What GHS Labels Mean for Ammonia System Safety

Why Are Low-Charge Ammonia Systems Safer but Still Dependent on Strict Safety Protocols?
In refrigeration and HVAC, efficiency and safety go hand in hand. That’s why many facilities are transitioning from legacy refrigerant systems to modern, low-charge ammonia systems. These newer systems offer compact designs, increased efficiency, and lower operating costs—all while using just a fraction of the ammonia required by traditional systems.
But while low-charge systems reduce the volume of ammonia in use, they don’t eliminate the need for robust safety practices. Employers, contractors, and technicians must implement and maintain a comprehensive safety management process that includes risk assessments, GHS labels, and continuous training to stay compliant and protect workers.
Why Ammonia Safety Labeling Still Matters
Low-charge anhydrous ammonia systems are gaining popularity among manufacturers, suppliers, and end-users for their energy efficiency and operational savings. These systems use the smallest possible amount of ammonia to deliver effective cooling while reducing environmental impact and chemical risk.
Beyond cost and energy savings, another benefit of low-charge systems is improved worker safety. A reduced ammonia inventory means fewer hazards in the event of a leak or equipment failure. But reduced risk does not mean no risk. Ammonia safety labeling, emergency planning, and site-specific training remain essential for compliance and protection.
Visibility Is the First Line of Defense
Even in low-charge systems, ammonia remains a highly hazardous chemical. Visibility—through proper labeling, signage, and hazard communication—is a foundational step toward preventing accidents. Clear visual cues help technicians recognize potential danger zones, follow procedures precisely, and respond quickly in the event of an emergency. That’s why labeling systems play such a critical role in overall ammonia safety—and why GHS labels are a key part of any compliant visual communication program.
Chemical Compliance and Ammonia Hazards
Anhydrous ammonia is widely used in industrial refrigeration and HVAC systems due to its efficiency and cost-effectiveness. However, it remains a hazardous chemical that requires careful handling. Exposure to ammonia can cause severe health effects, including respiratory irritation, chemical burns, and, in extreme cases, fatalities.
Incidents involving ammonia releases can result from equipment failure, human error, or improper maintenance. For example, a worker suffered severe chemical burns at a beef processing facility in Nebraska due to an ammonia leak. The Occupational Safety and Health Administration (OSHA) issued 16 violations, including failures in lockout/tagout procedures and deficiencies in process safety documentation.
“When employers fail to properly document procedures and control highly hazardous chemicals, there is the potential for unintentional releases that can result in serious and fatal injuries,” said Jeff Funke, OSHA’s Omaha Area Director. “By implementing and sustaining workplace safety and health programs, employers can monitor their processes to ensure safeguards are in place to protect workers.”
To ensure safety and compliance, it’s essential for employees and contractors to understand ammonia's properties, associated hazards, and relevant OSHA regulations. Implementing comprehensive safety protocols and continuous training can significantly reduce risks and support chemical compliance.
Chemical Storage Signs and OSHA’s PSM Requirements
OSHA developed the Process Safety Management (PSM) standard to prevent catastrophic releases of hazardous chemicals, including ammonia. A well-executed PSM program includes hazard analysis, employee training, emergency response planning, and mechanical integrity evaluations.
Here are three key areas that support PSM compliance for facilities using low-charge ammonia:
1. Prioritize Clear Communication
Consistent, visual communication supports hazard awareness and safe behavior. Facilities can reinforce ammonia safety protocols with labels and signage that inform and instruct. For example:
-
Use GHS labels on containers to identify chemical hazards at a glance.
-
Mark ammonia storage areas with chemical storage signs to restrict unauthorized access.
-
Apply ammonia pipe marking to indicate flow direction, contents, and pressure levels.
-
Use floor marking to guide personnel and vehicles safely around refrigeration systems.
Simple, visual reminders help standardize responses across teams, especially when third-party contractors are involved.
2. Strengthen Risk Management Practices
Risk management begins with a job hazard analysis and continues with routine inspections and mitigation strategies. For ammonia systems, this includes:
-
Performing scheduled inspections on low-charge units to identify leaks, corrosion, or inefficiencies.
-
Documenting safety measures and required PPE at every workstation.
-
Maintaining a written record of identified risks and chemical tasks tied to each job role.
-
Regularly testing sensors and alarm systems for ammonia release or overpressure conditions.
