Importance of Lockout Tagout Training to Reduce Arc Flash

Machines inevitably break down and need to be serviced. It's not enough to just "shut them off" and make repairs. According to the Occupational Safety and Health Administration (OSHA), machines need to have power sources removed and be locked out, tagged out (LO/TO) and isolated from the source to prevent serious injury from electrical hazards like arc flash.
Many serious accidents have happened when someone thought a machine was safely shut off. LO/TO is a way to protect yourself and others from an electrical explosion by ensuring that machines remain completely, temporarily off.
A positive attitude about safety empowers everyone in the workplace. Injuries and fatalities can be prevented and losses in production time can be minimized while profitability can be increased.
While manufacturers today are very focused on cutting costs and improving production efficiency, there's no need to sacrifice employee safety. The consequences of not being in compliance with safety regulations are drastic — penalties, fines, damage to image, plant shutdown and fatalities from electrical arc flash. A safe operation minimizes downtime, which offers the least possible interruption in business.
To create change in workplace culture and reduce arc flash, organizations need to have a long-term vision for machine and plant safety.
That's why it is more important now than ever to generate awareness for LO/TO and educate a broad business audience about LO/TO procedures, best safety practices and the wide range of LO/TO products and services available. LO/TO regulations and appropriate personal protection equipment (PPE) protect employees who work around equipment that can create an electrical arc flash.
Combating Arc Flash Throughout the History of LOTO
OSHA put the federal standard, 1910.147 in place in 1989. While the purpose of LO/TO hasn't changed, the complexity of the equipment has increased. With complex PLC-linked interlocks, remote computer controls, light curtains, automatic valves and other machine automation accessories commonplace, both workers and facility managers need to be kept up to speed on current developments to ensure an arc flash doesn't occur.
The Control of Hazardous Energy Source Standard (OSHA 29 CFR 1910.147), which is more commonly known as the LO/TO Standard, is a Federal Occupational Safety and Health Administration (OSHA) program. It was created to prevent the unexpected start-up or energizing of equipment during service and maintenance operations which could cause employee injuries from an electrical explosion and prevent the release of stored energy which could cause employee injury.
OSHA LOTO Standards That Prevent Arc Flash
To comply with OSHA standards, companies must draft a written LO/TO plan which includes the scope and purpose of techniques to be used to control hazardous energy like an electrical arc flash.
The Five Main Causes of LO/TO Injuries, according to the Oklahoma State University EHA, are:
- Failure to stop equipment
- Failure to disconnect from power source
- Failure to dissipate residual energy
- Accidental restarting of equipment
- Failure to clear work areas before restarting
Whether you are a facility manager, a foreman or a machine operator and whether you work in a chemical plant, a pharmaceutical plant, a university, a government agency or in the military, you need to know about LO/TO for electrical explosion prevention. Certainly, the types of machines and energy sources will vary between plant types. Copper mines use large excavating equipment powered by electricity. Offshore platforms use large gas turbines powered by natural gas. Your specific safety considerations are industry, application, and site-specific, but might include the following tasks and applications:
- Replacing belts on compressors, ventilation equipment, shop machines
- Disassembling pump couplings to replace/repair motors or pumps
- Maintaining electric/hydraulic recycle balers and trash compactors
- Boiler repair
- Working on vehicle engines and drive trains
- Changing saw or chipper blades
- Replacing light ballasts
- Clearing conveyor jams
So why would anyone be reluctant to follow LO/TO guidelines even if it means avoiding an arc flash? These common "excuses" all relate to productivity.
- An employee is required to clear a jammed machine several times each day and locking out the machine would drop product onto the floor
- Performing LO/TO to change the tape roll inside a box machine would result in data loss to a programmable logic controller
- Programming a robot must be conducted inside the robot cell while the robot remains energized
Even those workplaces that have established LO/TO processes face challenges that can still create an electrical explosion, including:
- Lack of specific procedures written for each piece of equipment identifying all energy sources and energy isolation devices
- Lack of comprehensive safety training for everyone in the workplace.
- Incorrect tag use
- Inappropriate lock use
- Working under someone else's lock
- Communication. Employees need to let the next shift operators know via operator worksheets that work has been finished. When uncertain, production may halt causing thousands of dollars of losses in output.
Again, consider the benefits of LO/TO:
- Minimizes exposure to injury if machines are accidentally started
- Minimizes exposure to injury in unexpected releases of hazardous energy, such as steam blasts, corrosive chemical, and electrical arc flash
- Saves lives
- Minimize exposure to litigation
- In some states, companies receive benefits and discounts on worker's compensation if they have few accidents
- Making safety a top priority inspires employee confidence and trust
- Profitability
Arc Flash Solutions from DuraLabel
Easily design and print arc flash labels and safety signs any time you need them, onsite or in the field with the capable Kodiak Max. This printer also serves as an excellent facility-wide industrial labeling system to print signs and labels for all kinds of applications and environmental conditions indoors and out.
Get help crafting a system that will provide the safety communication you need. Call 1-888-820-4631 and one of our experts will guide you through the process.
Conduct an arc flash risk assessment and create your own labels with guidance from our arc flash labeling guide. It's important to periodically evaluate your facility for electrical safety and ensure all labels are up to date to keep workers safe and your facility operating smoothly.
Learn more about arc flash labeling with the DuraLabel Arc Flash Labeling Instant Action Guide. This guide will improve safety on your site, as well as walk you through how to create effective arc flash labels for your entire site. Download our free guide on Arc Flash Labeling below.
Read Next:
Related Resources

How to Improve Arc Flash Safety in Mining Operations
Mining operations depend heavily on electrically powered equipment—including drills, shovels, conveyors, and ...
Read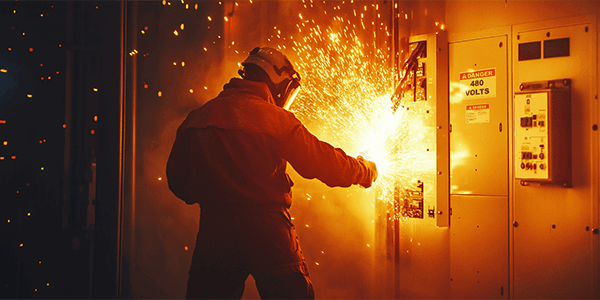
Arc Flash Labeling Essentials for Industrial Facilities & Field Teams
What Makes Arc Flash Labeling Essential for Electrical Safety? A loud explosion. A sudden flash of blinding ...
Read
Steps for Arc Flash Safety and Security in Electrical Substations
Electrical substations truly have the power. In the wrong hands, that power is dangerous. That's why it's ...
Read