From Flash to Ash: Understanding Arc Flash Hazards and Prevention

What is Arc Flash?
When it comes to electrical safety, arc flash is one of the most dangerous—and most ignored—hazards. Arc flash is a powerful electrical event that occurs when an electric current strays from its intended path and travels through the air between conductors. This sudden release of energy creates an intense flash of light and heat. It is often followed with a loud noise and dangerous debris. It can cause severe injuries, permanent damage, and even fatalities in seconds. Yet, many facilities and workers still fail to take it seriously.
In 2022, the U.S. Bureau of Labor Statistics (BLS) reported 145 deaths from electrical exposure, with 81 of those being direct exposure. The good news: these tragedies are preventable by following proper arc flash safety guidelines and implementing protective measures.
Causes of Arc Flash
An arc flash incident can be triggered by numerous factors, including:
- Equipment failure
- Accidental contact with electrical conductors
- Improper maintenance
- Dust or corrosion on electrical components
- Improper installation of parts
When any of these conditions happen, the protective barriers meant to hold back the electricity can fail, leading to an arc flash event.
The Importance of Arc Flash Safety
An arc flash hazard poses serious risks to both people and property. The intense heat created during an arc flash can cause severe burns, while the explosive force can result in severe injuries and even death. The high temperatures and pressure created by an arc flash incident can damage equipment. This leads to costly repairs and downtime. Understanding and implementing arc flash safety measures is crucial for protecting workers and maintaining a safe working environment.
In this guide, we will explore more about arc flashes, and what facilities can do to reduce the risks, while ensuring the safety of all those working with or near electrical equipment.
Understanding the Role of NFPA in Arc Flash Safety
The National Fire Protection Association (NFPA) plays a crucial role in establishing standards and regulations aimed at verifying safety in various industries, including electrical work. Specifically, NFPA 70E provides guidelines for protecting workers from electrical hazards like an arc flash incident.
This standard outlines:
- Safety procedures
- Training requirements
- Protective measures
Everything that the NFPA 70E standard goes over is to reduce the risks that come with arc flash events.
Compliance with NFPA 70E is essential for employers and employees working with or near electrical equipment. Organizations can create a safer work environment, reduce the likelihood of an arc flash, and minimize the severity of injuries in the event of an accident by following these standards.
NFPA 70E is often referenced by regulatory agencies such as the Occupational Safety and Health Administration (OSHA) in developing safety regulations. Familiarity with NFPA standards is necessary for following regulations and ensuring legal and regulatory compliance.
Implementing NFPA 70E Standards for Arc Flash Safety
There are countless strategies facilities can use to be aligned with NFPA 70E for arc flash safety.
Conduct arc flash risk assessments: Conduct a detailed arc flash risk assessment in all areas where electrical work is performed. Identify potential hazards, assess the likelihood of arc flash incidents, and determine the severity of consequences. This assessment forms the foundation for developing appropriate safety measures.
Establish safe work practices: Train employees on safe work practices outlined in NFPA 70E. This includes proper electrical equipment operation, lockout/tagout (LOTO) procedures, and the use of personal protective equipment (PPE). Emphasize the importance of following established safety protocols to mitigate arc flash risks.
Implement engineering controls: Utilize engineering controls, such as equipment labeling, insulation upgrades, and equipment maintenance to reduce the likelihood of an arc flash accident. Ensure that all electrical equipment is properly installed, maintained, and inspected to minimize the risk of failures that could lead to an arc flash incident.
Provide personal protective equipment: Equip workers with appropriate arc flash PPE, including:
- Arc-rated clothing
- Face shields
- Insulated gloves
This equipment is to protect against an arc flash hazard. Make sure that arc flash PPE is properly fitted, regularly inspected, and replaced as needed to maintain effectiveness.
Develop emergency response plans: Create thorough emergency response plans that outline procedures for how to respond to arc flashes, including:
- Evacuation routes
- Emergency shutdown protocol
- Medical response procedure
Conduct regular drills and training exercises to confirm all employees are prepared to respond effectively in an arc flash emergency.
