Strengthening Arc Flash Hazard Analysis with OSHA Signs
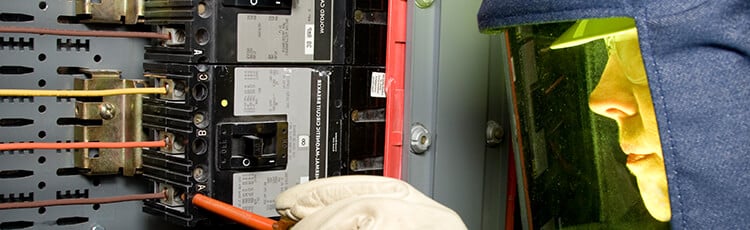
Conducting an arc flash hazard study is the cornerstone for worker safety when working with live equipment and can be improved with the implementation of OSHA signs. These signs and thousands of others can easily be printed with the DuraLabel Kodiak Max Industrial Sign and Label Print System and LabelForge Pro, our free sign and label design software.
What Comprises an Arc Flash Hazard Analysis?
The study requires electrical engineering expertise and in-depth knowledge of a facility's electrical system. The purpose of an arc flash hazard analysis is to determine the location and severity of arc flash hazards and to suggest appropriate courses of action to minimize them.
IEEE 1584 provides a formula for conducting an arc flash study. Other methods exist as well, including calculations based on the formulas presented in NFPA 70E. All of the various methods for performing an arc flash study have certain similarities. In general, an arc flash study consists of the following steps:
- Collect system data including, for example, available maximum and minimum short circuit currents from the utility, protective device time-current curves, conductor characteristics (such as length, size, and material), motor impedance, equipment grounding states, system voltages, and so forth. Data collection requires a review of existing documentation--drawings, equipment specifications, short-circuit and coordination studies--followed by collecting data by hand to fill in any gaps. The data collection process is likely to be the most time-consuming and difficult portion of an arc flash hazard study.
- Model the system After data has been assembled into an accurate and up-to-date one-line diagram, it is necessary to identify any variant modes of operation--alternative power sources, emergency or maintenance modes, effects of opening or closing ties, use of generators, shut-down of large motors, and potential hazards such as arc blasts. Each mode of operation should be analyzed to determine if it results in hazard conditions that differ significantly from normal operations.
- Determine arcing fault currents for each piece of equipment from bolted fault current data, gap size, and other data. IEEE 1584 presents formulas for determining arcing fault currents, which are often around 50% of the bolted fault current values. Although most short-circuit analyses focus on single-phase events, it is conservative to calculate three-phase values for arc fault currents.
- Determine fault-clearing times using the time-current curves of upstream protective devices. IEEE 1584 recommends calculating fault-clearing times based on both 100% and 85% of the calculated arc fault current, to account for possible fluctuations. If the arc fault current falls in the steep portion of a protective device's time-current curve, a small decrease in current can cause a significant increase in clearing time. This in turn can greatly affect incident energy. The worst-case scenario should be used for subsequent calculations.
- Calculate incident energy using either the empirical formulas presented in IEEE 1584 or the theoretical formulas of NFPA 70E. In practice, the IEEE formulas are considered more accurate, while the NFPA 70E formulas produce relatively conservative results. Actual incident energy levels depend on a range of environmental conditions such as temperature, humidity, and equipment geometry, in addition to the values used in the equations. To calculate incident energy, a working distance must be assumed. This is the distance from the arc to a worker's face or chest. 18 inches is the most commonly assumed working distance, but more precise working distances should be used when available. IEEE 1584 Table 3 presents working usual distances for various types of equipment.
- Calculate arc flash protection boundaries the distance at which incident energy is 1.2 cal/cm2. This is the energy needed to cause second-degree burns. NFPA 70E provides three acceptable methods for determining these boundaries:
- Using NFPA 70E tables 220.2(B)(2) and 220.6(B)(9)
- Using the formulas in NFPA 70E Annex B
- Using the formulas in IEEE 1584
The data collected and calculated in the course of the study is put to various uses, including printing warning labels for equipment that meet OSHA label requirements, determining required PPE, and training workers. Data may also be analyzed to optimize the system itself by modifying or replacing protective devices or making other changes to the system architecture.
Performing an arc flash study by hand is a forbidding task. However, arc flash software is commercially available to greatly decrease the work required and to allow easy integration of arc flash information with other aspects of a facility's electrical safety program. Whether you perform the study by hand, or with a program, it is important that it meets OSHA electrical panel labeling requirements when being made.
Free Guide to Arc Flash Hazards
DuraLabel's free Arc Flash Labeling Quick Start Guide provides the necessary details needed to train workers on hazards, along with some OSHA arc flash labeling requirements, and more. Looking for additional information? Give us a call at 1-888-965-3359 and one of our safety experts will guide you through the process.
Want to learn more about arc flash PPE? DuraLabel's free Arc Flash PPE Quick Reference Chart is an essential resource for workers who work in areas with energized equipment. The chart also explains the four arc flash categories and lists minimum arc rating.
Read Next:
Preventing Arc Flash Incidents with Proper Labeling and Communication
Related Resources
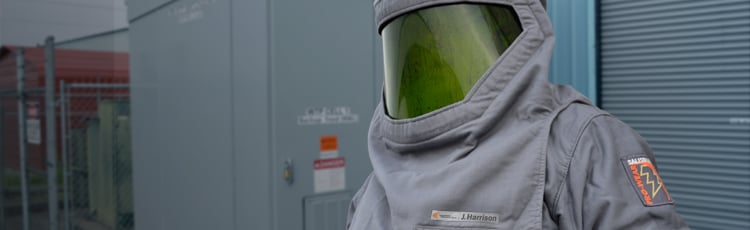
Arc Flash PPE
Personal Protective Equipment (PPE) is the last line of defense against injuries. When it comes to arc flash, ...
Read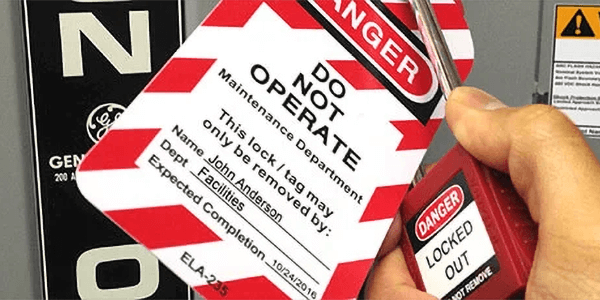
How to Prevent Arc Flash with Lockout Tagout Signs and Safety Labels
What Are the First Steps to Preventing Arc Flash in the Workplace? In the realm of electrical safety, the ...
Read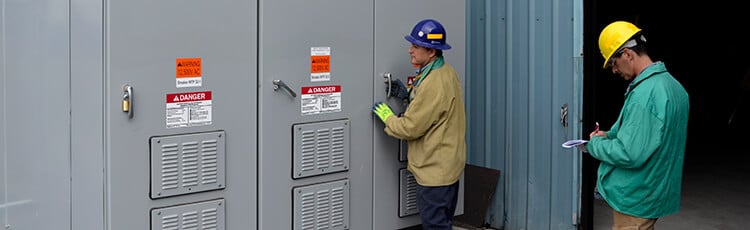
Understanding Arc Flash: The Shocking Truth About Electrical Injuries
Electrical workers consider shocks as part of their job and normal, according to a study. However, it could ...
Read