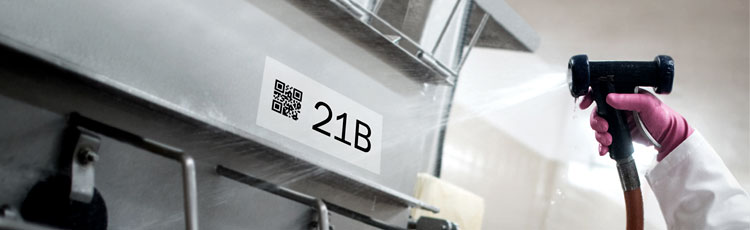
Thousands of freshly plucked chickens move through a conveyor line in Fremont, Nebraska. At this large facility, workers rapidly process the chickens to prepare them for cutting, weighing, and packing before being sent to stores throughout the United States. To keep pace with today's demands, more U.S. poultry processing plants such as this are going high tech and are highly efficient. Part of that efficiency lies in simplifying maintenance and increasing worker safety, which in turn produces poultry processing success.
The Challenges of Poultry Processing
Poultry processing is a fast-paced and complex operation. With high demands for production, facilities must manage multiple challenges.
These include:
- Maintaining proper sanitation to prevent contamination
- Ensuring machine safety
- Reducing the risk of worker injury
According to the National Chicken Council, Americans eat roughly 101.1 pounds per capita. This makes chicken the number one protein consumed in the United States. To meet this growing demand, poultry processing plants are ramping up production with advanced technology and streamlined operations. These efforts ensure a consistent supply to retailers and maintain food safety standards across the industry.
OSHA and USDA Compliance
Poultry processing facilities in the U.S. must follow strict regulatory standards for the safety of both workers and food products. Two key agencies, the Occupational Safety and Health Administration (OSHA) and the U.S. Department of Agriculture (USDA), enforce rules that impact day-to-day operations in these plants.
OSHA’s regulations focus on worker safety, covering critical areas such as machine safety and chemical handling. Poultry processing plants are required to implement safety protocols like Lockout/Tagout (LOTO) procedures to prevent machines from being accidentally powered on during maintenance. They are also required to label hazardous chemicals like ammonia, commonly used in refrigeration systems. OSHA also mandates the use of personal protective equipment (PPE), including hearing protection, respiratory gear, and ergonomic supports, all of which help reduce the risk of injury in a noisy and physically demanding environment.
The USDA’s regulations, on the other hand, are geared toward food safety. These guidelines require that processing facilities implement stringent sanitation practices to avoid contamination of poultry products. Facilities must establish Hazard Analysis and Critical Control Points plans, which identify key points in the production process where food safety risks can occur, and implement controls to minimize those risks. Proper labeling and clear communication of safety measures are vital in upholding compliance with these standards.
Failure to comply with these regulations can result in severe penalties, including fines, shutdowns, or recalls, which can impact a company's bottom line and reputation. To stay ahead, many poultry processing plants rely on comprehensive safety programs and visual communication tools to maintain compliance. Visual labels, signs, and pipe markers help workers stay informed about hazards and safety protocols, contributing to a safer and more efficient workplace.
Technological Advancements for the Poultry Industry
New technology is reshaping poultry processing, providing better solutions to enhance safety. Automation systems help minimize direct human contact with hazardous machinery, while sensors and monitoring devices detect potential safety breaches in real-time. Some facilities have implemented robotic systems to reduce worker exposure to dangerous tasks, such as repetitive lifting or working with sharp cutting tools. Digital tracking systems also help ensure compliance with safety protocols by monitoring key operational areas and equipment conditions.
Introducing new systems and technology for poultry production has its challenges, but the benefits outweigh the stress, according to Walt Shafer, project manager at Lincoln Premium Poultry. He shared his advice and experience in a recent article in Nebraska Farmer magazine.
"The biggest challenge is really [that] no one knows poultry," Shafer said. "Growers get intimidated by this technology, but we have service personnel that will work with them for as long as they're raising birds with us."