Give regular training and education: Provide ongoing training and education on NFPA 70E arc flash standards, arc flash risks, and safety procedures to all employees involved in electrical work. Encourage active participation in safety programs and promote a culture of continuous improvement and accountability.
Organizations can significantly enhance arc flash safety in the workplace, protect employees from harm, and promote a culture of electrical safety awareness and compliance by carrying out these strategies and complying with NFPA 70E arc flash standards.
Labeling the Arc Flash with the NFPA 70E Standard
Arc flash labels are crucial for safety in places with electrical hazards. It’s important to be informed about labeling requirements, safety signs, why clear labels matter, and labeling standards.
The NFPA sets rules for arc flash labels with the NFPA 70E standard. These rules make sure that labels are consistent and easy to read no matter where you are. It provides guidelines for things like what information should be on the label, the colors to use, and where to place them. Following these standards helps create a safe visual communication factory.
Arc Flash Sign and Label Requirements
The arc flash risk assessment will determine the information needed on arc flash labels, such as the arc flash boundary and the kind of arc flash PPE required to work within that boundary.
Each arc flash label is required to display this information:
- Nominal system voltage—The nominal system voltage gauges the equipment's power level.
- Arc flash boundary—The arc flash boundary was created to share the safest distance a person could be to prevent severe injury.
- At least one of the following to indicate PPE requirements:
- Incident energy and working distance, or arc flash PPE category, but not both
- Minimum arc rating of clothing
- Site-specific description of PPE required
It's important to avoid labeling a piece of equipment with both a calculated incident energy and an arc flash PPE category, because these two pieces of information come from different methods of evaluating arc flash danger. If both forms of information are present on the label, it could cause confusion or conflicting safety recommendations.
Arc flash labels usually include more than just the information listed above. Some information may have shock protection info, like a restricted and limited approach boundary, or show the date of when the last risk assessment was conducted.
In addition to the information provided on the label, effective arc flash labels often adhere to a standardized format outlined in the ANSI Z535 standard. This approach uses eye-catching colored headers and signal words to get noticed and quickly convey messages.
Labeling Electrical Equipment
Electrical gear, like panels and switches, must have warning labels for arc flash risks. These labels show things like how dangerous the flash can be and what protective gear to wear. For example, if there's an elevated risk of a powerful arc flash, the label should include what protective clothing workers need to wear to be in that area. Following these rules helps workers know the risks and stay protected while working with electricity.
Why Clear Labels Matter
It's crucial that labels are easy to understand. Confusing labels can lead to accidents because workers might not know safety protocols. Understandable labels make it clear what the risks are and what precautions to take. For example, a label might say, "Danger: Arc Flash Hazard - Wear Arc Flash Clothing and Face Protection." This tells workers exactly what they need to do to protect themselves. Workers can quickly understand the dangers and take the necessary precautions to stay safe when the labels are clear.
In 2020, the Electrical Safety Foundation shared that there were 2,220 non-fatal electrical injuries. This was a 17% increase from 2019. Properly labeling equipment and areas where an arc flash incident may occur can make a huge difference in reducing the amount of electrical hazard injuries and fatalities.
OSHA Arc Flash Compliance: Key Safety Requirements
Compliance with OSHA regulations is essential for maintaining a safe work environment and protecting employees from an arc flash accident. OSHA provides specific guidelines and regulations for electrical safety, including measures to prevent arc flash.
General duty clause: OSHA's General Duty Clause, Section 5(a)(1) of the Occupational and Health Act, requires employers to provide a workplace free from dangers—such as arc flash hazards—that are likely to cause death or serious physical harm. This enforces employers to identify and mitigate potential risks associated with electrical work.
Signage and labeling electrical safety standards: OSHA's electrical safety standards for signage and labeling, outlined in 29 CFR 1910.303, states that electrical equipment must be marked with warning signs, labels, or other means to warn employees of potential electrical hazards. According to OSHA 29 CFR 1910.335, workers must also be warned if they are working near electrical hazards.
NFPA 70E incorporation: OSHA often uses NFPA 70E as a widely accepted standard for electrical safety compliance in the industry. While NFPA 70E itself is not an OSHA regulation, OSHA uses it to determine if employers are following electrical safety guidelines.
