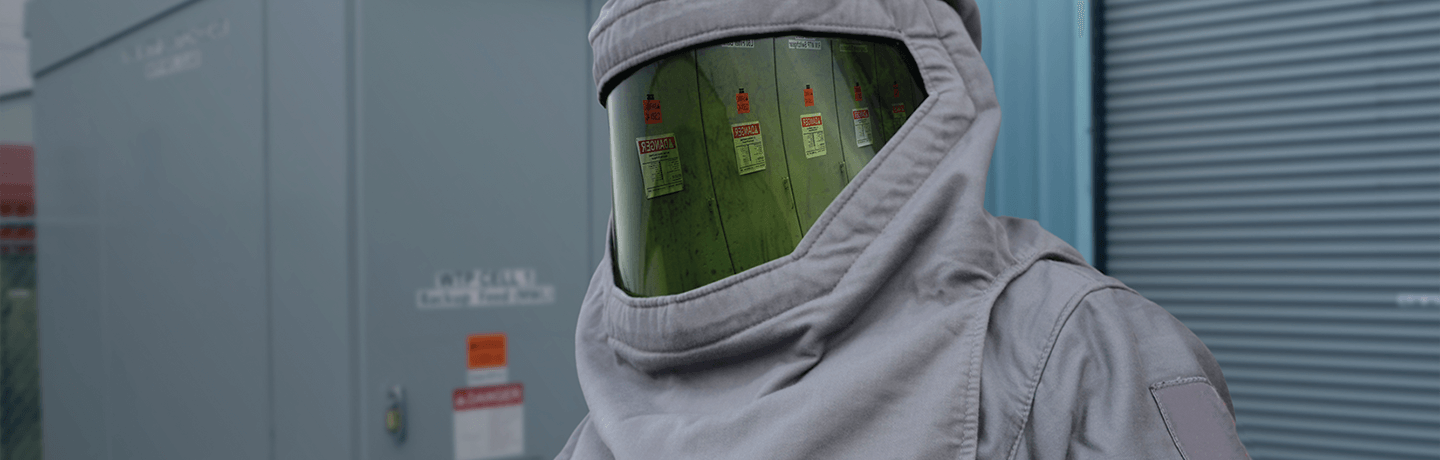
NFPA 70E Arc Flash with OSHA Signs
What is NFPA 70E? NFPA 70E, or the NFPA's Standard for Electrical Safety in the Workplace, outlines specific ...
Read