For example, massive bird raising barns are all automated and controlled by computer, which makes managing weigh cells, temperatures, water, and other reporting functions easy, even from afar.
Enhancing Safety in Poultry Processing Facilities
Poultry processing steps are swift. Activities include working around rapid conveyor systems and other machines, harsh cleaning regimens using chemicals, workplace noise, slippery floors, and other potentially hazardous activities. From animal handling to product quality testing and facility sanitation, workers must navigate these operating procedures quickly to limit downtime for maximum efficiency. Common hazard controls include:
- Maintaining walking and working surfaces to help prevent slips, trips, and falls.
- Communicate protocol around dangerous equipment so that all workers understand risks.
- Follow OSHA standards for chemicals and process safety management, including proper pipe marking for ammonia.
- Control design and maintenance of systems using an effective LOTO program.
- Mark active working areas near machines and equipment with visual boundaries to protect other workers and visitors nearby.
- Keep the facility tidy through thorough sanitation and organized in case of an emergency.
- Provide personal protective equipment, including hearing conservation tools, ventilation methods, and ergonomic assistive devices.
With the implementation of newer equipment, some poultry processing facilities have an edge in hazard mitigation, however, adhering to strict timelines can still be challenging for workers. Many facilities see the value of using digital lean manufacturing strategies while maximizing facility safety using visual workplace management.
DuraLabel Solutions for Poultry Processing
As poultry processing facilities continue to evolve, worker safety and operational efficiency remains a top priority. Meeting high production demands while protecting employees from hazards requires the right tools and strategies. DuraLabel offers a range of solutions designed to help facilities overcome these challenges and comply with industry regulations.
DuraLabel’s durable signs, labels, and floor markings play a critical role in promoting safety. High-visibility signage helps communicate important protocols around machinery and chemical hazards, while durable labels provide proper identification of pipes, storage areas, and hazardous substances like ammonia. These visual safety cues help prevent accidents and guide workers through potentially hazardous environments.
With DuraLabel printers like the DuraLabel Kodiak Max Industrial Sign and Label Print System, facilities can easily create custom labels and signs tailored to their specific needs. The Kodiak Max's versatility make it ideal for the fast-paced demands of poultry processing plants. Its ability to produce labels that withstand harsh cleaning chemicals, extreme temperatures, and moisture ensures long-lasting performance in tough environments. From marking equipment and machinery to designating safe walkways and emergency exits, DuraLabel’s solutions contribute to a safer, more organized workplace.
For more information on how DuraLabel products can improve safety and efficiency in your facility, download our free Facility Signage Handbook. From compliance to improving communication, this handbook provides key information to make informed decisions about your facility's signage.
Read Next:
OSHA Signs Regulations and Compliance: Everything You Need to Know
Ammonia Refrigeration Safety Fundamentals: Pipe Marking and Beyond
Related Resources
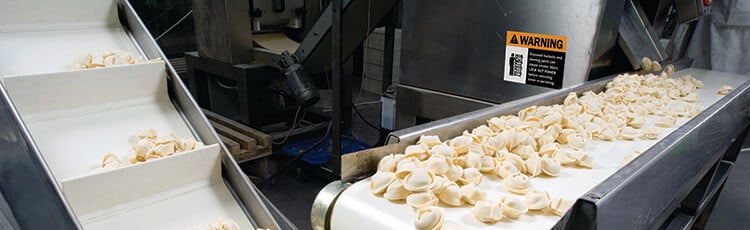
Avoiding Hazards in the Food Processing Industry
Journalist and activist, Upton Sinclair, revealed the horrors of the food processing and manufacturing ...
Read
Boosting Workplace Efficiency with Clear, Strategic Labeling
Efficiency is essential for productivity, safety, and smooth operations in any workplace. One ...
Read
Ammonia Accidents Threaten Worker Safety, Business Operations
Year after year, anhydrous ammonia accidents kill workers and cause severe financial penalties to businesses. ...
Read