Training requirements: OSHA mandates that employers provide training to employees who may be exposed to electrical hazards.
Training should cover topics such as:
- Electrical safety procedures
- Hazard recognition
- Use of arc flash PPE
- Emergency response protocols
Employers must ensure that employees are properly trained to perform their jobs safely and are aware of the risks related to an arc flash hazard.
Recordkeeping and documentation: OSHA requires employers to maintain records of electrical safety training, hazard assessments, and incident investigations related to arc flash hazards. Employers must keep a record of the steps they have taken to fix any hazards and make sure they are following OSHA rules.
Employers can create a safer work environment, reduce the risk of an arc flash incident, and protect employees from serious injuries or fatalities associated with electrical hazards by observing OSHA regulations and incorporating best practices for arc flash safety. Regular audits, training programs, and hazard assessments are essential components of OSHA compliance efforts aimed at promoting arc flash safety in the workplace.
How to Prevent an Arc Flash
As great as labels and procedures are, there still may be instances where an arc flash accident occurs. What can a warehouse do to decrease the chance of that arc flash hazard happening? There are plenty of methods to prevent them, including:
- Engineering controls
- Lockout tagout procedures
- Administrative controls
- Personal protective equipment requirements
Making Equipment Safer from Arc Flashes
Engineering controls are ways to make equipment safer and reduce the chances of an arc flash incident. This might mean using special equipment that can handle arc flashes safely or regularly checking equipment to catch problems early.
Some special equipment that can safely handle arc flashes includes:
- Arc-resistant switchgear
- Circuit breakers with arc fault protection
- Arc-resistant motor control centers
These types of equipment are designed to contain and redirect arc energy safely which reduces the likelihood of injury or damage should an arc flash incident arise.
Companies can lower the risk of arc flashes by providing the right equipment for workers who may be at risk from exposure to electricity.
Lockout Tagout Procedures
LOTO procedures are in place for stopping electrical equipment from turning on accidentally during maintenance. Before starting any work on electrical equipment, workers must follow LOTO steps to ensure arc flash safety:
- Inform all impacted employees that the equipment will be locked out
- Identify all sources of electrical power to the equipment
- Shut down the equipment
- Disconnect the equipment from its energy sources
- Relieve any stored energy by grounding, attempting to start the equipment, or other methods
- Attach lockout/tagout devices to energy-isolating points
- Use a testing tool to confirm the equipment is de-energized
- When needed, install a grounding device to remove the risk of induced or stored voltage
Following the LOTO process helps prevent arc flashes caused by equipment turning on unexpectedly.
Administrative Controls for Arc Flash Safety
Administrative controls include rules, procedures, and training to protect workers from an arc flash accident. This might mean:
- Teaching workers how to do their jobs safely
- Holding regular safety meetings
- Planning for emergencies
Facilities can prevent accidents and protect workers with clear rules and arc flash knowledge.
Personal Protective Equipment Requirements
Employers must make sure workers know how to choose and use arc flash PPE correctly and provide enough gear for everyone who needs it. By wearing the right PPE, workers can reduce their chances of getting hurt in an arc flash hazard.
Companies can prevent arc flashes and make workplaces safer for everyone by using engineering controls, following LOTO procedures, implementing administrative controls, and providing arc flash PPE.
Training and Education to Keep Workers Safe
Training and education are essential components of arc flash prevention. Workers need to understand the risks associated with arc flashes and know how to work safely around electrical equipment. Training programs should cover topics, such as:
- Hazard recognition
- Safe work practices
- Emergency response procedures
- Proper use of protective equipment
Never underestimate the influence training can have on workers. With impactful training, workers will be better skilled to work in electrically dangerous environments.
Know Your Arc Flashes
Arc flashes can happen in unusual ways and each incident can be dangerous. There are four types of arc flashes that can occur in any facility:
- Open-air arc flash
- Arc-in-a-box
- Ejected arc
- Tracking arc
Open-Air Arc Flash
The open-air arc flash is the most well-known and studied type of arc flash hazard. It happens when electricity arcs through the air between exposed wires or equipment. Things like equipment malfunctions, poor maintenance, or making mistakes can cause these flashes, which are a common danger in industrial areas.
