5S Examples in Action: The Good, the Bad, and the Successful

Can 5S Improve Efficiency and Engagement Across Industries?
The 5S system is a proven method for improving efficiency, but its impact depends entirely on how it is applied. In environments where 5S is aligned with real operational needs and introduced with collaboration and purpose, teams see measurable gains in productivity, safety, and morale.
The following 5S success and failure stories illustrate how this Lean tool works in practice—and where it can fall short.
Apply 5S as a Problem-Solving Strategy
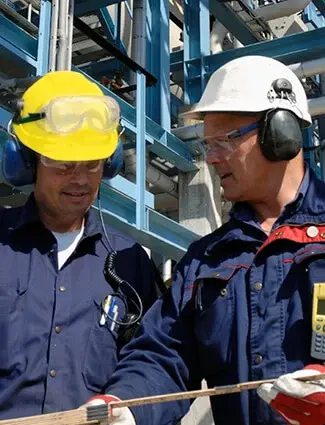
5S is most effective when used to address specific operational issues rather than implemented as a generic checklist. The goal isn’t to make spaces look cleaner—it’s to make them function better. A problem-solving approach ensures that each phase of 5S directly supports your team’s daily work.
Dearborn Mid-West Company (DMC) provides a textbook example of a successful 5S implementation. DMC started by looking at their engineering process and considering how tasks could be completed more efficiently. The company used the 5 Whys method to uncover root causes of inefficiency and mapped solutions directly to each 5S step:
-
Sort: Identified and eliminated redundant engineering steps
-
Set: Reordered task sequences to improve clarity and flow
-
Shine: Introduced quality checks to catch issues earlier
-
Standardize: Documented consistent procedures for all teams
-
Sustain: Embedded 5S thinking into everyday culture
This case study highlights how 5S can be a problem-solving lean tool when applied correctly to address inefficiencies at their root cause.
Avoid Common 5S Pitfalls in Office Environments
Even well-intentioned 5S initiatives can backfire when they’re applied without flexibility or context. Offices, in particular, require tailored solutions that reflect how different roles and workflows operate. Without this nuance, 5S risks becoming performative rather than productive.
A common misuse of 5S in office environments is when companies enforce rigid organization rules without considering the actual needs of employees, the origination, or the principles of visual communication.
For example, a company looking to improve efficiency decides to implement 5S across all office desks. A consultant recommends that every desk must have the same tools, removing any unique or personal items. Labeling is enforced, and compliance reviews are scheduled to ensure that the workspace remains uniform.
The result? Decreased morale, slower workflows, and zero improvement in efficiency. This kind of blind application is a common 5S implementation pitfall. When visual workplace tools aren’t aligned with how people actually work, they become distractions—not assets.
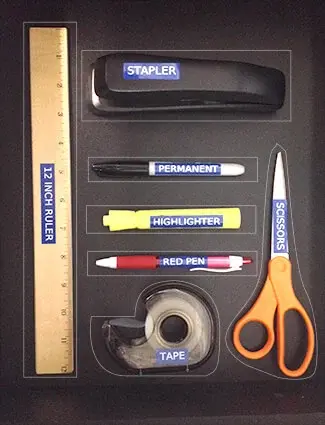
What's wrong with this picture?
Shigeo Shingo, one of the architects of Toyota’s lean system, emphasized the importance of asking 'why' repeatedly to break through status quo thinking. Rigidly enforcing a 5S process without asking 'why' fails to address real inefficiencies.
For example, "Why should every desk be the same when employees have different tasks and work styles?" A standardized toolset may limit certain employees’ ability to work effectively, causing unnecessary delays and frustration. 5S should be flexible and adapted through communication between management and employees to maximize efficiency while maintaining workplace organization.
Each application of 5S needs to be targeted to address issues of efficiency and cost. 5S is meant to be flexible and can be adapted for each department through open and meaningful communication among management and employees.
Understand Why 5S Succeeds or Fails
What separates lasting 5S results from short-lived efforts? It often comes down to how the system is introduced and supported. Leadership mindset, team involvement, and communication methods all play critical roles in determining success or failure.
The difference often comes down to leadership approach. Top-down mandates rarely stick, but collaborative efforts grounded in training, communication, and visual reinforcement deliver better outcomes.
Build 5S Commitment Through Collaboration
When 5S is treated as a shared responsibility, employees are more likely to see the value and participate fully. Total employee involvement is critical for long-term success in 5S implementation is treated as a shared responsibility, employees are more likely to see the value and participate fully. Collaborative planning and iterative feedback make each phase of 5S more grounded in actual workflow needs.
