What’s the Real Cost of Failing to Meet OSHA Safety Standards?
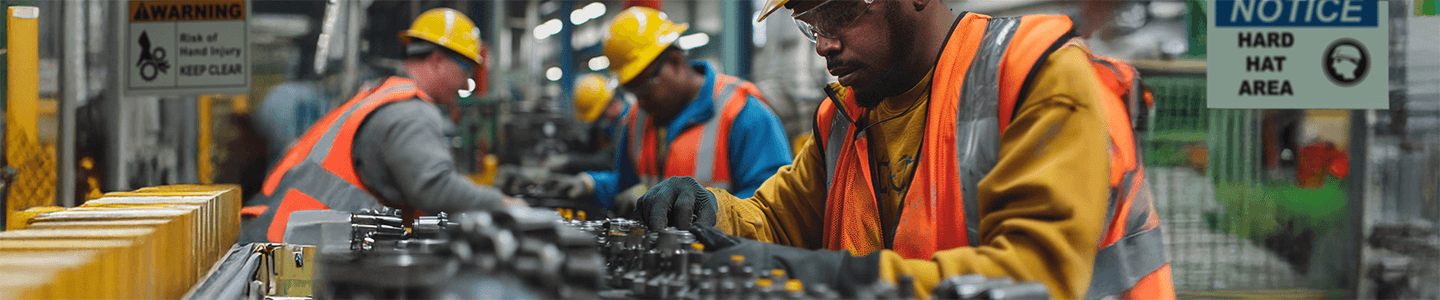
A workplace safety incident can have far-reaching consequences. In an instant, operations can grind to a halt, injuries can change lives, and businesses are left dealing with the aftermath. The U.S. Bureau of Labor Statistics (BLS) reported 2.6 million nonfatal workplace injuries and illnesses in 2023, highlighting how common these incidents are.
Companies that fail to prioritize Occupational Safety and Health Administration (OSHA) regulations face more than just fines. Operational losses, legal liabilities, and reputation damage can take years to recover.
Regulatory compliance is about more than just preventing fines—it protects employees and keeps business operations on track. Let’s explore what happens when a serious safety incident occurs and how proactive measures, including OSHA labeling solutions, help reduce risk and support compliance with OSHA regulations.
Immediate Impact: Chaos and Operational Disruption
When a serious safety incident occurs, the aftermath is often chaotic and overwhelming. Operations shut down, employees are shaken, and management scrambles to respond. The response can be broken into several key areas:
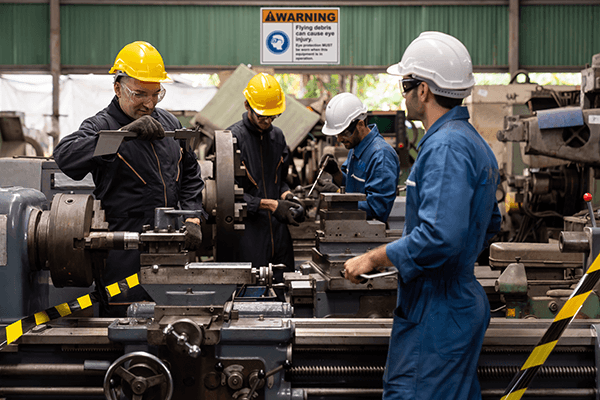
Operational Shutdown
One of the first steps, after an incident is to shut down operations. This is necessary to resolve any safety concerns and allow space for an investigation. Depending on the incident, a production line or even an entire facility may remain idle for days or weeks. For example, if a machine guarding failure results in a serious injury, OSHA inspectors may require the affected area to stay offline until the investigation is complete and corrections are made.
Extended downtime impacts production schedules, delays customer commitments, and hurts revenue. Even businesses with contingency plans struggle to recover from prolonged operational delays.
OSHA Inspection Process
After a serious incident, OSHA conducts an on-site inspection by following these steps:
- Preparation—OSHA compliance officers review the inspection history, examine current operations, and gather necessary protective equipment for testing instruments.
- Presentation of Credentials—The compliance officer presents official credentials, including a photo and serial number.
- Opening Conference—The officer explains the reason for the inspection, its scope, and procedures, while the employer selects a representative to accompany them. Employees may also have a representative present and can be interviewed.
- Walkaround—The officer inspects the workplace for hazards, reviews injury records, and ensures OSHA posters are displayed. Inspectors will look for violations of OSHA regulations, such as missing safety guards, inadequate signage, or improper lockout/tagout procedures.
- Closing Conference—The officer discusses findings with the employer and employee representatives, outlining possible actions, including informal conferences, contesting citations, or using consultation services.