Arc-in-a-box
Arc-in-a-box is a type of arc flash test mainly used in the European Union (EU). Here, the arc is kept inside a controlled space, letting scientists observe its actions under certain conditions. Although this method is not utilized much outside of labs, it provides valuable information about arc flashes. This helps us make safety rules and guidelines.
Ejected Arc
An ejected arc happens when the hot plasma from an arc forcefully shoots out and contacts a worker. This type of arc flash hazard is dangerous because the fast-moving plasma can cause serious burns and injuries when it connects. Even though it's not usually thought about in regular safety rules and calculations, ejected arcs are a real danger, especially when dealing with high voltages (like 480V and up). In these cases, a simple arc flash incident can turn into an ejected arc fast.
Tracking Arc
Tracking arcs occur when the plasma from an arc travels along a worker's skin or through their clothes. This type of arc flash is more likely to occur with higher voltages and when there's contact with electricity, putting workers in danger. While tracking arcs are most common in places with extremely high voltages, they remind us why it's important to wear proper arc flash PPE and follow safety protocols, even when things seem safe.
Keep in mind that all arc flashes are dangerous and can cause serious injuries and damage. Be cautious when working with or around an electrical environment.
Common Locations for Arc Flash 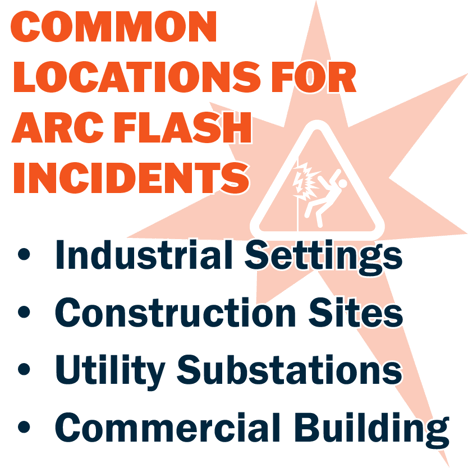
Arc flashes can happen in various settings and each area presents its own risks and challenges. There are four common locations where an arc flash may take place:
Industrial Settings
Industrial settings, such as manufacturing plants and factories, are prime locations for an arc flash incident due to the presence of heavy machinery and electrical equipment. Factors such as equipment maintenance, inadequate training, and improper use of tools can increase the risk of arc flashes in industrial environments.
Construction Sites
Construction sites are active environments where workers are often exposed to electrical hazards. Activities such as electrical installations, wiring, and equipment maintenance create a significant risk of arc flashes. Components such as temporary power sources, incomplete wiring, and improper grounding can contribute to an arc flash incident on construction sites.
Utility Substations
Utility substations are critical facilities that distribute electricity to homes, businesses, and industries. These facilities contain high-voltage equipment and pose inherent risks of arc flashes. Factors such as equipment malfunction, inadequate maintenance, and human error can lead to an arc flash hazard in utility substations. Workers in these facilities must follow strict safety protocols and wear appropriate arc flash PPE to mitigate the risks linked to arc flashes.
Commercial Buildings
Commercial buildings, including offices, retail stores, and healthcare facilities, present potential risks of arc flashes. Common commercial equipment can be sources of an arc flash accident such as:
- Panelboards
- Switchgear
- Transformers
Overloading circuits, improper installation, and lack of maintenance can contribute to an arc flash hazard in these settings. Employers must prioritize electrical safety and implement preventive measures to protect occupants and property from arc flash incidents.
Facilities can reduce the risk of accidents and create safer environments for workers and the public once they understand where arc flashes happen and implement appropriate safety measures.
DuraLabel Solutions to Reduce Arc Flash
It’s clear that arc flashes are serious hazards that can harm workers and damage property. Understanding the importance of arc flashes, using preventive measures, and creating a safety-focused workplace are all key contributors to ensure facilities are doing all they can to avoid arc flash incidents.
