How to Improve Arc Flash Safety in Mining Operations

Mining operations depend heavily on electrically powered equipment—including drills, shovels, conveyors, and crushers. Power stations, motor control centers (MCCs), mobile substations, and E-houses are distributed across extensive areas of a mining site.
Electrical systems power nearly every critical function in a mining operation. To protect workers, the Mine Safety and Health Administration (MSHA) outlines electrical safety requirements in Title 30 CFR, Part 56, Subpart K. However, these regulations do not specifically cover arc flash hazards or reference NFPA 70E—the standard widely adopted in other industries for electrical safety.
How should mining operations manage the unique risks of arc flash if they are not mentioned?
Understand the Risk of Arc Flash in Mining
What is an arc flash? An arc flash is an explosive burst caused by an uncontrolled electrical arc. These blasts can reach temperatures of 35,000°F and occur in less than a second. The intense heat and pressure can vaporize metal, destroy equipment, and cause fatal injuries.
Even experienced workers are at risk. In a recent six-month period, 11 miners suffered injuries due to electric arc flashes, according to MSHA's 2024 safety alert.
Arc flash incidents often result from poor maintenance, equipment failure, or unsafe work practices. Without a formal arc flash program, mining sites leave workers vulnerable to catastrophic injury—and costly downtime.
The next step is understanding how to evaluate and reduce these risks through a formal arc flash risk assessment.
Start with an Arc Flash Assessment
To reduce arc flash hazards, safety managers must first complete an arc flash risk assessment. This evaluation—outlined in NFPA 70E—helps identify potential dangers and determine the level of protection workers need.
During the assessment, safety personnel gather critical data and analyze electrical systems to:
-
Collect equipment specifications and electrical ratings
-
Identify system modes of operation
-
Calculate bolted fault and arc fault currents
-
Document voltage levels and equipment classes
-
Determine arc flash boundaries
-
Evaluate the incident energy for each piece of equipment
-
Identify required personal protective equipment (PPE)
-
Review the protective characteristics of overcurrent devices
-
Define working distances and safety parameters
A thorough risk assessment provides the foundation for safe procedures, proper labeling, and PPE selection. It also lays the groundwork for a site-wide arc flash safety program.
Train Miners in Arc Flash Safety
Training plays a key role in reducing arc flash incidents. Any worker who may be exposed to energized equipment must know how to identify hazards, wear the correct PPE, and follow site-specific procedures.
Effective arc flash training should cover:
-
How to identify arc flash hazards
-
How to safely work on energized equipment
-
How to select and wear arc-rated PPE
-
How to follow lockout/tagout (LOTO) procedures
Site-specific training ensures workers understand the unique risks in their environment. Safety teams should review training at least once per year and after any major system changes.
Lockout/tagout training should also prepare workers to:
-
Follow LOTO steps for each piece of equipment
-
Recognize locked-out equipment to prevent accidental re-energization
-
Restore power safely and correctly
Regular, targeted training gives workers the knowledge and confidence to work safely around electrical systems.
Implement a Site-Wide Arc Flash Safety Program
A structured arc flash safety program strengthens electrical safety and reduces the likelihood of serious incidents. After completing a risk assessment, organizations should use the data to establish consistent, site-wide safety procedures.
An effective arc flash safety program includes the following elements:
-
Defined procedures for working on energized and de-energized systems
-
Clear identification of required arc-rated PPE by task and equipment type
-
Established approach boundaries and minimum safe work distances
-
A standardized labeling system that communicates arc flash hazards at the point of risk
-
Ongoing training and recertification for personnel exposed to electrical hazards
-
Documentation for assessments, training records, equipment data, and procedural updates
The program should reflect actual working conditions and remain adaptable to operational changes. Treating the arc flash program as a living system supports continuous improvement and maintains compliance with evolving safety standards.
Maintain and Update the Arc Flash Program
Mining environments change frequently. Equipment upgrades, system reconfigurations, and process adjustments can all affect arc flash risk. Each change requires a fresh evaluation of the arc flash program to maintain safety and compliance.
Labeling plays a central role in this process. When equipment is added, replaced, or modified, arc flash labels must reflect the updated incident energy levels and protection requirements. Outdated or inaccurate labels can lead to serious injuries and regulatory violations.
Program updates should also include revised system documentation, re-evaluated PPE requirements, and retraining for affected personnel. Workers rely on clear, up-to-date labels to understand the hazards in their immediate environment. Maintaining accurate labeling across the site strengthens safety communication and helps align the program with NFPA 70E and MSHA expectations.
The Critical Role of Arc Flash Labels
Arc flash labels deliver immediate, visual warnings that help workers recognize hazards before beginning a task. In high-risk environments like mining, clear labeling can be the difference between a safe procedure and a serious incident.
Each label should communicate essential details, including voltage, incident energy levels, required PPE, and approach boundaries. When placed directly on panels, MCCs, and other energized equipment, these labels provide workers with the information they need.
Accurate labeling also supports compliance. NFPA 70E requires arc flash labels on equipment where an arc flash hazard exists, and inspectors often rely on these labels to assess whether safety programs meet regulatory standards.
