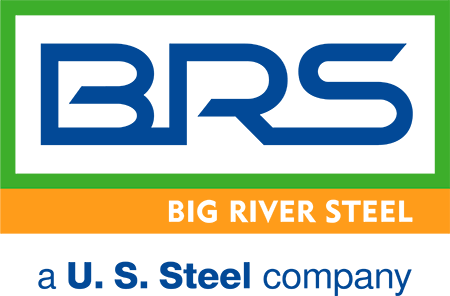
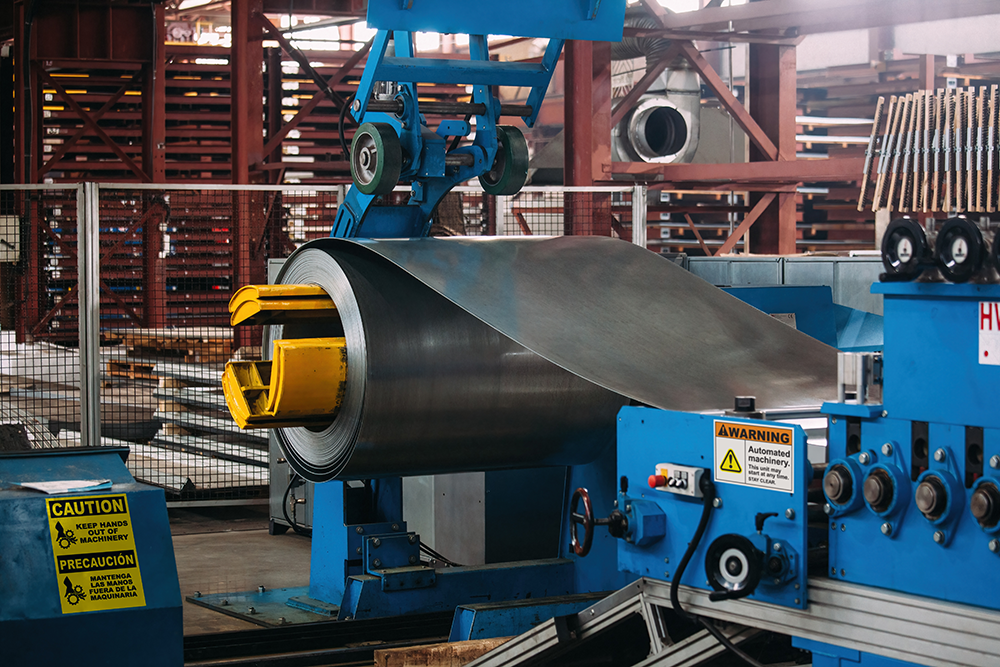
Industry
Manufacturing
Challenge
Big River Steel's outdated labeling system was slow, inconsistent, and error-prone, particularly for critical tasks like lockout/tagout. As the facility expanded, the system couldn't keep up with increasing labeling demands.
Results
The DuraLabel system improved labeling accuracy, boosted safety, and saved time with batch printing. Big River Steel now operates more efficiently while presenting a professional image.
“Being able to provide [the Toro Max’s streamlined labeling process] to my technicians helps their job and makes me a logistics hero.”