Inspections often expand beyond the initial incident area, uncovering additional safety violations that can result in new citations and costly fines. Inspectors can review records, interview employees, and assess training programs to ensure compliance with occupational safety standards.
Employee Well-being
Safety incidents affect employees beyond physical injuries. After witnessing or experiencing a serious workplace injury, workers often feel anxious or fearful about returning to their jobs. This drop in morale negatively affects productivity and increases employee turnover.
Rebuilding trust requires visible improvements regarding worker safety. Clear visual communication through OSHA-compliant labels and safety signs is one step in helping reassure employees that management is taking action to prioritize their well-being.
Financial Consequences and OSHA Regulations Fines
Safety incidents come with significant financial consequences. While many focus on the direct cost of OSHA fines, the hidden costs often cause greater long-term damage.
Breakdown of OSHA Fines
Violations of OSHA regulations carry hefty fines depending on the severity.
- Serious violations—Over $16,000 per instance.
- Willful or repeated violations—Over $165,000 per instance.
For a business already dealing with downtime and lost revenue, these fines add to their financial strain like a crushing blow.
Hidden Costs of Safety Incidents
Beyond fines, businesses often face a range of indirect costs related to:
- Medical expenses and compensation for injured workers
- Legal fees from lawsuits and settlements
- Increased insurance premiums that can remain elevated for years
- Equipment repair or replacement
For example, a forklift collision due to missing OSHA safety signs can result in hefty repair costs, downtime, and lost productivity while repairs are made.
Legal Ramifications
Legal consequences can escalate quickly after serious incidents. Injured employees may pursue legal action, and in some cases, the business could face criminal charges if negligence is proven. Settlements or court judgments can cost hundreds of thousands or even millions of dollars.
Rebuilding Trust After Reputational Damage
A damaged reputation often takes longer to recover from than financial losses. Severe injuries or fatalities draw public attention. This negative publicity lingers in customers’ minds and erodes their trust.
Customer and Partner Perception
In industries such as manufacturing, construction, or energy, safety directly affects reliability. A serious safety incident may cause customers and business partners to reevaluate their relationships.
Internal Trust and Morale
Employees want to feel safe at work. When a company’s occupational safety standards fall short, trust declines. High turnover and lower engagement follow. Rebuilding trust takes time, but an effective way to accelerate the process is by enhancing visual communication with OSHA labels and safety signs, ensuring clear, consistent messaging that reinforces safe work practices
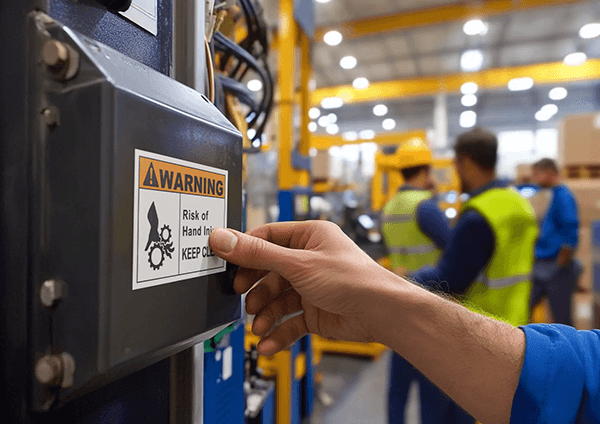
The Role of OSHA Safety Standards in Compliance
OSHA safety standards protect workers and reduce incidents. Compliance creates a safer work environment while helping businesses avoid costly citations.
Some of the most critical OSHA regulations focus on machine guarding, fall protection, hazardous materials, and lockout/tagout procedures. Businesses that follow these standards reduce the risk of incidents and avoid costly citations.
Role of Visual Communication in Compliance
Clear communication is a cornerstone of workplace safety. OSHA labels and safety signs help workers identify hazards and follow safety protocols. Common examples include:
- Hazardous chemical labeling to comply with HazCom 2012 standards
- Machine safety labels indicating pinch points or rotating parts
- Exit signs and emergency evacuation labels for clear egress during emergencies
Training and Employee Engagement
Compliance goes beyond proper labeling. Regular safety training reinforces procedures and empowers employees to identify hazards and report issues. Visual tools like OSHA labeling then support these lessons on the floor.
DuraLabel Helps Build a Safer Future with OSHA Labeling Solutions
No company wants to face the fallout of a serious safety incident. While the aftermath can be challenging, businesses can reduce risks by taking proactive steps. Building a strong safety culture and using OSHA-compliant labeling solutions are key parts of that effort.