In successful 5S examples, leadership and employees:
-
Work together to identify inefficiencies
-
Co-create labeling and layout systems that support real tasks
-
Use feedback loops to refine visual systems over time
By developing solutions that account for both the big and the small picture, employees and management are more likely to see the positive changes and commit to 5S as part of the workplace culture.
Recognize the Risks of Mandated 5S
In contrast, when 5S is implemented as a mandate from leadership without team engagement, it often leads to confusion and resistance. Without proper training or clear reasoning, employees may misunderstand the purpose of each phase and miss opportunities for genuine improvement.
A common misconception about 5S implementation is that it is simply a cleaning exercise. However, Shine is not about tidiness—it is about identifying process inefficiencies. Employees who are not properly trained to recognize the signs of inefficiencies, such as material buildup, equipment wear, or leaks, may miss critical warning signs that could lead to costly failures.
When approached as a problem-solving philosophy, to improve all aspects of the workplace, 5S shows its strength. This lean tool must be properly implemented with open, clear communication at all times. To avoid 5S failure, companies must prioritize training, problem-solving, and employee engagement, ensuring that 5S is perceived as a valuable tool rather than an imposed regulation.
DuraLabel 5S Labeling Resources
Visual cues are a core component of 5S. They guide behavior, reduce ambiguity, and make standards obvious at a glance. A visual workplace supports efficiency and safety, and makes it easier to onboard new team members and maintain consistency across shifts.
To maximize the success of your 5S program, having effective visual communication is crucial. Whether you’re launching a new program or correcting a misfire, DuraLabel’s Industrial Sign and Label Systems can assist in developing clear, impactful signage that reinforces 5S principles in your workplace.
Our industrial labeling tools and DuraLabel Kodiak Max 5S kits are built for demanding applications, from warehouse floor layouts to tool identification and safety signage. Combined with intuitive software and expert guidance, we help teams make their 5S system clear, consistent, and sustainable.
Ready to move forward with confidence? Download the 5S Quick Start Guide to explore real-world 5S success and failure stories and learn how to build a program that works for your team.
Want direct support? Call 1-888-965-3359 to speak with a DuraLabel specialist about warehouse labeling for 5S and visual solutions that drive measurable performance.
Read Next:
Related Resources
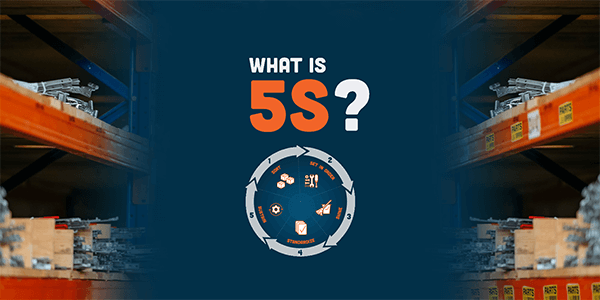
The 5S System Explained: From Origins to Implementation
What Is the 5S System? The 5S system is a lean manufacturing tool that improves workplace efficiency and ...
Read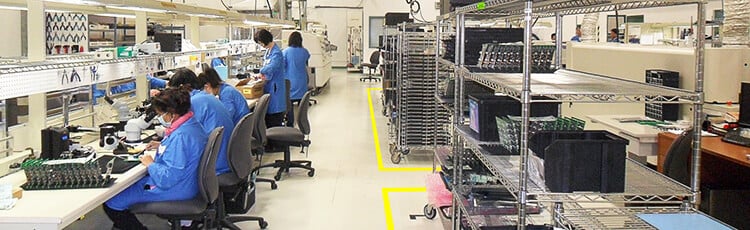
Lean Manufacturing and the 5S System
What is 5S in Manufacturing? 5S is a lean manufacturing method used to eliminate waste, improve workplace ...
Read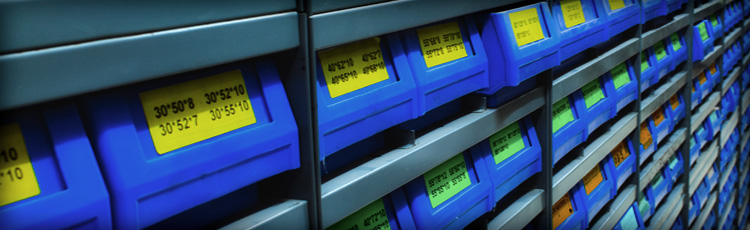
Creating a Visual Factory with the 5S System
What Is a Visual Factory with the 5S System? The term "visual factory" refers to an approach to lean ...
Read