- Using chemical storage signs and pipe markers to reinforce hazard awareness in shared work zones.
OSHA requires that any facility storing or using hazardous chemicals develop written procedures for safe operation. By keeping these procedures current and visible, safety managers promote accountability and preparedness.
3. Invest in Ongoing Training
Low-charge ammonia systems may reduce hazard exposure, but they still demand specialized handling and response knowledge. Annual and task-specific training keeps employees up to date on best practices and evolving risks.
-
Provide onboarding and refresher training for changes in equipment or process design.
-
Maintain a written exposure control plan and review emergency evacuation procedures.
-
Organize and label PPE stations so workers can quickly locate and don gloves, eyewear, and respiratory gear for ammonia protection.
-
Revisit lockout/tagout processes regularly, particularly when new personnel are brought on or equipment is modified.
-
Training should reinforce not only procedures but also how to interpret ammonia safety labeling in real-world situations.
-
Understanding ammonia pipe marking is especially important for maintenance teams and emergency responders.
Ammonia continues to pose significant risks in industrial settings, with incidents often resulting from equipment failure or human error. Implementing proactive training and stringent process controls is essential to prevent injuries and ensure workplace safety.
Where Labeling Breaks Down: Common Pitfalls to Avoid
Even facilities with the best intentions can fall short on safety labeling due to small oversights. Missing or damaged labels, inconsistent language, or failure to update signage after a process change can all undermine safety efforts. For low-charge ammonia systems, these small gaps may lead to confusion during routine maintenance—or worse, during an emergency.
To avoid these pitfalls, facilities should:
-
Conduct periodic audits to check for faded, peeling, or outdated labels.
-
Standardize label formats and wording to reduce ambiguity.
-
Ensure temporary signage is replaced with durable, long-term solutions.
-
Train contractors and visiting personnel to recognize and understand in-house labeling systems.
- Failing to maintain ammonia safety labeling can result in workers overlooking critical hazards during inspections or maintenance.
When labeling breaks down, so does hazard communication. Preventing these issues starts with assigning ownership and following a consistent visual communication strategy.
DuraLabel Resources for Ammonia Safety Labeling
Effective ammonia safety communication enhances operational clarity, improves compliance, and supports long-term efficiency. From chemical storage signs that warn personnel, to ammonia pipe marking that improves hazard visibility during inspections, DuraLabel offers a full suite of solutions for ammonia labeling needs.
Facility managers can design compliant GHS labels, hazard signage, and safety reminders using the free LabelForge PRO Design Software and print them instantly with one of the DuraLabel Industrial Sign and Label Systems. Whether labeling ammonia tanks or identifying PPE stations, these systems make it easy to keep messaging clear and up to date.
Need help choosing the right labeling supplies for your ammonia system? Call 1-888-897-5580 to speak with an expert to explore durable, industry-tested labeling solutions.
Want to reinforce ammonia safety? Download the free Ammonia Pipe Marking Reference Chart to see exactly how to label pipes according to regulatory standards. It’s a quick, reliable guide to building a visual communication system that supports safer maintenance, inspections, and emergency response.
Read Next:
HazCom Plans Crucial in Preventing Employee Exposure
How Premium Vinyl Labels Help Facilities Boost Safety and Compliance
Related Resources

Ammonia Accidents Threaten Worker Safety, Business Operations
Year after year, anhydrous ammonia accidents kill workers and cause severe financial penalties to businesses. ...
Read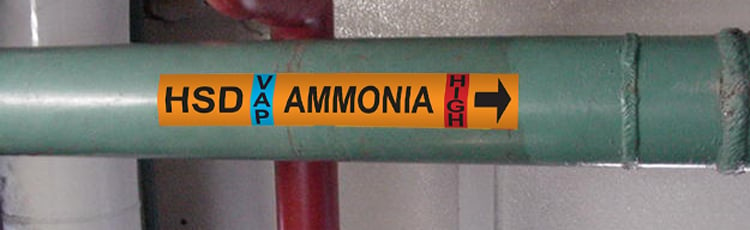
How to Meet IIAR Standards for Ammonia Pipe Marking
For safe operations and maintenance, its important employees know what's inside the pipes they're working ...
Read
Ammonia Refrigeration Safety Fundamentals: Pipe Marking and Beyond
Artificial cooling systems keep industry running, and many of these systems use anhydrous ammonia as a ...
Read