Facilities can ensure the safety of their workers with proper arc flash labels and signs. The DuraLabel Kodiak Max Industrial Sign and Label System can easily handle all your signage needs to guarantee OSHA compliance and a well-protected environment.
Get help crafting a system that will provide the safe communication you need. Call 1-888-902-2148 and one of our experts will guide you through the process.
Conduct an arc flash risk assessment and create custom labels with guidance from DuraLabel’s free Arc Flash Labeling Quick Start Guide. This guide helps evaluate your facility’s electrical safety and ensures all arc flash labels are up to date.
Read Next:
Keep Job Sites Safe: How Custom Labels Change the Game for Contractors
Printing Electrical Safety Signs with a Thermal Transfer Printer
Related Resources
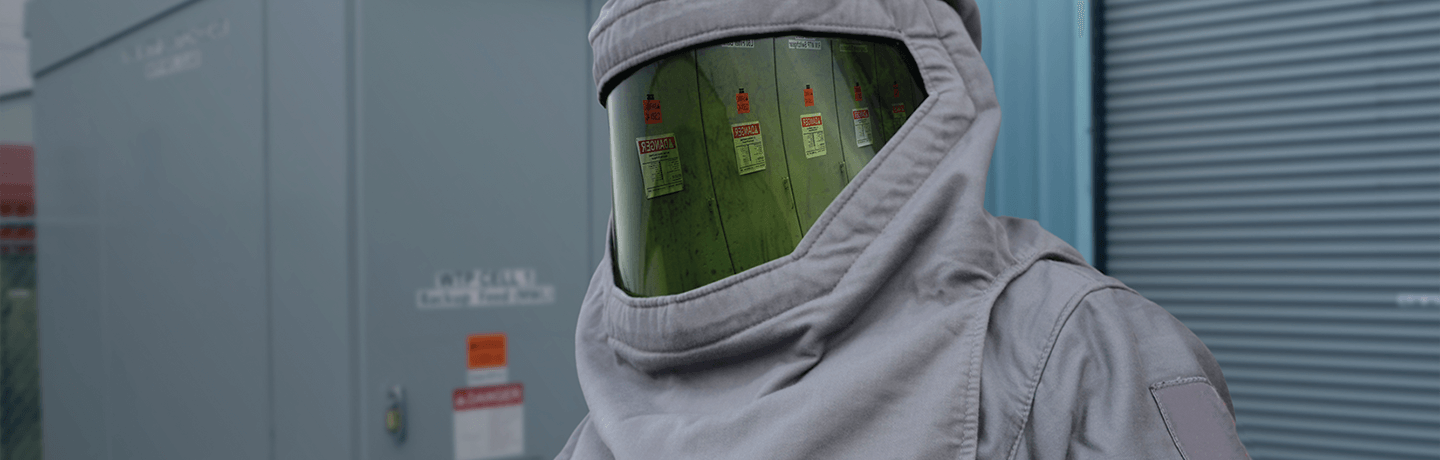
NFPA 70E Arc Flash with OSHA Signs
What is NFPA 70E? NFPA 70E, or the NFPA's Standard for Electrical Safety in the Workplace, outlines specific ...
Read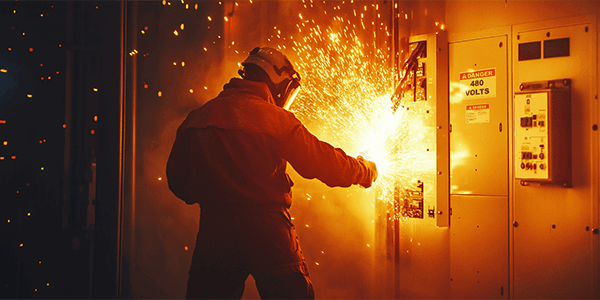
Arc Flash Labeling Essentials for Industrial Facilities & Field Teams
What Makes Arc Flash Labeling Essential for Electrical Safety? A loud explosion. A sudden flash of blinding ...
Read
How to Improve Arc Flash Safety in Mining Operations
Mining operations depend heavily on electrically powered equipment—including drills, shovels, conveyors, and ...
Read