Linking Lean and Visuals
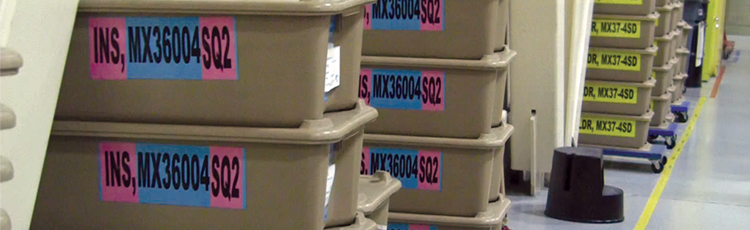
The visual workplace and lean are two distinct yet complementary tools that can improve work processes, make work easier, and reduce costs. Lean is a series of tools that can be used to reduce cycle time, eliminate wasted motion, minimize errors, and simplify work processes. The language that supports the lean transformation is the visual workplace. Gwendolyn Galsworth, creator of the visual workplace, defines it as "a self-ordering, self-explaining, self-regulating, and self-improving work environment-where what is supposed to happen does happen, on time, every time, day or night." The visual workplace accomplishes this by using visuals such as labels and signs to communicate important information throughout the workplace.
When used together in a thoughtful, strategic way, they create a workplace where positive change is not only repeatable but also sustainable.
Benefits of the Visual Workplace
The visual workplace provides many benefits to businesses. These benefits include:
- Clarifying the work across all departments
- Revealing vital information and making it accessible with visuals
- Building a work culture of continuous improvement
- Anchoring lean principles and practices into the physical workspace
To this end, McKinsey Global Consulting reports that lean has a shelf life of only three to five years without the stabilizing capability of visuals. Afterward, lean begins to erode, and with it, the benefits of quality, speed, and pull. Galsworth calls the relationship between lean and visual the visual-lean? alliance. Each requires the other to reach its potential and provide the greatest benefit.
Let's look at a prime example of how Total Productive Maintenance (TPM) and the visual workplace work together.
The Role of Lean in TPM
When lean is deployed as a system, it takes on every aspect of the organization and drives out waste- from purchasing and receiving to design and fabrication, in offices and on the production floor. The methods in the lean tool box are designed to search out and destroy inefficiency and ineffectiveness on all operational levels. TPM, for example, focuses on equipment. It focuses on improving the effectiveness of equipment, based on your company's needs.
TPM accomplishes this on many equipment levels. Some involve your maintenance department but others require engineers, purchasing, field staff, and operators to participate as well. Well-known sub-targets include:
- Equipment life-cycle cost
- Quick changeover
- Preventive maintenance
- Equipment updates and enhancements
Another key element is autonomous maintenance, which requires operators to undergo special training so they can perform routine maintenance as part of their work. This includes learning how to spot problems or potential problems before breakdowns occur. Any issues are reported to the company's maintenance staff.
The Role of the Visual Workplace in TPM
Shigeo Shingo, master practitioners and co-architect of the Toyota Production system, once said, that people forget, and more importantly they forget that they forgot.
This is where visuals become critical. No matter how well-trained or well-intentioned, people need assistance from visuals to help them consistently remember their tasks. Visuals can help operators:
- Identify and verify machine status and performance.
- Spot equipment abnormalities.
- Track their maintenance tasks so everyone can see their timely completion.
- Track and share any problem or potential problem they spot along the way.
When visuals become part of the process, operators automatically know what to do. They can do their jobs using the information they see.
This process begins when operators take the information that is often hidden in binders or someone's head and draw the info out to make it part of the workspace. They translate the previously hidden information into visual standards, placing them at or near their point-of-use. These standards help change the pattern of work and include:
- Start/stop, speed/feed instructions
- Daily and weekly maintenance and inspection points
- Match marks to verify, for example, chain tension, bolt tightness, and sprocket wear
- Good-to-go gauge markings for pressure, temperature, speed, and so on
- Lubrication points directly on the machine
- Lubrication diagrams near or on the machine
- Color-coded zerk fittings and grease guns
- Oil level indicators
With just a glance, operators can tell if the pressure is OK, where they need to lube equipment, and when they need to add more oil to the machine. The information, hidden in complicated charts and manuals, has been transformed and made part of the work space. The result? Workflow is streamlined, procedures are followed, and mistakes and errors are eliminated. TPM is sustained.
Visual Workplace Solutions
Every visual should be designed to provide information where it is lacking. To accomplish this, every visual solution should take several things into account:
- Visuals should convey the exact information needed.
- Visuals should be placed where they are needed and where they will be seen.
- Visuals should support or enhance workflow.
The workplace must be understood: how work is done in the space, which tools are used, and where they are located. Are items where you need them most? Or do you frequently move from one station to the next, looking for tools and supplies?
Duralabel' array of DuraLabel printers, labels, and signage can help you make lasting visual solutions. Labels and signs help indicate what things are and where they belong, as well as provide essential safety information throughout the workplace. Some common uses include:
- Marking bins, racks, and other storage locations
- Identifying equipment, tools, and supplies to improve asset tracking, item history, and more
- Identifying the steps required to perform tasks that are frequently done incorrectly
- Creating safety signs and labels to meet federal, state, and local requirements
Remove uncertainty and help improve workflow by ensuring workers can quickly find the information they need. With the Visual Workplace implemented, time is no longer wasted looking for information that may be hidden. Information is at the point-of-use, where companies, employees, and eventually the consumers, need it most.
Related Resources
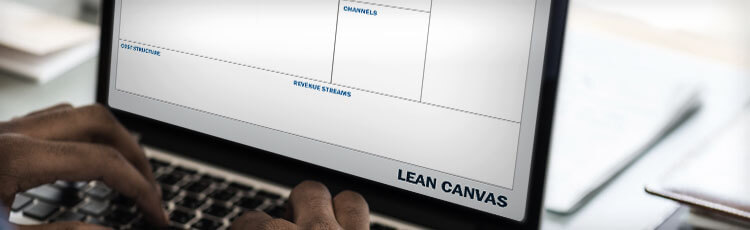
Lean Canvas
Compared to writing a business plan, which can take several weeks or months, you can outline multiple ...
Read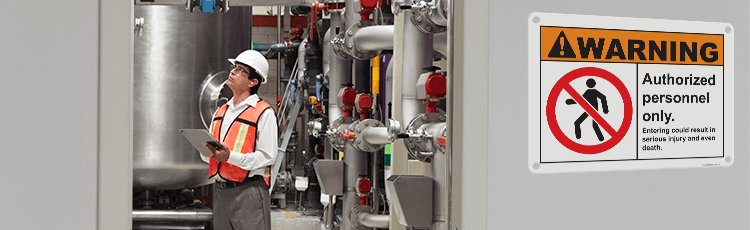
Got a Need for Speed? Here Are 5 Ways to Increase Productivity Without Sacrificing Safety
Safety is an essential element of any facility's success. The real challenge is how to maintain productivity ...
ReadSIPOC
SIPOC is an acronym for Suppliers, Inputs, Processes, Outputs, and Customers and shows how these business ...
Read