DuraLabel print systems and supplies help businesses create custom labels and safety signs that support compliance with OSHA regulations. From chemical storage to equipment safety, DuraLabel printers make it easy to create durable, on-demand labels for any workplace hazard. Tough-tested supplies ensure labels stay legible and effective in harsh environments, keeping employees informed and reducing the chance of violations.
Need help choosing the right signage? Download DuraLabel’s free Facility Signage Handbook for guidance on compliance requirements and product recommendations. Have specific questions? Call a DuraLabel support rep at 1-888-695-5670 for personalized assistance!
Read Next:
Related Resources
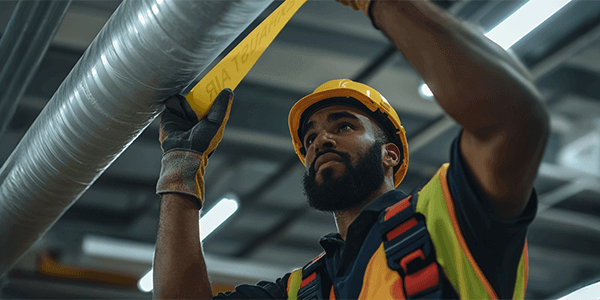
Why Custom Industrial Labels Matter for Mechanical Job Sites
How Do Custom Industrial Labels Improve Safety and Organization on Job Sites? Mechanical job sites are ...
Read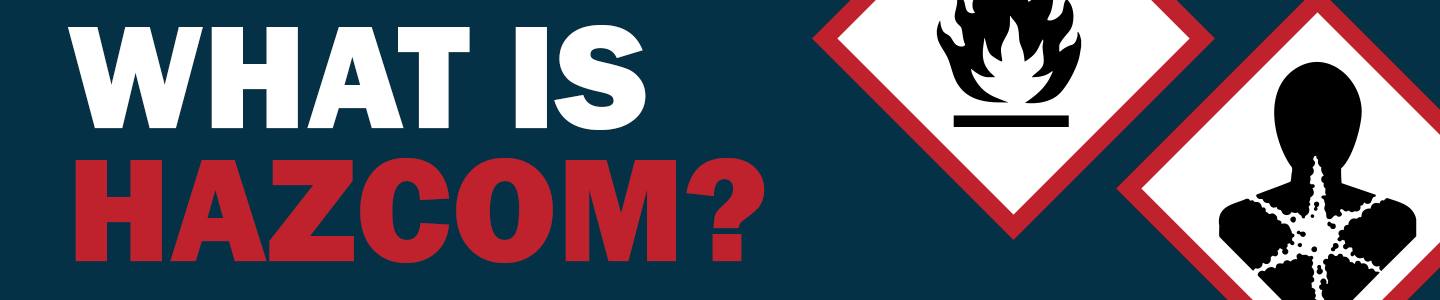
What is HazCom? Your Guide to Chemical Labeling, GHS, & OSHA Standards
What Is OSHA’s Hazard Communication Standard (HazCom)? "HazCom" is short for "Hazard Communication," OSHA’s ...
Read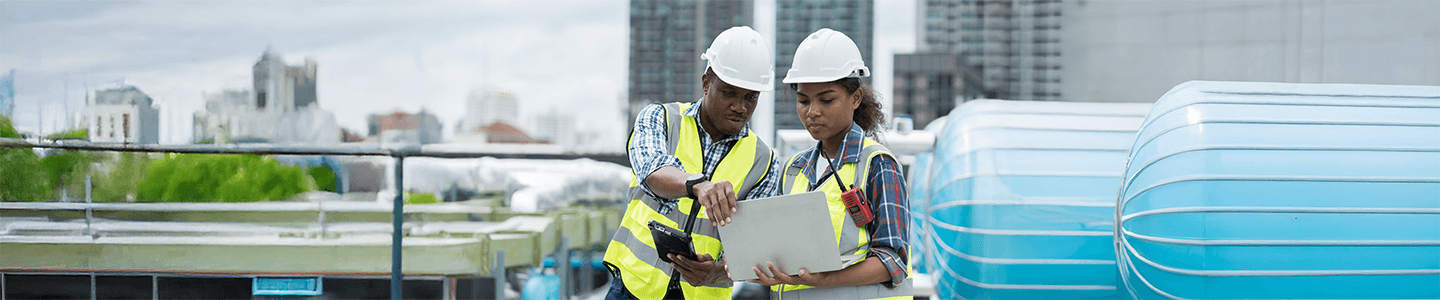
Top 5 Challenges Mechanical Project Managers Face
What Are the Biggest Obstacles Mechanical Project Managers Face? Mechanical project managers oversee ...
Read