What Is Lean Manufacturing
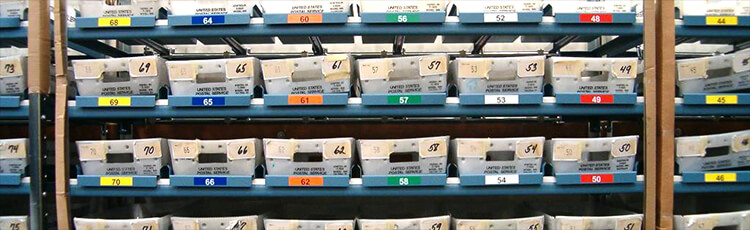
Lean is an efficient approach to running a process, business or organization to minimize waste, lower lead times, reduce overhead and the amount of costly resources.
Lean manufacturing incorporates methods such as Kaizen, 5S and Kanban. It was originally developed by Toyota in the 1950's and became known as the Toyota Production System (TPS). TPS is not the only approach to lean. Other methods, such as Six Sigma which was developed by Motorola, can be also used to create a lean business.
Is "lean" just for manufacturing?
While it was initially created as a way to improve production with limited resources, lean can be applied to any part of a business or organization. Lean methods can be applied to an office, service company, or even a non-profit organization or church. Lean is all about finding better ways to do things, so that they require less effort, less time and fewer resources.
What are the benefits of lean manufacturing?
In a nutshell the benefit is reducing waste. All types of waste. Implementing lean will uncover types of waste you never knew existed. For example:
- Material Handling Waste - Lean manufacturing will simplify material handling. It will reduce the distance materials are moved, the number of times they are moved, the amount of material moved, and the labor/equipment required to handle materials. Cost reductions of up to 90% are not unusual.
- Human Resources Waste - Lean manufacturing simplifies communications and reduces the amount of information that needs to be transferred. The transfer of information becomes quick, simple and informal. Coordination of work is simplified, reducing supervisory time. Because of its focus on a cell structure, lean builds teams and fosters cooperation. Employees can see the result of their work, are more involved in the overall process, and have the opportunity to be involved in a wider range of skills. The result is higher production, less employee stress, and a higher level of employee job satisfaction (people enjoy their work more).
With the reduction in waste you'll be able to produce more products using the same facilities and employees-reducing or eliminating the need for capital expansion projects. - Reduction In Inventory - A key part of lean manufacturing is that it reduces inventory. Inventory has associated costs such as: capital costs, warehousing costs, loss due to damage, material handling costs and overstock costs. With lean the objective is to have the right amount of inventory, in the right place, at the right time.
A reduction in inventory also has less obvious benefits. For example, it makes it much easier to spot problems in the production of components and parts. If there is a problem that results in a component defect, because there is not a large inventory of that component, the defect will be discovered sooner-before large quantities of the defective component are made. - Lean also benefits your customer - With lean your customers will see faster, more reliable deliveries. The quality of your products will improve, and you'll be able to respond to the special needs of individual customers-increasing the quality of service you provide. Lean puts the focus on the customer, resulting in a better customer relationship and improved communications.
Related Resources
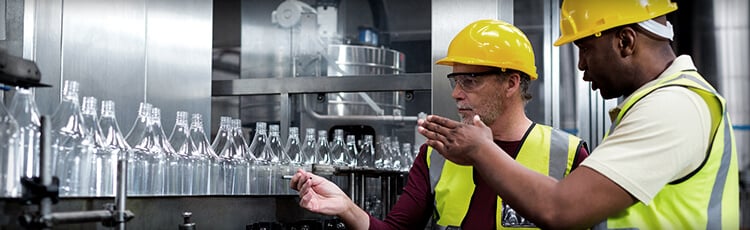
How to Improve Quality Control in Manufacturing with Lean and 5S
What Is Quality Control in Manufacturing and Why Does It Matter? In manufacturing, quality control is a ...
Read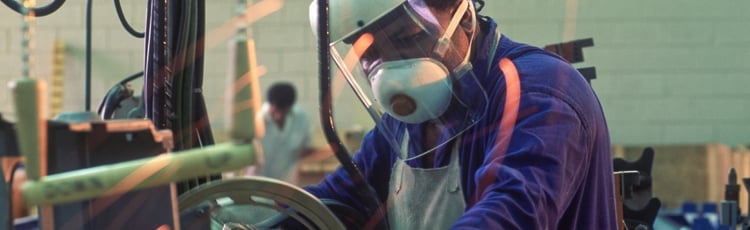
Toyota Production System
What Is the Toyota Production System and Why Does It Matter? TheToyota Production System(TPS) is a ...
Read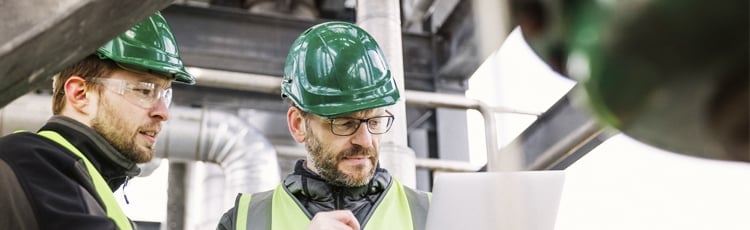
The Advantages of Lean Manufacturing: 5S, Kaizen, and TPM in Action
What Are the Advantages of Lean Manufacturing? Womack and Jones, in their book Lean Thinking, define lean ...
Read