Maintaining high-quality, up-to-date labels helps standardize communication across departments, reinforces training, and protects workers during routine maintenance, troubleshooting, and emergency repairs.
DuraLabel Arc Flash Solutions for Mining
A well-maintained arc flash program depends on accurate, visible labels. When electrical systems change, labeling must keep pace. DuraLabel provides the tools mining operations need to update arc flash labels quickly and consistently.
The DuraLabel Toro Max Industrial Sign and Label System offers a rugged, mobile printing solution built for industrial environments. The Toro Max allows teams to print compliant arc flash labels onsite—without returning to an office or waiting on third-party suppliers. Labels can be customized to display incident energy levels, required PPE, approach boundaries, and other critical safety details.
For even faster labeling, the pre-installed LabelForge PRO software streamlines the process with preloaded arc flash templates, built-in compliance standards, and centralized data management.
To streamline arc flash labeling across a site, contact a DuraLabel representative at 1-888-411-3520. For additional guidance, download the free Arc Flash Labeling Quick Start Guide, designed to support safe, accurate labeling from assessment to application.
Read Next:
Miswired and Mislabeled: The Electrical Errors That Could Cost You
Related Resources
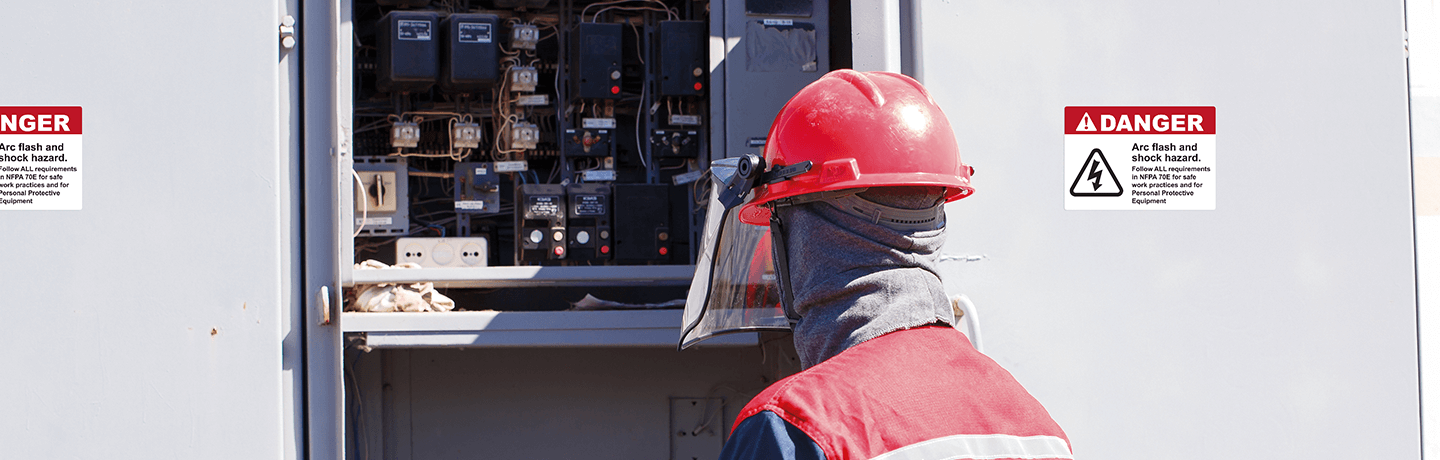
5 Shocking Arc Flash Mistakes
Everyone knows arc flash is dangerous and the hazards that come with electrical work. However, sometimes ...
Read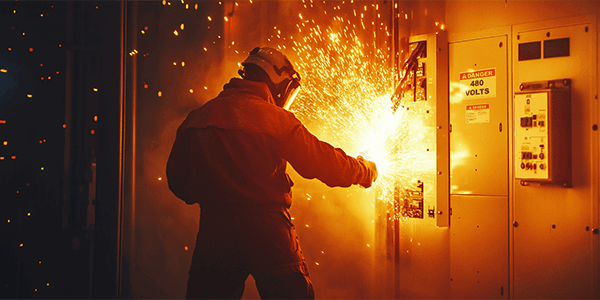
Arc Flash Labeling Essentials for Industrial Facilities & Field Teams
What Makes Arc Flash Labeling Essential for Electrical Safety? A loud explosion. A sudden flash of blinding ...
Read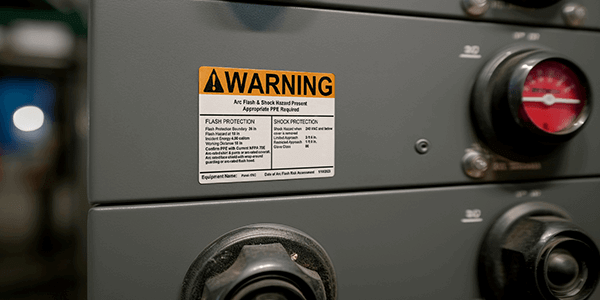
Arc Flash Labels and Safety Tips for Understanding Flash Hazards
What Are Arc Flash Labels and Why Are They Important? Arc flash labels are essential for communicating ...
Read