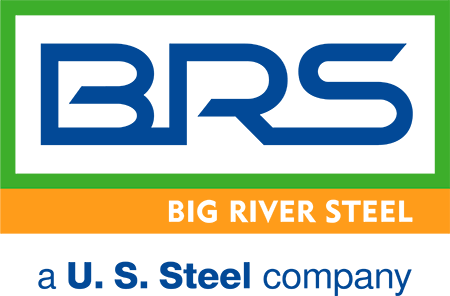
Michael Lysell
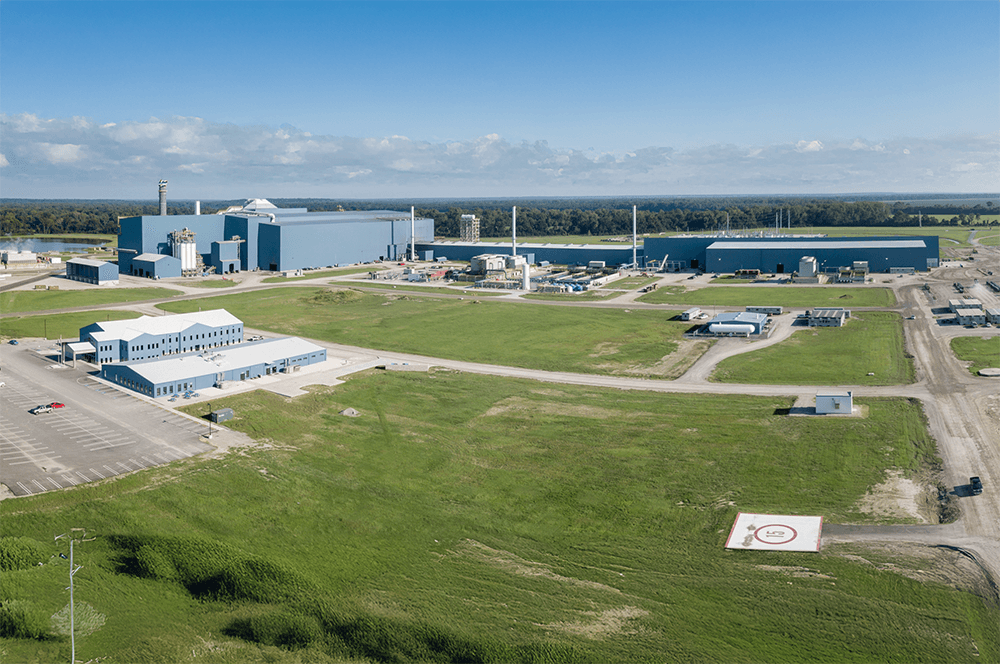
Big River Steel, a major contributor in the steel manufacturing industry, owns one of North America’s newest and greenest steel plants. With an impressive annual capacity of 1.5 million tons, the facility sets the standard in both output and environmental sustainability. To maintain smooth operations, the plant relies on accurate and reliable labeling across its equipment and systems. That’s where DuraLabel comes in—working closely with Big River Steel’s Maintenance/Reliability Planner, Michael Lysell, to provide high-quality labeling solutions that enhance safety and efficiency.
The Challenge
Big River Steel’s operations depend heavily on clear, consistent labeling for a range of applications, including equipment naming, piping identification, and lockout/tagout (LOTO) safety protocols. Prior to partnering with DuraLabel, the team struggled with outdated label-making systems. These older systems featured small, clumsy keyboards and offered limited formatting capabilities. “We were using older style labels with small keyboards and limited format,” Lysell explained.
This setup significantly slowed down their labeling process, especially as the company was expanding and constructing a new production line. Labeling tasks became time-consuming and error-prone, particularly when they had to input each label manually. Consistency was difficult to maintain, especially for applications like LOTO, where mistakes could lead to serious safety hazards. As Big River Steel grew, it became clear that their old system could not keep up with the increasing demand for labels across the facility.
The Solution
To solve these challenges, Big River Steel adopted DuraLabel’s Toro Max printers. This upgrade transformed their labeling process by introducing automation and precision. The Toro Max printers allowed the team to automate much of their labeling process, including the ability to batch print labels from pre-loaded spreadsheets. This functionality saved the team countless hours of manual data entry. Lysell highlighted the significant improvement, saying, “Being able to load a spreadsheet and push go, and have hundreds of labels print out automatically, is an incalculable labor savings over having to hand-enter each label.”
The flexibility of the DuraLabel printers also played a crucial role in their success. The team was able to create labels with greater precision and consistency, whether they were marking equipment, identifying piping systems, or ensuring safety compliance with LOTO procedures. The printers ran non-stop during the construction of the new production line to tackle the increased demand without issue. What would have been an overwhelming task using the older systems became streamlined and efficient with the Toro Max printers. The ease of use also meant that multiple team members could operate the system without extensive training, further enhancing productivity. specific features unique to your product that made their success possible. If available, include at least one quote from your customer in this section for their point of view.
“Being able to load a spreadsheet... and have hundreds of labels print out automatically, is an incalculable labor savings..."
The Results
Since implementing the DuraLabel system, Big River Steel has experienced improvements for their plant. Lysell explained, “Greater legibility and accuracy of labeling contributes significantly to greater reliability and safety.” These improvements have directly contributed to fewer safety incidents and improved regulatory compliance.
From an operational standpoint, the ability to batch print labels has saved the company a significant amount of time and labor. Lysell mentioned how this new efficiency has freed up the team to focus on more critical tasks rather than spending hours manually creating labels. “Being able to provide this to my technicians helps their job and makes me a logistics hero,” Lysell said. The streamlined labeling process has also given the plant a more professional look, enhancing its overall image.